A CHEVROLET Produced Every 10 Minutes
Page 61
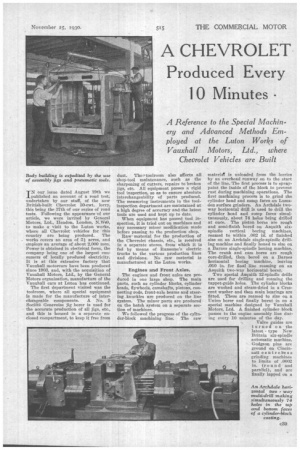
Page 62
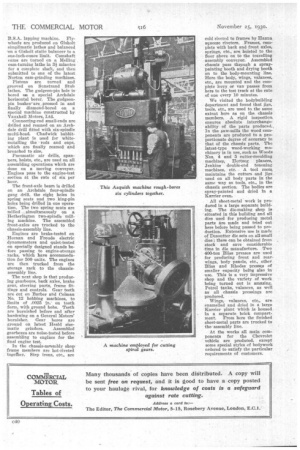
If you've noticed an error in this article please click here to report it so we can fix it.
A Reference to the Special Machinery and Advanced Methods Employed at the Luton Works of Vauxhall Motors, Ltd., where Chevrolet Vehicles are Built
IN our issue dated August 19th we published an account of a road test, undertaken by our staff, of the new British-built Chevrolet 20-cwt. lorry, this being the 27th of our series of road tests. Following the appearance of our article, we were invited by General Motors, Ltd., Hendon, London, N.W40, to make avisit to the Luton works, where all Chevrolet vehicles for this country are being produced. The works covers an area of 7i acres, and employs an average of about 2,000 men. Power is obtained in electrical form, the company being one of the largest consumers of locally produced electricity. It is at this extensive factory that Vauxhall motorcars have been produced since 1903, and, with the acquisition of Vauxhall Motors, Ltd., by the General Motors organization, manufacture of the Vauxhall cars at Duton has continued.
The first department visited was the toolroom, where all special equipment is made for the manufacture of interchangeable components. A No. 5 Societe Genevoise jig borer is used for the accurate production of all jigs, etc., and this is housed in a separate enclosed compartment, to keep it free from
dust. Thei,toolroorn also affects all shop-tool maintenance, such as the sharpening of cutters, repairs to broken jigs, etc. All equipment passes a rigid tool inspection, so as to ensure absolute interchangeability of parts produced. The measuring instruments in the toolinspection department are maintained at a high degree of accuracy and the latest tools are used and kept up to date.
When equipment has passed tool inspection, it is tried out on machines and any necessary minor modification made before passing to the production shop.
Raw-material for the production of the Chevrolet chassis, etc., is received in a separate stores, from which it is fed by means of Ransome's electric trucks to the various production lines and divisions. No raw material is manufactured at the Luton works.
Engines and Front Axles.
The engines and front axles are produced in one large shop. The main parts, such as cylinder blocks, cylinder heads, flywheels, camshafts, pistons, connecting rods, front-axle beams and steering knuckles are produced On the line system. The minor parts are produced on the batch system on a separate section of machines.
We followed the progress of the cylinder-block machining line. The raw materie is unloaded from the lorries by an overhead runway on to the start of the line. The first process is to spraypaint the inside of the block to prevent rust during machining operations. The first machining process is to grind the cylinder head and sump faces on Lumsden surface grinders. An Archdale twoway horizontal drill is used to drill the cylinder head and sump faces simultaneously, about 74 holes being drilled at once. The piston bores are rough and semi-finish bored on Asquith sixspindle vertical boring machines, reamed to within .002 id. of finished size on an Archdale single-spindle drilling machine and finally honed to size on a Barnes single-spindle honing machine. The crank and etun bores are rough core-drilled, then bored on a Barnes horizontal boring machine, leaving .010 in. for final line reaming on an Asquith two-way horizontal borer.
Two special Asquith 12-spindle drills are used for drilling and reaming the tappet-guide holes. The cylinder blocks are washed and steam-dried in a Crascent washer and then main bearings are fitted. These are reamed to size on a Union borer and finally burnt in on a special machine designed by Vauxhall Motors, Ltd. A finished cylinder block passes to the engine assembly line during every 10 minutes of the day.
Valve guides are turned on the latest type New Britain six-spindle automatic machine. Gudgeon pins are ground on Cincinnati centre ke s s grinding machines to limits of .0002 in. (r ound and parallel), and are finally lapped du a
B.S.A. lapping machine. Flywheels are produced on Gisholt simplimatic lathes and balanced 'on a Gisholt static balancer to a one-inch-ounce limit. Camshaft cams are turned on a Melling cam-turning lathe in n minutes for a complete shaft, and then submitted to one of the latest Norton cam-grinding machines.
Pistons are turned and grooved on Sunstrand Stub lathes. The gudgeon-pin bole is bored an a special Archdale horizontal borer. The gudgeonpin bushes'are pressed in and finally diamond-bored on a special machine constructed by Vauxhall Motors, Ltd.
Connecting-rod small-ends are drilled and reamed on an Archdale drill fitted with six-spindle multi-head. Chadwick babbiting plant is used for whitemetalling the rods and caps, which are finally reamed and broached to size.
Pneumatic air drills, spanners, hoists, etc., are used on all assembling operations which are done on a moving conveyor. Engines pass to the engine-test . section at the rate of six per him r.
The front-axle beam is drilled on an Archdale four-spindle gang drill, the eight holes in spring seats and two king-pin holes being drilled in one operation. The two 'spring seats are milled simultaneously on a Hetherington two-spindle milling machine. The assembled front-axles are trucked to the chassis-assembly line.
Engines are brake-tested on Heenan and Froude electric dynamometers and quiet-tested on specially designed stands he-fore passing to engine-storage racks, which have accommodation for 500 units. The engines are then trucked from the storage rack to the ehassisassembly line.
The next shop is that producing gearboxes, back axles, brake gear, steering parts, frame fittings and controls. Gear teeth are cut on Barber and Colman No. 12 hobbing machines, to limits of .0025 011 tooth form, with ground hobs. Teeth are burnished before and after hardening on a General Motors' burnisher. Gear bores are ground on latest Heald sizematte grinders. Assembled gearboxes are noise-tested before assembling to engines for the final engine test.
In the chassis-assembly shop frame members are hot-riveted together. Step irons, etc., are cold riveted to frames by Hanna squeeze riveters. Frames, complete with back and front axles, springs, etc., are hoisted to the floor above on to the travelling assembly conveyor. Assembled chassis pass through a spraypainting booth and drying booth on to the body-mounting line. Here the body, wings, valances, etc., are mounted and the complete lorry Or van passes from here to the test track at the rate of one every 10 minutes.
We visited the bodybuilding department and found that jigs, tools, etc., are used to the same extent here as on the chassis members. A rigid inspection, ensures absolute interchangeability of the parts produced., In the saw-mills the wood components arc produced to a proportionate degree of accuracy to that of the chassis parts. The latest-type wood-working machinery is in use, such as Woods Nos. 4 and 5 cutter-moulding machines, Hertzog planers, Jenkins double-end tenoning machines, etc. A tool room, maintains the cutters and jigs used on all body parts in the same way as tools, etc., in the chassis section. The bodies are spray-painted and dried in a Karrier oven.
All sheet-metal work is produced in a large separate building. The die-making shop is situated in this building and all dies used for producing metal parts are made and tried out here before being passed to production. Extensive use is made of Desoutter die sets on all small dies ; these can be obtained from stock and save considerable time in die manufacture. Two 400-ton Bliss presses are used for producing front and rear, wings, body panels, etc., other Bliss and Rhodes presses of smaller capacity being also in use. This is a very impressive shop and the variety of work being turned out is amazing. Petrol tanks, valances, as well as all chassis pressings are produced.
Wings, valances, etc., are enamelled and dried in a large Earner plant which is housedin a separate brick compartment. From here the finished sheet-metal parts are trucked to the•asserebly line.
At the works all main components for the Chevrolet vehicle are produced, except some special styles of bodywork ordered to satisfy the particular requirements of customers.