SCREEN SAVERS!
Page 48
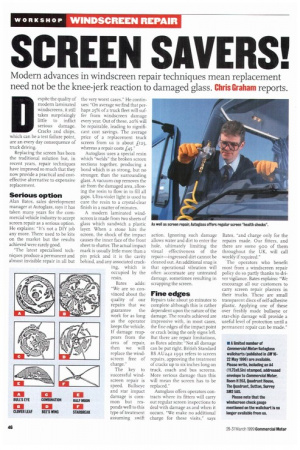
If you've noticed an error in this article please click here to report it so we can fix it.
Modern advances in windscreen repair techniques mean replacement need not be the knee-jerk reaction to damaged glass. Chris Graham reports.
Despite the quality of modern laminated windscreens, it still takes surprisingly little to inflict serious damage. Cracks and chips, which can be a test failure point, are an every day consequence of truck driving.
Replacing the screen has been the traditional solution but, in recent years, repair techniques have improved so much that they now provide a practical and costeffective alternative to expensive replacement.
Serious option
Alan Bates, sales development manager at Autoglass, says it has taken many years for the commercial vehide industry to accept screen repair as a serious option. He explains: "It's not a DIY job any more. There used to be kits on the market but the results achieved were rarely good.
"The latest specialised techniques produce a permanent and almost invisible repair in all but the very worst cases." He continues: "On average we find that perhaps 25% of a truck fleet will suffer from windscreen damage every year. Out of these, 20% will be repairable, leading to significant cost savings. The average price of a replacement truck screen from us is about £125, whereas a repair costs £45."
Autoglass uses a special resin which "welds" the broken screen sections together, producing a bond which is as strong, but no stronger, than the surrounding glass. A vacuum cup removes the air from the damaged area, allowing the resin to flow in to fill all gaps. Ultra-violet light is used to cure the resin to a crystal-clear finish in a matter of minutes.
A modem laminated windscreen is made from two sheets of Bates adds: "We are so convinced about the quality of our repairs that we guarantee the work for as long as the operator keeps the vehicle. If damage reappears from the area of repair, then we will replace the windscreen free of charge."
The key to successful windscreen repair is speed. Bullseye and star impact damage is common but responds well to this type of treatment assuming swift
action. Ignoring such damage allows water and dirt to enter the hole, ultimately limiting the visual effectiveness of the repair—ingressed dirt cannot be cleaned out. An additional snag is that operational vibration will often accentuate any untreated damage, sometimes resulting in scrapping the screen.
Fine edges
Repairs take about 30 minutes to complete although this is rather dependent upon the nature of the damage. The results achieved are impressive with, in most cases, the fine edges of the impact point or crack being the only signs left. But there are repair limitations, as Bates admits: "Not all damage can be put right. British Standard BS AU242 1991 refers to screen repairs, approving the treatment of cracks up to six inches long on truck, coach and bus screens. More serious damage than this will mean the screen has to be replaced."
Autoglass offers operators contracts where its fitters will carry out regular screen inspections to deal with damage as and when it occurs. "We make no additional charge for these visits," says Bates, "and charge only for the repairs made. Our fitters, and there are some 900 of them throughout the UK, will call weekly if required."
The operators who benefit most from a windscreen repair policy do so partly thanks to driver vigilance. Bates explains: "We encourage all our customers to carry screen repair plasters in their trucks. These are small transparent discs of self-adhesive plastic. Applying one of these over freshly made bullseye or star-chip damage will provide a useful level of protection until a permanent repair can be made."