Give your gasket a seal of approval
Page 120
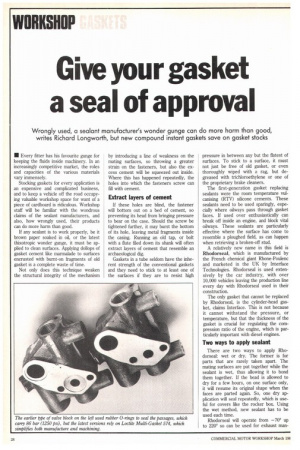
Page 121

Page 122
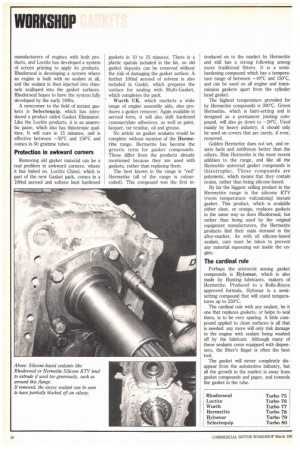
If you've noticed an error in this article please click here to report it so we can fix it.
Wrongly used, a sealant manufacturer's wonder gunge can do more harm than good, writes Richard Longworth, but new compound instant gaskets save on gasket stocks
• Every fitter has his favourite gunge for keeping the fluids inside machinery. In an increasingly competitive market, the roles and capacities of the various materials vary immensely.
Stocking gaskets for every application is an expensive and complicated business, and to keep a vehicle off the road occupying valuable workshop space for want of a piece of cardboard is ridiculous. Workshop staff will be familiar with the wondrous claims of the sealant manufacturers, and also, how wrongly used, their products can do more harm than good.
If any sealant is to work properly, be it brown paper soaked in oil, or the latest thixotropic wonder gunge, it must be applied to clean surfaces. Applying dollops of gasket cement like marmalade to surfaces encrusted with burnt-on fragments of old gasket is a complete waste of time.
Not only does this technique weaken the structural integrity of the mechanism by introducing a line of weakness on the mating surfaces, so throwing a greater strain on the fasteners, but also the excess cement will be squeezed out inside. Where this has happened repeatedly, the holes into which the fasteners screw can fill with cement.
Extract layers of cement
If these holes are blind, the fastener will bottom out on a bed of cement, so preventing its head from bringing pressure to bear on the case. Should the screw be tightened further, it may burst the bottom of its hole, leaving metal fragments inside the casing. Running an old tap, or bolt with a flute filed down its shank will often extract layers of cement that resemble an archaeological dig.
Gaskets in a tube seldom have the inherent strength of the conventional gaskets and they need to stick to at least one of the surfaces if they are to resist high pressure in between any but the flatest of surfaces. To stick to a surface, it must not just be free of old gasket, or even thoroughly wiped with a rag, but degreased with trichloroethylene or one of the proprietary brake cleaners.
The first-generation gasket replacing sealants were the room temperature vulcanising (R'FV) silicone cements. These sealants need to be used sparingly, especially where oilways pass through gasket faces. If used over enthusiastically can break off inside an engine, and block vital oilways. These sealants are particularly effective where the surface has come to resemble a ploughed field, as can happen when retrieving a broken-off stud.
A relatively new name in this field is Rhodorseal, which is manufactured by the French chemical giant Rhone-Poulenc and marketed in the UK by Interface Technologies. Rhodorseal is used extensively by the car industry, with over 10,000 vehicles leaving the production line every day with Rhodorseal used in their construction.
The only gasket that cannot be replaced by Rhodorseal, is the cylinder-head gasket, claims Interface. This is not because it cannot withstand the pressure, or temperature, but that the thickness of the gasket is crucial for regulating the compression ratio of the engine, which is particularly important with diesel engines.
Two ways to apply sealant
There are two ways to apply Rhodorseal: wet or dry. The former is for parts that are rarely taken apart. The mating surfaces are put together while the sealant is wet, thus allowing it to bond them together. If the bead is allowed to dry for a few hours, on one surface only, it will resume its original shape when the faces are parted again. So, one dry application will seal repeatedly, which is useful for covers like the rocker box. Using the wet method, new sealant has to be used each time.
Rhodorseal will operate from —70° up to 220° so can be used for exhaust man ifolds, It takes eight hours for a twomillimetre thickness to fully cure, but once cured it is strong enough to prevent any material that has extruded into the engine from breaking off, and possibly causing damage. Large swelling may occur where Rhodorseal is continuously immersed in diesel fuel, or petrol at 25°C
A company that is perhaps better known for its thread locking products, but also makes a variety of sealants, is Locate. Its general-purpose flange sealant is called the Multi-Gasket 574, and is claimed to fill gaps up to 0.5mm, and cure to half its full strength within one hour, at 5°C.
Multi-Gasket 574 is thixotropic, which means that it goes fluid when shaken in the bottle, but rapidly goes stiff once left. This makes it easier to apply to vertical surfaces. Loctite 518 is recommended for aluminium flanges, fills gaps up to 0.25mrn and is claimed to withstand flange movements caused by fluctuating pressures.
For machinery operating at temperatures up to 200°C Loctite 510, which has the best adhesion properties of the Loctite range, will resist the more corrosive industrial fluids and gases and will fill gaps up to 0.15mm. Like the other sealants, 510 can either be applied as a bead from a standard cartridge gun, or spread using a small paint roller.
Surplus is squeezed out
Unlike the silicone-based products such as Rhodorseal, the Loctite products do not set, or vulcanise, when exposed to the atmosphere, but set when they are deprived of air. They are known as anaerobic products, and one benefit is that any surplus matter that is squeezed out inside the engine remains liquid, and so does not clog up oil ways.
Unlike either conventional paper gaskets or silicone sealants, the Loctite sealants fill the joint in liquid form, so allowing the two faces to lock tightly together, which increases the strength of the completed structure. Loctite claims that fewer bolts of a lower tensile strength are needed be achieve the same strength where a malleable gasketing material is used.
The metal-to-metal contact which occurs with the Loctite sealants is also claimed to eliminate the need for retorqueing components after they have been running for a while. It should, however, be remembered that gasket compression is not the only reason to retorque a component: the different expansion rates of cases and fasteners such as an aluminium case retained by steel bolts, can cause the fasteners to relax.
Both Rhodorseal and Loctite are working on application systems that allow unskilled labour to safely apply the products. Automatic applicators are used by the manufacturers of engines with both products, and Loctite has developed a system of screen printing to apply its products. Rhodorseal is developing a system where an engine is built with no sealant at all, and the sealant is then injected into channels scalloped into the gasket surfaces. Rhodorseal hopes to have the system fully developed by the early 1990s.
A newcomer to the field of instant gaskets is Selectequip, which has introduced a product called Gasket Eliminator. Like the Loctite products, it is an anaerobic paste, which also has thixotropic qualities. It will cure in 15 minutes, and is effective between —50°C and 150°C and comes in 50 gramme tubes.
Protection in awkward corners
Removing old gasket material can be a real problem in awkward corners, where it has baked on. Loctite Chisel, which is part of the new Gasket pack, comes in a 100ml aerosol and softens heat hardened gaskets in 10 to 15 minutes. There is a plastic spatula included in the kit, so old gasket deposits can be removed without the risk of damaging the gasket surface. A further 100m1 aerosol of solvent is also included in Gaskit, which prepares the surface for sealing with Multi-Gasket, which completes the pack.
Wurth UK, which markets a wide range of engine assembly aids, also produces a gasket remover. Again available in aerosol form, it will also shift hardened cyanoacrylate adhesives, as well as paint, lacquer, tar residue, oil and grease.
No article on gasket sealants would be complete without mention of the Hermetite range. Hermetite has become the generic term for gasket compounds. These differ from the products already mentioned because they are used with gaskets, rather than replacing them.
The best known in the range is "red" Hermetite (all of the range is colourcoded). This compound was the first in troduced on to the market by Hermetite and still has a strong following among more traditional fitters. It is a semihardening compound which has a temperance range of between —40°C and 150°C, and can be used on all engine and transmission gaskets apart from the cylinder head gasket.
The highest temperature provided for by Hermetite compounds is 300°C. Green Hermetite, which is hard-setting and is designed as a permanent jointing compound, will also go down to —20°C. Used mainly by heavy industry, it should only be used on covers that are rarely, if ever, removed.
Golden Hermetite does not set, and resists fuels and antifreeze better than the others. Blue Hermetite is the most recent addition to the range, and like all the Hermetite universal gasket compounds is thixotrophic. These compounds are polymeric, which means that they contain resins, rather than being silicone-based.
By far the biggest selling product in the Hermetite range is the silicone RTV (room temperature vulcanising) instant gasket. This product, which is available either clear, or orange, replaces gaskets in the same way as does Rhodorseal, but rather than being used by the original equipment manufacturers, the Hermetite products find their main demand in the after-market. As with all silicone-based sealant, care must be taken to prevent any material squeezing out inside the engine.
The cardinal rule
Perhaps the aristocrat among gasket compounds is Hylomar, which is also made by Hunting lubricants, makers of Hermetite. Produced to a Rolls-Royce approved formula, Hylomar is a semisetting compound that will stand temperatures up to 250°C.
The cardinal rule with any sealant, be it one that replaces gaskets, or helps to seal them, is to be very sparing. A little compound applied to clean surfaces is all that is needed: any more will only risk damage to the engine with sealant being washed off by the lubricant. Although many of these sealants come equipped with dispensers, the fitter's finger is often the best tool.
The gasket will never completely disappear from the automotive industry, but all the growth in the market is away from gasket compounds and paper, and towards the gasket in the tube.