A NEW DESIGN OF PROPELLER SHAFT
Page 45
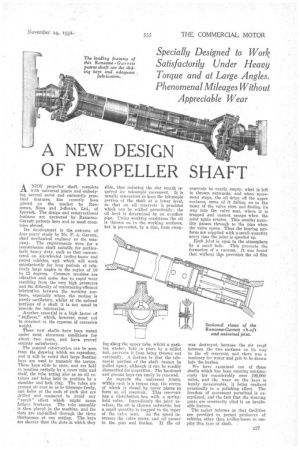
If you've noticed an error in this article please click here to report it so we can fix it.
ANEW propeller shaft, complete with universal joints and embodying several novel and eminently prac. tical features, has recently been placed on the market by Rancomes, Sims and Jefferies, Ltd., of Ipswich. The design and constructional features are protected by RansomeGarrett patents here and in most countries abroad.
Its development is the outcome of four years' study by Mr. F. A. Garrett, chief mechanical engineer to the company. The requirements were for a transmission shaft suitable for particularly heavy duty, such as that encountered on six-wheeled trolley-buses and petrol vehicles, and which Win work satisfactorily for long periods at relatively large angles in the region of 10 to 12 degrees. Common troubles are vibration and noise due to rapid wear resulting from the very high pressures and the difficulty of maintaining efficient lubrication between the working surfaces, especially where the motion is purely oscillatory, whilst at the splined portions of a shaft it is not usual to provide for lubrication.
Another essential is a high factor of "stiffness," which, however, must not be obtained at the expense of excessive weight.
These new shafts have been tested under most strenuous conditions for about two years, and have proved entirely satisfactory.
The general construction can be seen from the drawing which we reproduce, and it will be noted that large floating keys are used to transmit the torque. These keys slide in slots, and are held in position radially by a cover tube and shelf, the tube acting also as an oil retainer and being held in position by a shoulder and lock ring. The tubes are ground all over so as to telescope freely, and holes at the ends of bach slot are drilled and reamered to avoid any "notch" effect which might cause fatigue fractures. The tube assembly is then placed in the machine, and the slots are end-milled through the three thicknesses at one setting. The keys are shorter than the slots in which they slide, thus reducing the slot length required for telescopic movement. It is usuallv convenient to keep the telescopic portion of the Shaft at a lower level, so that an oil reservoir is provided which can be refilled periodically ; the oil level is determined by an overflow pipe. tinder working conditions the oil is thrown on to the working surfaces, but is prevented, by a disc, from creep
lag slang the upper tube, whilst a peeking washer, held in place by a milled mit, prevents it from being thrown out externally. A feature is that the telescopic portion of the shaft cannot be pulled apart, although it can be readily dismantled for inspection: The hardened and ground keys can easily be renewed.
As regards the universal joints, within each is a torque ring, the centre of which is closed by cover plates to form an oil reservoir. This reservoir has a distribution box with a springheld valve. Immediately the joint revolves, the oil is thrown outwards, but a small quantity is trapped in the taper of the valve seat. As the speed increases the valve opens, and oil passes to the pins and bushes. If the oil
reservoir be nearly empty, what is left is thrown outwards, and when movement stops, the oil drips off the upper surfaces, some of it falling on to the taper of the valve stem and finding its way into the valve seat, where it is trapped and cannot escape when the joint again rotates. This smaller quantity passes through to the pins when the valve opens. Thus the bearing surfaces are supplied with a small quantity every time the joint is speeded up.
Each joint is open to the atmosphere by a small hole. This prevents the formation of a vacuum. It was found that without this provision the oil film was destroyed, because the air crept between the two surfaces on its way to the oil reservoir, and there was a tendency for water and grit to be drawn into the bushes.
We have examined one of these shafts which has been running continuously for considerably over 100,000 miles, and the wear on the keys is barely measureable, it being confined practically to a polishing effect. The freedom of movement permitted is exceptional, and the fact that the wearing parts are constantly oiled is an invaluable feature.
The maker informs us that facilities are provided to permit producers of vehicles other than trolley-buses to employ this type of shaft. .