REQUIREMENTS IN A BUS SPECIFICATION.
Page 112
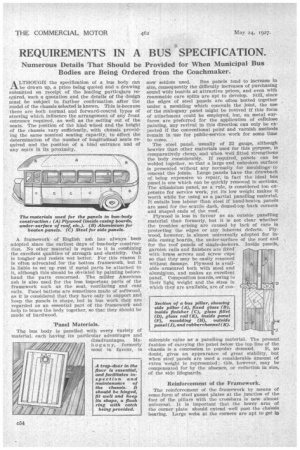
Page 113
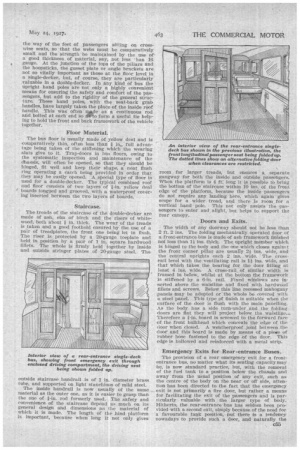
Page 114
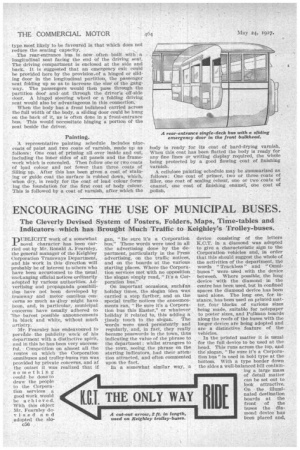
If you've noticed an error in this article please click here to report it so we can fix it.
Numerous Details That Should be Provided for When Municipal Bus Bodies are Being Ordered from the Coachmaker.
ALTHOTJGH the specification of a bus body can be drawn up, a price being quoted and a drawing submitted on receipt of the leading particulars required, -such a quotation and the details of the design must be subject to further confirmation after the model of the chassis selected is known. This is,because there are both normal and forward-control types of steering which influence the arrangement of any front entrance required, as well as the setting out of the seats. The position of the hind wheel and the height of the chassis vary sufficiently, with chassis providing the same nominal seating capacity, to affect the determination of the number of longitudinal seats required and the position of a hind entrance and of any seats irk its proximity.
A framework of English ash has always been adopted since the earliest days of bus-bodyconstruction. No other material is equal to it in combining the excellent qualities of strength and elasticity. Oak is tougher and resists wet better. For this reason it is often advocated for the bottom framework, but it is liable to set• up rust if metal parts be attached to it, although this should be obviated by painting beforehand the parts concerned. The milder American ash is also used, for the less important parts of the framework such as the seat, ventilating and cant rails. Panel battens are sometimes made of softwood, as it is considered that they have only to support and keep the pa n el s in shape, hut in bus work they are regarded as an essential part of the framework and help to brace the body together, so that they should be made of hardwood.
`Panel Materials.
The bus body is panelled with every variety of material, each having its particular advantages and disadvantages. Mahogany, formerly most in favour, is now seldom used. Bus panels tend to increase in size, consequently the difficulty increases of purchasing sound wide boards at attractive prices, and even with reasonable care splits are apt to develop. Still, since the edges of steel panels are often butted together under a moulding which conceals the joint, the use of the mahogany panel might be revived if this form of attachment could be employed, but, as metal surfaces are preferred for the application of cellulose painting, any revival in this direction can only be expected if the conventional paint and varnish methods remain in use for public-service work for some time to come.
The steel panel, usually of 22 gauge, although heavier than other materials used for this purpose, is comparatively cheap, and when well fitted strengthens the body considerably. If required, panels can be welded together, so that a large and unbroken surface is presented without any necessity for mouldings to conceal the joints. Large panels have the drawback of being expensive to repair, in fact the ideal bus panel is one which can be quickly removed in sections. The alliminium panel, as a rule, is considered too expensive for service work, yet its low weight makes it worth while for using as a partial panelling material. It entails less labour than steel if hand-beaten panels are used for the scuttle dash, domed-top back corners and shaped ends of the roof.
Plywood is less in favour as an outside panelling material than formerly, but it is not clear whether the troubles arising are caused by lack of care in protecting the edges or any inherent defects. Plywood, however, is almost universally adopted for inside casing boards, the under-surface of the roof and for the roof panels of single-deckers. Inside panels, garnish rails and finishers are fixedwith brass screws and screw cups ea that they may be easily removed without damage. Plywood is available armoured both with steel and alumiRium, and makes an excellent panel. Composition boards, owing to their light weight and the sizes in which they are available, are of con
siderable value as a panelling material. The present fashion of carrying the panel below the top line of the chassis is a concession to popular demand. It, no doubt, gives an appearance of great stability, but when steel panels are used a considerable amount of extra weight is represented ;. this, however, may be compensated for by the absence, or reduction in size, of the side lifeguards.
Reinforcement of the Framework.
The reinforcement of the framework by means of some form of steel gusset plates at the junction of the foot of the pillars with the crossbars is now almost universal. It is important that the lower arm of the corner plate should extend well past the chassis bearing. Large webs at the corners are apt to get in the way of the feet of passengers sitting on crosswise seats, so that the webs must be comparatively small and the strength be maintained by the use of a good thickness of material, say, not less 'han 16 gauge. At the junction of the tops of the pillars and the hoopsticks, the gusset plate or angle brackets are not so vitally important as those at the floor level in a single-decker, but, of course, they are particularly valuable in a double-decker. In any kind of bus the Upright hand poles are not only a highly convenient means for ensuring the safety and comfort of the passengers, but add to the rigidity of the general structure. These hand poles, with the seat-back grab handles, have largely taken the place of the inside roof handle. This was often ilade• as a continuous rod and bolted at each end so 110th form a useful tie helping to hold the front and back framework of the vehicle together.
Floor Material.
The bus floor is usually made of yellow deal and is comparatively thin, often less than I in„ full advantage being taken of the stiffening which the wearing slats give to it. Trap-doors in bus floors, owing to the systematic inspection and maintenance of the atassis, will often be opened, so that they should be hinged, fit well and keep their shape, a neat flush ring operating a catch being provided in order that they may be easily opened. .A special type of floor is used for a double-decker. The typical combined roof and floor consists of two layers of a-in. yellow deal boards tongued and grooved, with a waterproof covering inserted between the two layers Of beards.
Staircase.
The treads of the staircase of the double-decker are made of ash, elm of birch and the risers of whitewood, both about in. thick. The wear of the treads is .taken and a good foothold ensured by the use of a pair of treadplates, the front one being let in flush. The riser is protected by a 20-gauge toeplate and held in position by a .pair of 1 in, square hardwood fillets. The whole is firmly held 'together by inside and outside stringer plates of 20-gauge steel. The
outside staircase handrail is of 1 in. diameter brass tube, and supported on light stanchions of mild steel.
The inside handrail is now usually of the same._ material as the outer one, as it is easier to grasp than the one of Fin, rod formerly used. The safety and convenience of the staircase depend as much on its general design and dimensions as the material of which it is made. The length of the hind platform is important, because when long it not only gives
room for larger treads, but ensures a. separate gangway for, both the inside and outside passengers. -When the platform is 4 ft: long it is possible to.bring the bottom of the staircase within 10 ins, of the front edge of the platform, because the inside passengers do not require any landing here, which again gives scope for a wider tread, and there is room for a vertical hand pole. This not onlyassists the passengers to enter and alight, but helps to support the rear canopy.
Doors and Exits.
The width of any doorway should not be less than 2 ft. 2 ins. The folding mechanically operated door of a front-entrance bus is made of ash. framework finished not less than 11 ins. thick. The upright member which is hinged to the body and the one which closes again t the front corner pillar are usuafly 2i Ins, wide, and the central uprights each 2 ins. wide. The .crossTail level with the ventilating rail is 1.1 ins, wide, and that which takes the bearing for the door fitting at least 4 ins. wide. A cross-rail of similar width is framed in below, whilst at the bottom the framework is stiffened by a 6-in. rail. Fixed windows are inserted above the waistline and fixed with hardwood fillets and screws. Below this line recessed Mahogany panels may be adopted or-the whole be covered with a steel panel. This type of finish is suitable when the surface of the door is flush with the main panelling. As the body has a side turn-under and the folding floors are flat they will project below the. waistline... Therefore a fin, board is screwed to the forward face of. the front bulkhead which conceals the edge of the door when closed. A weatherproof joint between the door and this board is made by means of a piece of rubber hosefastened to the edge of the door. This edge is hollowed and reinforced with a metal strip.
Emergency Exits for Rear-entrance Buses.
'The provision of a rear emergency exit for a frontentrance bus, no matter what its seating capacity may be, is now standard practice, but, with the removal of the fuel tank to a position below the chassis and away from the usual position of any exit, such as the centre of the body on the near or off side, attention has been directed to the fact that the emergency • exit is not primarily a fire door, but rather a means for facilitating the exit of the passengers and is particularly valuable with the larger type of body. Hitherto, the rear-entrance bus has seldom been provided with a second exit, simply because of the need for a favourable tank position, but there is a tendency nowadays to provide such a door, and naturally the type most ,likely to be favoured is. that which does not reduce the seating 'capacity.
• The rear-entrance bus is now often• built with ; a 'longitudinal seat facing the end of the driving seat. The driving compartment is enclosed at the side and back. It is suggested that an emergency exit could he provided here by the provision,of a hinged or sliding door in the longitudinal partition, the passenger seat folding up so as to increase the sizeof the gangway. The passengers would then pass through the partition doot and out through the driver's off-side door. A hinged steering wheel or a folding driving seat would also be advantageous in this connection:.
When the body has a front bulkhead carried across the full width of the body, a sliding door could be hung on the back of it, as is often done in a front-entrance bus. This would necessitate hinging a portion of the seat beside the driver.
Painting.
A representative painting schedule includes nines coats of paint and two coats of varnish, made up as follows : One coat of priming all over inside and out, including the inner sides of all panels and the framework which is concealed. Then follow one or two coats of lead colour and not fewerthan three coats of filling up. After this has been given a coat of staining or guide coat the surface is rubbed down, which, when dry, is ready for the coat of lead colour forming the foundation for the first coat of body colour. This is followed by a coat of varnish, after .which the
body is ready for its coat of hard-drying varnish. When this coat has been flatted the body is ready for any fine lines or writing display required, the whole being protected by a good flowing coat of finishing varnish.
A cellulose painting schedule may be summarized as follows: One coat of primer, two or three coats of filler, one coat of sealing colour, one or two coats of enamel, one coat of finishing enamel, one coat of polish.