The Best System of Lubrication for Internal Combustion Engines.
Page 5
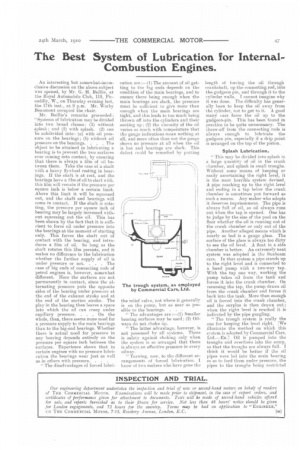
Page 6
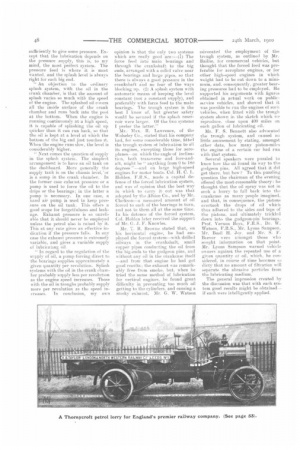
If you've noticed an error in this article please click here to report it so we can fix it.
An interesting but winewhat-inconelusive discussion on the above subject was opened, by Mr. G. 11. Bai!lie, at the _Royal Automobile Club, 119, Piccadilly, W., on Thursday evening last, the 17th inst., at 9 p.m. Mr_ Worby Beaumont occupied the chair. Mr_ Baillie's remarks proceeded : "Systems of lubrication may be divided into two broad classes : (I) without splash ; and (2) with splash. (2) can be subdivided into : (a) with oil pressure on the bearings; (b) without oil pressure on the bearings. . . The object to be attained in lubricating a bearing is to prevent the two surfaces ever coming into contact, by ensuring that there is always a film of oil between them. Take the case of a shaft with, a heavy flywheel resting in bearings. ff the shaft is at rest, and the bearings have a film of oil to start with. this film will remain if the pressure per square inch is below a certain limit. Above this limit it will be squeezed out, and the shaft and bearings will come in contact. If the shaft is rotating, the pressure per square inch of bearing may be largely increased without squeezing out the oil. This has been shown by the fact that it is sufficient to force oil under pressure into the bearings at the moment of starting only_ This forces the shaft out of contact with the bearing, and introduces a film of oil. So long as the shaft rotates this film persists, and it makes no difference to the lubrication whether the further supply of oil is under pressure or not. . . . The case of big ends of connecting rods of petrol engines is, however, somewhat different. Here the surfaces are not permanently in contact, since the alternating pressure puts the opposite sides of the bearing under pressure at the end of the exhaust stroke and at the end of the suction stroke. The play in the bearing then leaves a space into which the oil ran creep under capillary pressure. . . On the whole, then, there seems more need for a pressure supply to the main bearings than to the big-end bearings. Whether there is actual need for pressure in any bearing depends entirely on the pressure per square inch between the surfaces. Experience shows that in certain engines with no pressure lubrication the hearings wear just as well as in others with pressure. . . .
" The disadvantages of forced 101)6
cation are :—(1) The amount of oil getting to the big ends depends on the condition of the main bearings, and to ensure there being enough when the main bearings are slack, the pressure must be sufficient to give more than enough when the main bearings are tight, and this leads to too much being thrown off into the cylinders and their sooting up ; (2) the viscosity of the oil varies so much with temperature that the gauge indications mean nothing at all, and more often than not the gauge shows no pressure at all when the oil is hot and bearings are slack. Timis defect could be remedied by putting
the relief valve, not where it generally is on the pimp, hut as near as possible to the bearings. . . . " The advantages are :—(1) Smaller bearing surfaces may be used ; (2) Oilways do not choke up.
"The latter advantage, however, is not possessed by all systems. There is safety against choking only when the system is so arranged that there is always an effective pressure in every away.
" Turning, now, to the different arrangements of forced lubrication. 1 know of two makers who have gone the
length of forcing the oil through crankshaft, up the connecting rod, into the gudgeon pin, and through it to the cylinder walls. I cannot imagine why it was done. The difficulty has generally been to keep the oil away from the cylinder, not to get to it. A good many cars force the oil up to the gudgeon-pin. This has been found in practice to be quite unnecessary. The throw-off from the connecting rods is always enough to lubricate the gudgeon pin, especially if a drip point is arranged on the top of the piston.
Splash Lubrication.
" This may be divided into splash in a large quantity of oil in the crank chamber, and splash in small troughs. Without some means of keeping or easily ascertaining the right level, it is the most horrible system devised. A pipe reaching up to the right level and ending in a tap below the crank chamber is sometimes put forward as such a means. Any maker who adopts it deserves imprisonment. The pipe is always full of oil, so oil always runs out when the tap is opened. One has to judge by the size of the pool on the floor whether the oil is running out of the crank chamber or only out of the pipe. Another alleged means which is nearly as bad is a gauge glass. The surface of the glass is always too dirty to see the oil level. A float in a side chamber is better. An extremely neat system was adopted in the Sunbeam cars. In that system a pipe stands up to the right level and is connected to a hand pump with a two-way tap. With the tap one way, working the pump takes oil from the tank and forces it into the crank chamber. On reversing the tap, the pump draws oil from the crank chamber and farces it back into the tank. More than enough oil is forced into the crank chamber, and the surplus is then drawn out; when the right level is reached it is indicated by the pipe gurgling.
" The trough system is really the one for keeping the level right. [We illustrate the method on which this system is adopted by Commercial Cars, Ltd.--En.] Oil is pumped into the troughs and overflows into the sump, so that the troughs are always full. think it would be better if the oil pipes were led into the main bearing so as to feed them under pressure. the pipes to the troughs being restricted sufficiently to give some pressure. Except that the lubrication depends on the pressure supply, this is, to my mind, the most perfect system. The pressure feed is where it is most wanted, and the splash level is always right for each big end.
" An objection to the ordinary splash system, with the oil in the crank chamber, is that the amount of splash varies so much with the speed ot the engine. The splashed oil covers all the inside surface of the crank chamber and runs back into the pool at the bottom_ When the engine is running continuously at a high speed, it is capable of splashing the oil up quicker than it can run back, so that the oil is kept at a level at which the bottom of the big end just touches it. When the engine runs slow, the level is considerably higher.
" Next comes the question of supply in the splash system. The simpleet arrangement is to have an oil tank on the dashboard. More generally the supply tank is on the chassis level, 'or is a sump in the crank chamber. In the former case exhaust pressure or a pump is used to force the oil to the drips or the bearings ; in the latter a pump is necessary. In one case, a hand air pump is used to keep pressure on the oil tank. This offers a good scope for forgetfulness and leakage. Exhaust pressure is so unreliable that it should never be employed unless the petrol also is raised by it. This at any rate gives an effective indication if the pressure falls. In any case the exhaust pressure is extremely variable, and gives a. variable supply of lubricating oil.
" In regard to the regulation of the supply of oil, a pump forcing direct to the bearings supplies approximately a given quantity per revolution. Splash systems with the oil in the crank chamber probably supply less per revolution as the engine speed increases. Those with the oil in troughs probably supply more per revolution as the speed increases. In conclusion, may own opinion is that the only two systems which are really good are :--(1) The force feed into main bearings and through the crankshaft to the big ends, arranged with a relief valve near the bearings and large pipes, so that there is always a good pressure in the crankshaft and no fear of the ways blocking tip. (2) A splash system with automatic means of keeping the level constant (not a constant supply), and preferably with force feed to the main bearings. The trough system is the best T know of, but greater safety would be secured if the splash reservoir were larger. Of the two systems I prefer the latter."
Mr.. Max. R. Lawrence, of the Wolseley Co., stated that his company had for some co risim tern ble time fitted the trough system of lubrication to all its engines, excepting those for aeroplanes—on which the angle of inclination, both transverse and fore-andaft, might be " nnything from 0 to 180 degrees "--and on largo high-speed engines for motor boats. Col. H. C. L. Holden, F.R.S., made a capital defence of the forced lubrication system, and was of opinion that the best way in winch to carry it out was that adopted by the Albion Co., and by Mr. Clarkson—a measared amount of oil forced to each of the bearings in turn, and not to them all at the same time. In his defence of the forced system, Col. Holden later received the support of Mr. C. J. F. I:nowles.
Mr. T. B. Browne stated that, on his horizontal engine, he had employed the forced system—with drilled oilways in the crankshaft, small copper pipes conducting the oil from the big-ends to the gudgeon pins, and without anv nil in the crankcase itself —and from that engine he had got good results ; the exhaust was remarkably free from smoke, but, when he tried the same method of lubrication for vertical engines, he found great difficulty in preventing too much oil getting to the cylinders, and causing a smoky exhaust. Mr. G. W. Watson advocated the employment of tho trough system, as outlined by Mr. Baillie, for commercial vehicles, but thought that the forced feed was preferable for aeroplane engines, or for other high-speed engines in which weight had to be cut down to a minimum, and, consequently, greater bearMg pressures had to be employed. He supported his arguments with figures obtained in actual work on publicservice vehicles, and showed that it was possible to run the engines of such vehicles, when fitted with the trough system shown in the sketch which we reproduce, close upon 400 miles on each gallon of lubricating oil.
Mr. F. S. Bennett also advocated the trough system, and caused no little amusement by stating, amongst other data, how many piston-miles the engine of a certain car had run with that system. Several speakers were puzzled to know how the oil found its way to the gudgeon pins. All agreed that it did get there, but how ? To this puzzling question the chairman of the evening offered the most-reasonable theory : he thought that the oil spray was not in such a hurry to fall back into the crankcase as many people imagined, and that, in consequence, the pistons overtook the drops of oil which thus adhered to the sides and tops of the pistons, and ultimately trickled down into the gudgeon-pin bearings.
Prof. Vernon Boys, F.R.S., Dr. W.
Watson, F.R.S., Mr. Lyons Sampson,. Mr. Basil H. Joy. and Mr. S. F. Beevor ii erc amongst those who sought information on that point. Mr. Lyons Sampson warned vehicle
on ners against the repeated use of a
given quantity of oil, which, he considered, in course of time becomes ea dirty that no amount of filtration will separate the abrasive particles from the lubricating medium, The general impression created by the discussion was that with each system good resultsmight be obtained— if each were intelligently applied_