Check points
Page 19
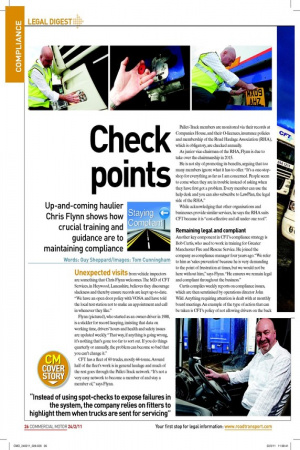
Page 21
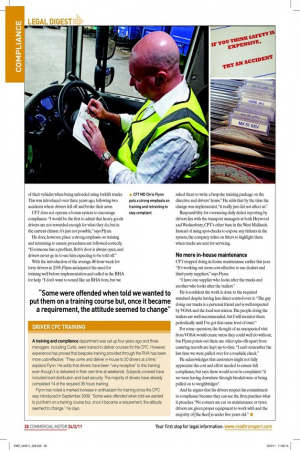
If you've noticed an error in this article please click here to report it so we can fix it.
Up-and-coming haulier Chris Flynn shows how crucial training and guidance are to maintaining compliance
Words: Guy Sheppard/Images: Tom Cunningham Unexpected visits from vehicle inspectors are something that Chris Flynn welcomes. The MD of CFT Services, in Heywood, Lancashire, believes they discourage slackness and thereby ensure records are kept up-to-date. “We have an open door policy with VOSA and have told the local test station not to make an appointment and call in whenever they like.”
Flynn (pictured), who started as an owner-driver in 1988, is a stickler for record keeping, insisting that data on working time, drivers’ hours and health and safety issues are updated weekly. “That way, if anything is going wrong, it’s nothing that’s gone too far to sort out. If you do things quarterly or annually, the problem can become so bad that you can’t change it.” CFT has a leet of 60 trucks, mostly 44-tonne. Around half of the leet’s work is in general haulage and much of the rest goes through the Pallet-Track network. “It’s not a very easy network to become a member of and stay a member of,” says Flynn. Pallet-Track members are monitored via their records at Companies House, and their O-licences, insurance policies and membership of the Road Haulage Association (RHA), which is obligatory, are checked annually.
As junior vice-chairman of the RHA, Flynn is due to take over the chairmanship in 2015.
He is not shy of promoting its beneits, arguing that too many members ignore what it has to offer. “It’s a one-stopshop for everything as far as I am concerned. People seem to come when they are in trouble instead of asking when they have irst got a problem. Every member can use the help desk and you can also subscribe to LawPlan, the legal side of the RHA.” While acknowledging that other organisations and businesses provide similar services, he says the RHA suits CFT because it is “cost-effective and all under one roof”.
Remaining legal and compliant
Another key component in CFT’s compliance strategy is Bob Curtis, who used to work in training for Greater Manchester Fire and Rescue Service. He joined the company as compliance manager four years ago. “We refer to him as ‘sales prevention’ because he is very demanding to the point of frustration at times, but we would not be here without him,” says Flynn. “He ensures we remain legal and compliant throughout the business.” Curtis compiles weekly reports on compliance issues, which are then scrutinised by operations director John Wild. Anything requiring attention is dealt with at monthly board meetings. An example of the type of action that can be taken is CFT’s policy of not allowing drivers on the back
of their vehicles when being unloaded using forklift trucks. ▲ CFT MD Chris Flynn This was introduced over three years ago, following two puts a strong emphasis on accidents where drivers fell off and broke their arms. training and retraining to CFT does not operate a bonus system to encourage stay compliant
compliance. “I would be the irst to admit that heavy goods drivers are not rewarded enough for what they do, but in the current climate it’s just not possible,” says Flynn.
He does, however, place a strong emphasis on training and retraining to ensure procedures are followed correctly. “If someone has a problem, Bob’s door is always open, and drivers never go in to see him expecting to be told off.” With the introduction of the average 48-hour week for lorry drivers in 2005, Flynn anticipated the need for training well before implementation and called in the RHA for help. “I don’t want to sound like an RHA bore, but we asked them to write a bespoke training package on the directive and drivers’ hours.” He adds that by the time the change was implemented, “it really just did not affect us”.
Responsibility for overseeing daily defect reporting by drivers lies with the transport managers at both Heywood and Wednesbury, CFT’s other base in the West Midlands. Instead of using spot-checks to expose any failures in the system, the company relies on itters to highlight them when trucks are sent for servicing.
No more in-house maintenance
CFT stopped doing in-house maintenance earlier this year. “It’s working out more cost-effective to use dealers and third party suppliers,” says Flynn.
“I have one supplier who looks after the trucks and another who looks after the trailers.” He is conident the work is done to the required standard despite having less direct control over it. “The guy doing our trucks is a personal friend and is well-respected by VOSA and the local test station. The people doing the trailers are well-recommended, but I will monitor them periodically until I’ve got that same level of trust.” For some operators, the thought of an unexpected visit from VOSA would create stress they could well do without, but Flynn points out there are other spin-offs apart from ensuring records are kept up-to-date. “I can’t remember the last time we were pulled over for a roadside check.” He acknowledges that customers might not fully appreciate the cost and effort needed to ensure full compliance, but says there would soon be complaints “if we were having downtime through breakdowns or being pulled on to weighbridges”.
And he argues that his drivers respect his commitment to compliance because they can see the irm practises what it preaches. “No corners are cut on maintenance or tyres; drivers are given proper equipment to work with and the majority of [the leet] is under ive years old.” ■