A 200-ton Trailer •
Page 43
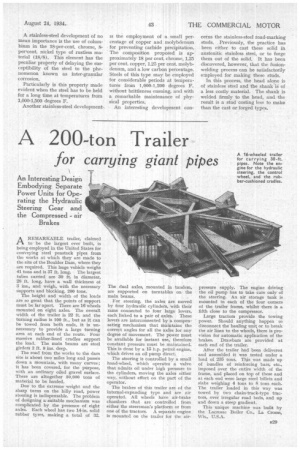
If you've noticed an error in this article please click here to report it so we can fix it.
for carrying giant pipes
An Interesting Design Embodying Separate Power Units for Operating the Hydraulic Steering Gear and the Compressed air Brakes
AREMARKABLE trailer, claimed to be the largest ever built, is being employed in the United States for conveying steel penstock pipes from the works at which they are made to the site of the Boulder Darn, where they are required. This huge vehicle weighs 41 tons and is 37 ft. long. The largest tubes carried are 30 ft. in diameter, 28 ft. long, have a wall thickness of 3 ins., and weigh, with the necessary supports and blocking, 200 tons.
The height and width of the loads are so great that the points of support must be far apart. There are 16 wheels mounted on eight axles. The overall width of the trailer is 22 ft. and the turning radius is 100 ft., but as it can be towed from both ends, it is unnecessary to provide a large turning area at each end of the route. Four massive rubber-lined cradles support the load. The main beams are steel girders 2 ft. 9 ins. deep.
The road from the works to the dam site is about two miles long and passes down a mountain, with many curves ; it has been covered, for the purpose, with an ordinary oiled gravel surface. There are altogether 50,000 tons of material to be hauled.
Due to the extreme weight and the sharp turns on the hilly road, power steering is indispensable. The problem of designing a suitable mechanism was complicated by the presence of eight axles. Each wheel has two 14-in, solid rubber tyres, making a total of 32. The dual axles, mounted in tandem, are supported on turntables on the main beams.
For steering, the axles are moved by four hydraulic cylinders, with their rams connected to four large levers, each linked to a pair of axles. These levers are interconnected by a compensating mechanism that maintains the correct angles for all the axles for any degree of movement. The power must be available for instant use, therefore constant pressure must be maintained. This is done by a 15 h.p. petrol engine, which drives an oil pump direct.
The steering is controlled by a small hand-wheel, which operates a valve that admits oil under high pressure to the cylinders, moving the axles either way, without effort on the part of the operator.
The brakes of this trailer are of the internal-expanding type and are air operated. All wheels have air-brake chambers that are controlled from either the steersman's platform or from one of the tractors. A separate engine is mounted on the trailer for the air
pressure supply. The engine driving the oil pump has to take care only of the steering. An air storage tank is mounted in each of the four corners of the trailer frame, whilst there is a fifth close to the compressor.
Large tractors provide the towing power. Should anything happen to disconnect the hauling unit, or to break the air lines to the wheels, there is provision for automatic application of the brakes. Drawbars are provided at each end of the trailer.
After the trailer had been delivered and assembled it was tested under a load of 235 tons. This was made .up of bundles of reinforcing bars, etc., imposed over the entire width of the frame, and placed on top of these and at each end were large steel billets and slabs weighing 4 tons to 8 tons each. The trailer loaded in this way was towed by two chain-track-type tractors, over irregular road beds, and up and down a steep gradient.
This unique machine was built by the Lacrosse Boiler Co., La Crosse, Wis., U.S.A.