A "Magnetic-top" Torque Converter
Page 66
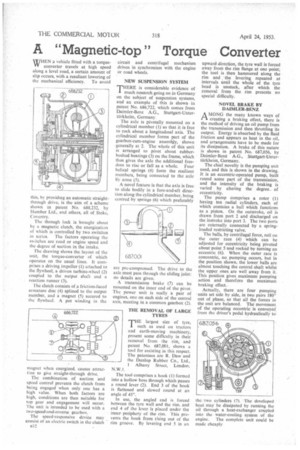
If you've noticed an error in this article please click here to report it so we can fix it.
W e WHEN a vehicle fitted with a torque travels at high speed along a level road, a certain amount of slip occurs, with a resultant lowering of the mechanical efficiency. To avoid this, by providing an automatic straightthrough drive, is the aim of a scheme shown in patent No. 688,232, by Humber Ltd., and others, all of Stoke, Coventry.
The through lock is brought about by a magnetic clutch, the energization of which is controlled by two switches in series. The factors operating the su itches are:road or engine speed and the degree of suction in the intake.
The drawing shows the layout of the unit, the torque-converter of which operates on the usual lines. It comprises a driving impeller (I) attached to the flywheel, a driven turbine-wheel (2) coupled to the output shaft arid a reaction runner (3).
The clutch consists of a friction-faced armature disc (4) splined to the output member, and a magnet (5) secured to the flywheel. A pot winding in the magnet when energized, causes attraction to give straight-through drive.
The combination of suction and speed control prevents the clutch from being engaged when only one has a high value. When both factors arc high, conditions are then suitable for lop gear and engagement will occur. The unit is intended to be used with a two-speed-and-reverse gearbox.
The speed-responsive device may consist of an electric switch in the clutch n32 circuit and centrifugal mechanism driven in synchronism with the engine or road wheels.
NEW SUSPENSION SYSTEM
THERE is considerable evidence of I much research going on in Germany on the subject of suspension systems, arid an example of this is shown in patent No. 686,722, which comes from Daimler-Benz A.G., Stuttgart-Unterttirkheim, Germany.
The axle is pivotally mounted on a cylindrical member (I) so that it is free to rock about a longitudinal axis. The cylindrical member forms part of the gearbox-cum-engine assemlajy, shown generally at 2. The whole of this unit is arranged to pivot about rubberbushed bearings (3) on the frame, which thus gives the axle the additional freedom to rise or fall as a whole. Four helical springs (4) form the resilient members, being connected to the axle by arms (5).
A novel feature is that the axle is freeto slide bodily in a fore-and-aft direction along the cylindrical member, being centred by springs (6) which preferably
are pre-compressed. The drive to the axle must pass through the sliding joint: no details are given.
A transmission brake (7) can be mounted on the inner end of the pivot. The power unit is really a pair of engines, one on each side of the central axis, meeting in a common gearbox (2).
THE REMOVAL OF LARGE TYRES
THE largest size of tyre, such as used on tractors and earth-moving machinery, present some difficulty in their removal from the rim, and patent No. 687,001, shows a tool for assisting in this respect. The patentees are R. Daw and the Dunlop Rubber Co., Ltd., 1 Albany Street, London, N.W.I.
The tool comprises a hook (1) formed into a hollow boss through which passes a round lever (2). End 3 of the hook is flattened and slesvcd round at an angle of 45°.
In use, the angled end is forced between the tyre wall and the rim, and end 4 of the lever is placed under the innerperiphery of the rim. This prevents the hook from rising out of the rim groove. By levering end 5 in an upward direction, the tyre wall is forced away from the rim flange at one point; the tool is then hammered along the rim and the levering repeated at intervals until the whole of the tyre bead is unstuck, after which the removal from the rim presents no special difficulty.
NOVEL BRAKE BY DAIMLER-BENZ
A MONG the many known ways of creating a braking effect, there is
the method of driving an oil pump from the transmission and then throttling its output. Energy is absorbed by the fluid friction and appears as heat in the oil, and arrangements have to be made for its dissipation. A brake of this nature is shown in patent No. 687.056, by Daimler-Benz A.G., Stuttgart-Untertilirkheim, Germany.
The chief novelty is the pumping unit
used, and this is shown in the drawing. It is an eccentric-operated pump, built round some part of the transmission, and the intensity of the braking is varied by altering the degree. of eccentricity.
The pump comprises a rotor (1) having ten radial cylinders, each of which contains a ball which functions as a piston. On the outstroke, oil is drawn from port 2 and discharged on the instrokc into port 3. The two ports are externally connected by a springloaded restricting valve.
The halls, by centrifugal force, roll on
the outer race (4) which can be adjusted for eccentricity being pivoted about point 5 and rocked by turning an eccentric (6). When the outer race is concentric, no, pumping occurs, but in the position shown, the lower halls are almost touching the central shaft whilst the upper ones are well away from it. This position gives maximum pumping action and therefore the maximum braking effect.
Actually, there are four pumping
units set side by side, in two pairs 1800 out of phase, so that all the forces in the unit are balanced. The movement of the operating eccentric is conveyed from the driver's pedal hydraulically to the two cylinders (7). The developed heat may be dissipated by running the oil through a heat-exchanger coupled into the water-cooling system of the
engine. The complete unit could be made cheaply