Bermondsey goes for Burtonwood
Page 60
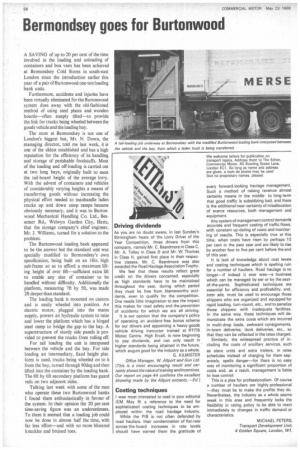
If you've noticed an error in this article please click here to report it so we can fix it.
A SAVING of up to 20 per cent of the time involved in the loading and unloading of containers and box vans has been achieved at Bermondsey Cold Stores in south-east London since the introduction earlier this year of a pair of Burtonwood one-ton loading bank units.
Furthermore, accidents and injuries have been virtually eliminated for the Buttonwood system does away with the old-fashioned method of using steel plates and wooden boards—often steeply tilted—to provide the link for trucks being wheeled between the goods vehicle and the loading bay.
The store at Bermondsey is not one of London's biggest but. Mr. N. Down, the managing director, told me last week, it is one of the oldest established and has a high reputation for the efficiency of its handling and storage of perishable foodstuffs. Most of the loading and off-loading is carried out at two long bays, originally built to meet the tail-board height of the average lorry. With the advent of containers and vehicles of considerably varying heights a means of transferring goods without increasing the physical effort needed to manhandle laden trucks up and down steep ramps became obviously necessary, and it was to Burtonwood Mechanical Handling Co. Ltd., Bessemer Rd., Welwyn Garden City. Hefts, that the storage company's chief engineer, Mr. J. Williams, turned for a solution to the problem.
The Burtonwood loading bank appeared to be the answer but the standard unit was specially modified to Bermondsey's own specification, being built on an 18in. high sub-frame so as to afford a maximum lifting height of over 6ft—sufficient extra lift to enable any size of container to be handled without difficulty. Additionally the platform, measuring 7ft by 5ft, was made 2ft deeper than standard.
The loading bank is mounted on castors and is easily wheeled into position. An electric motor, plugged into the mains supply, powers an hydraulic system to raise and lower the platform which has a hinged steel ramp to bridge the gap to the bay. A superstructure of sturdy side panels is provided to prevent the trucks from rolling off.
For tail loading the unit is interposed between the vehicle and the bay. For side loading an intermediary, fixed height platform is used, trucks being wheeled on to it from the bay, turned through 90deg and then lifted into the container by the loading bank. The 8ft by 6ft secondary platform has guard rails on two adjacent sides.
Talking last week with some of the men who operate these two Burtonwood banks I found them enthusiastically in favour of the system. In their opinion the 20 per cent time-saving figure was an underestimate. To them it seemed that a loading job could now be done in almost half the time, with far less effort—and with no more blistered knuckles and bruised toes. Driving dividends As you are no doubt aware, in last Sunday's Birmingham heats of the Lorry Driver of the Year Competition, three drivers from this company, namely Mr. C. Beardmore in Class C, Mr. A. Tolley in Class D and Mr. W. Thomas in Class H. gained first place in their respective classes. Mr. C. Beardmore was also awarded the Road Haulage Association Trophy.
We feel that these results reflect great credit on the drivers concerned, especially as high standards have to be maintained throughout the year, during which period they must be free from blameworthy accidents, even to qualify for the competition. One needs little imagination to see the impact this makes for road safety and the prevention of accidents for which we are all striving.
It is our opinion that the company's policy of operating an accident-free bonus scheme for our drivers and appointing a heavy goods vehicle driving instructor trained at RTITB Motec Centre, High Ercall, is now beginning to pay dividends, and can only result in higher standards being attained in the future, which augurs good for the industry as a whole.
G. KILMISTER Office Manager, W. Al/port and Son Ltd. I This is a most encouraging result and certainly shows the value of training and incentives. Our report on page 44 confirms the excellent showing made by the Al/port entrants.—Ed.
Costing techniques
I was most interested to read in your editorial (CM May 9) a reference to the need for sophisticated costing techniques to be employed within the road haulage industry.
While the PI6 is not often defended by road hauliers. their condemnation of flat-rate across-the-board increases in rate levels should have earned them the gratitude of every forward-looking haulage management. Such a method of raising revenue almost certainly means in the middleto long-term that good traffic is subsidizing bad, and there is the additional near-certainty of misallocation of scarce resources, both management and equipment.
Any system of management control demands accurate and frequent costing of traffic flows, with constant up-dating of costs and monitoring of results. This is especially true at this time, when costs have risen by perhaps 10 per cent in the past year and are likely to rise by another four to five per cent before the end of this year.
It is lack of knowledge about cost levels and costing techniques which is spelling ruin for a number of hauliers. Road haulage is no longer—if indeed it ever was—a business which can be managed by ear or by the seatof-the-pants. Sophisticated techniques are essential for efficiency and profitability, and, inter alia, must be used to encourage those shippers who are organized and equipped for rapid loading, turn-round, etc., and to penalize those shippers with inadequate facilities. In the same way. these techniques will demonstrate the extra costs which are incurred in multi-drop loads, awkward consignments, in-town deliveries, dock deliveries, etc., so that they can be reflected in the rates charged.
Similarly, the widespread practice of including the costs of ancillary services, such as slave units and extra trailers, in rates schedules instead of charging for them separately, spells danger—for there is no easy way of monitoring a significant proportion of costs and, as a result, management is liable to lose control.
This is a plea for professionalism. Of course a number of hauliers are highly professional —they must be to make the profits they do. Nevertheless, the industry as a whole seems weak in this area and frequently lacks the flexibility in rating policy to be able to react immediately to changes in traffic demand or characteristics.