road and
Page 56
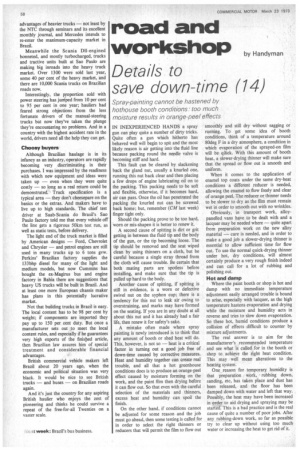
If you've noticed an error in this article please click here to report it so we can fix it.
workshop by Handyman
Details to save down-time (14)
Spray-painting cannot be hastened by hothouse booth conditions: too much moisture results in orange-peel effects
IN INEXPERIENCED HANDS a spray gun can play quite a number of dirty tricks. Quite often a gun which hitherto has behaved well will begin to spit and the most likely reason is air getting into the fluid line because packing round the needle valve is becoming stiff and hard.
This fault can be cleared by slackening back the gland nut, usually a knurled one, running this nut back clear and then placing a few drops of engine lubricating oil on to the packing. This packing needs to be soft and flexible, otherwise, if it becomes hard, air can pass. Once the oil has penetrated the packing the knurled nut can be screwed back home; but, remember (CM last week) finger tight only.
Should the packing prove to be too hard, worn or mis-shapen it is better to renew it.
A second cause of spitting is dirt or grit getting in between the fluid tip and the body of the gun, or the tip becoming loose. The tip should be removed and the seat wiped clean by using thinners on a cloth, but be careful because a single stray thread from the cloth will cause trouble. Be certain that both mating parts are spotless before installing, and make sure that the tip is pulled up hard to the body.
Another cause of spitting, if spitting is still in evidence, is a worn or defective swivel nut on the syphon cup; there is a tendency for this nut to leak air owing to overstraining, and marks may have formed on the seating. If you are in any doubt at all about this nut and it has already had a fair life, then renew it for safety's sake.
A mistake often made where spray painting is newly introduced is to think that any amount of booth or shed heat will do. This, however, is not so — heat is a critical factor in turning out a good job free of down-time caused by corrective measures. Heat and humidity together can create real trouble, and all that a hot greenhouse conditions does is to produce an orange-peel effect caused by moisture forming on the work, and the paint film then drying before it can flow out. So that even with the careful selection of the materials and thinners, excess heat and humidity can spoil the finish.
On the other hand, if conditions cannot be adjusted for some reason and the job must go ahead, then some testing is called for in order to select the right thinners or reducers that will permit the film to flow out smoothly and still dry without sagging or running. To get some idea of booth conditions, think of a temperature around &Meg F in a dry atmosphere, a condition in which evaporation of the sprayed-on film will be qilick. With this amount of booth heat, a slower-drying thinner will make sure that the spread or flow out is smooth and uniform.
When it comes to the application of enamel top coats under the same dry-heat conditions a different reducer is needed, allowing the enamel to flow freely and clear of orange peel. The reducer or thinner needs to be slower to dry as the film must remain wet in order to smooth out with no wrinkles.
Obviously, in transport work, alloypanelled vans have to be dealt with and a lacquer may be needed where — quite apart from preparation work on the new alloy material — care is needed, and in order to make a good job a slower-drying thinner is essential to allow sufficient time for flow out. To use the normal quick-drying thinner under hot, dry conditions, will almost certainly produce a very rough finish indeed and can call for a lot of rubbing and polishing out.
Hot and damp Where the paint booth or shop is hot and damp with no immediate temperature adjustment easily arranged trouble is bound to arise, especially with lacquer, as the high temperature hastens evaporation and drying while the moisture and humidity acts in reverse and tries to slow down evaporation. So these hot, humid conditions produce a collision of effects difficult to counter by mixture adjustments.
The real answer is to aim for the manufacturer's recommended temperature and see what is called for in the booth or shop to achieve the right heat condition. This may well mean alterations to the heating system.
One reason for temporary humidity is that preparation work, rubbing down, sanding, etc, has taken place and dust has been released, and the floor has been damped down with water and left that way. Possibly, the heat may have been increased in order to aid drying and spraying may be started. This is a bad practice and is the real cause of quite a number of poor jobs. After any rubbing-down work, so far as possible try to clear up without using too much water or increasing the heat to get rid of it.