Electronic Vehicle Control is a Reality
Page 48
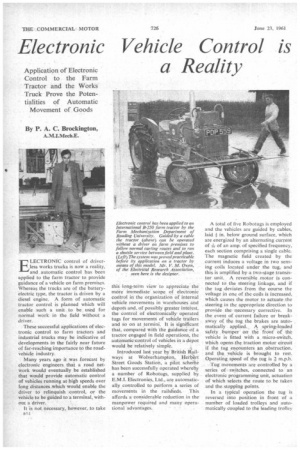
Page 49
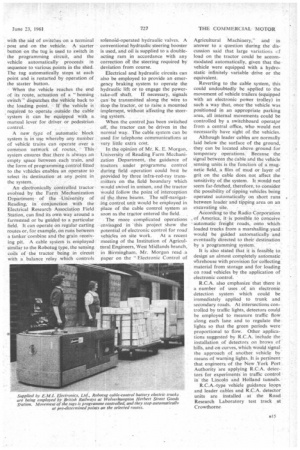
If you've noticed an error in this article please click here to report it so we can fix it.
Application of Electronic Control to the Farm Tractor and the Works Truck Prove the Potentialities of Automatic Movement of Goods By P. A. C. Brockington, A.M.I.Mech.E.
ELECTRONIC control of driverless works trucks is now a reality, and automatic control has been applied to the farm tractor to provide guidance of a vehicle on farm premises. Whereas the trucks are of the batteryelectric type, the tractor is driven by a diesel engine. A form of automatic tractor control is planned which will enable such a unit to be used for normal work in the field without a driver.
These successful applications of electronic control to farm tractors and industrial trucks may be indicative of developments in the fairly near future of far-reaching importance to the roadvehicle industry.
Many years ago it was forecast by electronic engineers that a road network would eventually be established that would provide automatic control of vehicles running at high speeds over Jong distances .which would enable the driver to relinquish control, or the vehicle to be guided to a terminal, without a driver.
It is not necessary, however, to take n14
this long-term view to appreciate the more immediate scope of electronic control in the organization of internal vehicle movements in warehouses and depots and, of possibly greater interest, the control of electronically operated tugs for movements of vehicle trailers and so on at termini. It is significant that, compared with the guidance of a tractor engaged in field operations, the automatic -control of vehicles in.a depot would be relatively simple.
Introduced last year by British Railways. at Wolverhampton, HeiVrt Street Goods Station, a pilot scheifie has been successfully operated whereb.y a number of Robotugs, supplied hy E.M.I. Electronics, Ltd., are automatically controlled to perform a series of movements in the railslieds. This affords a considerable reduction in the manpower required and many operational advantages.
A total of five Robotugs is employed and the vehicles are guided by cables, laid 4in. below ground surface, which are energized by an alternating current of -Aof an amp. of specified frequency. each section comprising a single cable. The magnetic field created by the current induces a voltage in two sensing coils located under the tug,and this is amplified by-a two-stage transistor unit. A reversible motor is connected to the steering linkage, and if the tug deviates from the course the voltage in one of the coils is increased, which causes the motor to actuate the steering in the appropriate direction to provide the necessary corrective. In the event of current failure or breakaway of the tug the brakes are auto, matically applied._ A spring-loaded safety bumper onthe front of the vehicle is fitted with a micro-switch. which opens the traction motor circuit if the tug encounters an obstruction. and the vehicle is brought to rest. Operating speed of the tug is 2 m.p,h, Tug movements are controlled by a series of switches, connected to an electronic programming unit, actuation of which selects the route to be taken and the stopping points.
In a typical operation the tug is reversed into position in front of a number of loaded trolleys and automatically coupled to the leading trolley with the aid of switches on a terminal Post and on the vehicle. A starter button on the tug is used to switch in the programming circuit, and the vehicle automatically proceeds in sequence to various points in the shed. The tug automatically stops at each point and is restarted by operation of the starter button.
When the vehicle reaches the end of its route, actuation of a "homing switch" dispatches the vehicle back to the loading point. If the vehicle is . required to operate outside the cable system it can be equipped with a manual lever for driver or pedestrian control.
A new type of automatic block system is in use whereby any number of vehicle trains can operate over a common network of routes. This system ensures that there is always an empty space between each train, and the form of programming control fitted to the vehicles enables an operator to select its destination at any point in the system.
An electronically controlled tractor evolved by the Farm Mechanization Department, of the University of Reading, in conjunction with the Electrical Research Association Field Station, can find its own way around a farmstead or be guided to a particular field. It can operate on regular carting routes or, for example, on runs between a tanker combine and the grain receiving pit. A cable system is employed similar to the Robotug type, the sensing coils of the tractor being in circuit with a balance relay which controls
solenoid-operated hydraulic valves. A conventional hydraulic steering booster is used, and oil is supplied to a doubleacting ram in accordance with any correction a the steering required by deviation from course.
Electrical and hydraulic circuits can also be employed to provide an emergency braking system to operate the hydraulic lift or to engage the power . take-off shaft. If necessary, signals can be transmitted along the wire to stop the tractor, or to raise a mounted implement, without affecting the steering system.
When the control ,has been switched off, the tractor can be driven in the normal way. The cable system can be used for telephone communications at very little extra cost.
In the opinion of Mr. K. E. Morgan. University of Reading Farm Mechanization Department, the guidance of tractors under programme control during field operation could best be provided by three infra-red-ray transmitters on the field boundary which would swivel in unison, and the tractor would follow the point of interception of the three beams. The self-navigating control unit would be employed in place of the cable control system as soon as the tractor entered the field. .
The more complicated operations envisaged in this project show the potential of electronic control for road vehicles on site work. At a recent meeting of the Institution of Agricultural Engineers, West Midlands branch, in Birmingham. Mr. Morgan read a paper on the " Electronic Control of Agricultural Machinery," and in answer to a question during the discussion said that large variations ef load on the tractor could be accommodated automatically, given that the vehicle were equipped with a hydrostatic infinitely variable drive or the equivalent.
Reverting to the cable system, this could undoubtedly be applied to the movement of vehicle trailers (equipped with an electronic power trolley) in such a way that, once the vehicle was positioned in an appropriate parking area, all internal movements could be controlled by a switchboard operator from a central office, who would not necessarily have sight of the vehicles.
Although leader cables are normally laid below the surface of the ground, they can be located above ground for temporary operations. Because the signal between the cable and the vehicle sensing units is the function of a magnetic field, a film of mud or layer of grit on the cable does not affect the sensitivity of the system. It would not seem far-fetched, therefore, to consider the possibility of tipping vehicles being operated automatically on short runs , between loader and tipping area on an excavating site. • According to the Radio Corporation of America, it is possible to conceive automatic freight roads, onto which loaded trucks from a marshalling. yard would be guided automatically and eventually directed to their destination
by a programming. system. '
It is also stated that it is feasible to design an almost completely automatic wIrehouse with provision for coflecting material from storage and for loading on road vehicles by the application of electronic control. '
R.C.A. also emphasize that 'there is a number of uses of an electronic. detection system which could be immediately applied to trunk and secondary roads. At intersections controlled by traffic lights, detectors could be employed to measure traffic flow along each lane and to regulate the lights so that the green periods were ' proportional to Row. Other applications suggested by R.C.A. include the', installation of detectors on brows of hills, and on curves, which would signal: the approach of another vehicle by means of warning lights. It is pertinent • that engineers of the New ,York Port Authority are applying R.C.A. detectors for experiments in traffic control in the Lincoln and Holland tunnels.
R.C.A.-type vehicle guidance loops and leader cables and R.C.A. detector units are installed at the Road Research Laboratory test track at Crowthorne