PRECISION WORK
Page 50
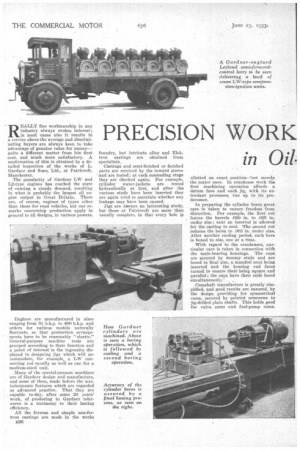
Page 51
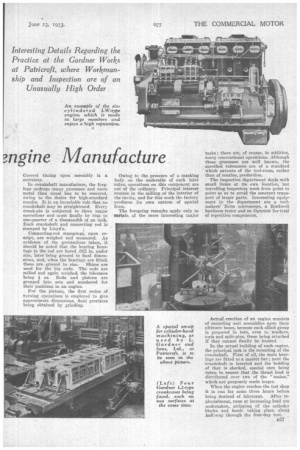
If you've noticed an error in this article please click here to report it so we can fix it.
inOil! ?ngine Manufacture
EAT.,LY fine workmanship in any industry always evokes interest; in most cases also it results in a service above the average and discriminating buyers are always keen to take advantage of genuine value for money— quite a different matter from low first cost, and much more satisfactory. A confirmation of this is obtained by a detailed inspection of the works of L. Gardner and Sons, Ltd., at Patrieroft, Manchester.
The popularity of Gardner LW and L2-type engines has reached the state of causing a steady demand, resulting in what is probably the largest oil engine output in Great Britain. There are, of course, engines of types other than those for road vehicles, but our remarks concerning production apply in general to all designs, in various powers.
Engines are manufactured in sizes ranging from 9i blip, to 400 b.h.p. and orders for various models naturally fluctuate, so that production arran-gements have to he reasonably "elastic." General-purpose machine tools are grouped according to their function and a point Of interest is the ingenuity displayed in designing jigs which will accommodate, for example, a LW connecting rod equally as well as one for a medium-sized unit.
Many of the special-purpose machines are of Gardner design and manufacture, and some of them, made before the war, incorporate features which are regarded as advanced practice. That they are capable to-day, after some 20 years' work, of producing to Gardner tolerances is a testimony to their lasting efficiency.
All the ferrous and simple non-ferrous castings are made in the works B36
foundry, but intricate alloy and Elektron castings are obtained from specialists.
Castings and semi-finished or finished parts are received by the inward stores and are tested ; at each succeeding stage they are checked again. For example, cylinder water-jackets are tested hydraulically at first, and after the various studs have been inserted they are again tried to ascertain whether any leakage may have been caused.
Jigs are always an interesting study, but those at Patricroft are more than usually complete, in that every bole is
allotted an exact position—tnot merely the major ones. In crankcase work the first machining operation affords a datum face and each jig, with its attendant processes, ties up to its predecessor.
In preparing the cylinder bores great care is taken to ensure freedom from distortion. For example, the first cut leaves the barrels .020 in. to .025 in. under size ; next an interval is allowed for the casting to cool. The second cut reduces the bores to .003 in. under size. After another cooling period, each bore is honed to size, one at a time.
With regard to the crankcases, particular care is taken in connection with the main-hearing housings. The caps are secured by dummy studs and are bored to final size, a mandrel next being inserted and the housing end faces turned to ensure their being square and parallel; the caps have their ends faced simultaneously. ,
Camshaft manufacture is greatly simplified, and good results are ensured, by the design providing for symmetrical cams, secured by pointed setscrews to jig-drilled plain shafts. This holds good for valve cams and fuel-pump Caine.
Correct timing upon assembly is a certainty.
In crankshaft manufacture, the forgings undergo many processes and more metal than usual has to he removed, owing to the desire for high-standard results. It is an invariable rule that no crankshaft may be straightened. Every crank-pin is subjected to three major operations and must finally be titre to one-quarter of a thousandth of an inch. Each crankshaft and connecting rod is stamped by Lloyd's.
Connecting-rod stampings, upon receipt, are weighed and measured. As evidence of the precautions taken, it should he noted that the bearing housings in the rod are bored .012 in. under size, later being ground to final dimensions, and, when the bearings are fitted, these are ground to size. Shims are used for the big ends. The rods are milled and again weighed, the tolerance being oz. Rods and pistons are grouped into sets and numbered for their positions in an engine.
For the pistons, the first series of turning operations is employed to give approximate dimensions, final precision being obtained by grinding. Owing to the presence of a masking body on the •underside of each inlet valve, operations on this component are out of the ordinary. Principal interest centres in the milling of the interior of the cavity, and for this work the factory produces its own cutters of special form.
The foregoing remarks, apply only to Certain of the more interesting major tasks ; there are, Of course, in addition, many conventional operations. Although these processes are well known, the specified tolerances are of a standard which savours of the tool-room, rather than of routine, production.
The inspection department deals with small items at its own location, but travelling inspectors work from point to point so as to avoid the constant transport of larger parts. Interesting equip-• ment in the department are a toolmakers' 'Zeiss microscope, a Rockwell . hardness tester and an Optotest for trial of repetition components.
Actual erection of an engine consists of mounting unit assemblies upon their ultimate bases, because each allied group is prepared in tote, even to washers, .nuts and split-pins, these being attaithed if they cannot finally be located.
In the actual building of each engine. the principal task is the mounting of the craaltshaft. First of all, the main bearings are fitted to a master bar ; next the crankshaft is inserted and the bedding of that is checked, special care being taken to ensure that the thrust load is distributed over two of the "mains," which are purposely made larger.
When the engine reaches the test shop it is run for some three hours before being drained of lubricant. After replenishment, runs at increasing load are undertaken, stripping of the cylinder blocks and heads taking place about half-way through the four-day test,
• B37