CONCRETE FORA ROAD IN A HURRY
Page 42
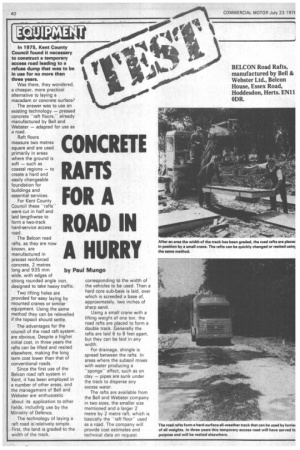
If you've noticed an error in this article please click here to report it so we can fix it.
by Paul Mungo
In 1975, Kent County Council found it necessary to construct a temporary access road leading to a refuse dump that was to be in use for no more than three years.
Was there, they wondered, a cheaper, more practical alternative to laying a macadam or concrete surface?
The answer was to use an existing technology — pressed concrete ''raft floors," already manufactured by Bell and Webster — adapted for use as a road.
Raft floors measure two metres square and are used primarily in areas where the ground is soft — such as coastal regions — to create a hard and easily changeable foundation for buildings and essential services.
For Kent County Council these "rafts" were cut in half and laid lengthwise to form a two-track hard-service access road.
The Belcon road rafts, as they are now known, are manufactured in precast reinforced concrete, 2 metres long and 935 mm wide, with edges of strong rounded angle iron, designed to take heavy traffic.
Two lifting holes are provided for easy laying by mounted cranes or'similar equipment. Using the same method they can be relevelled if the topsoil should settle.
The advantages for the council of the road raft system are obvious. Despite a higher initial cost, in three years the rafts can be lifted and resited elsewhere, making the long term cost lower than that of conventional roads.
Since the first use of the Belcon road raft system in Kent, it has been employed in a number of other areas, and the management of Bell and Webster are enthusiastic -about its application to other fields, including use by the Ministry of Defence.
The technology of laying a raft road is'relatively simple. First, the land is graded to the width of the track, corresponding to the width of the vehicles to be used. Then a hard core sub-base is laid, over which is screeded a base of, approximately, two inches of sharp sand.
Using a small crane with a lifting weight of one ton, the road rafts are placed to form a double track. Generally the rafts are laid 6 to 8 feet apart, but they can be laid in any width.
For drainage, shingle is spread between the rafts. In areas where the subsoil mixes with water producing a "sponge" effect, such as on clay — pipes are sunk under the track to disperse any excess water.
The rafts are available from the Bell and Webster company in two sizes, the smaller size mentioned and a larger 2 metre by 2 metre raft, which is basically the "raft floor" used as a road. The company will provide cost estimates and technical data on request.