• Since its introduction in April 1986 the number of
Page 115
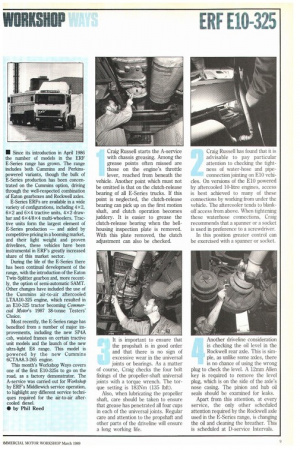
Page 116
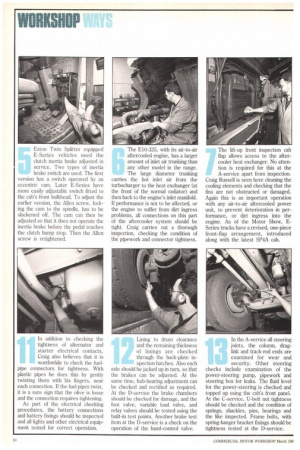
Page 117
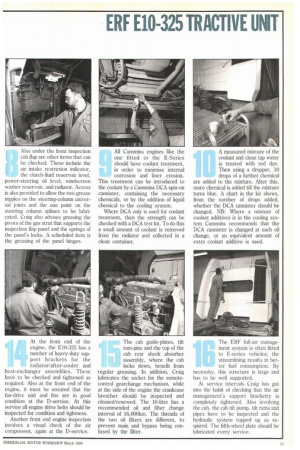
If you've noticed an error in this article please click here to report it so we can fix it.
models in the ERF E-Series range has grown. The range includes both Cummins and Perkinspowered variants, though the bulk of E-Series production has been concentrated on the Cummins option, driving through the well-respected combination of Eaton gearboxes and Rockwell axles.
E-Series ERFs are available in a wide variety of configurations, including 4 x 2, 6x2 and 6x4 tractive units, 4x2 drawbar and 6x 4/8 x 4 multi-wheelers. Tractive units form the largest element of E-Series production — and aided by competitive pricing in a booming market, and their light weight and proven drivelines, these vehicles have been instrumental in ERF's greatly increased share of this market sector.
During the life of the E-Series there has been continual development of the range, with the introduction of the Eaton Twin-Splitter gearbox and, more recently, the option of semi-automatic SAMT. Other changes have included the use of the Cummins air-to-air aftercooled LTAA10-325 engine, which resulted in an E10-325 tractor becoming Commercial Motor's 1987 38-tonne Testers' Choice.
Most recently, the E-Series range has benefited from a number of major improvements, including the new SP4A cab, waisted frames on certain tractive unit models and the launch of the new ultra-light E8 range. This model is powered by the new Cummins 6CTAA8.3-265 engine.
This month's Workshop Ways covers one of the first E10-325s to go on the road, as a factory demonstrator. The A-service was carried out for Workshop by ERF's Middlewich service operation, to highlight any different service techniques required for the air-to-air aftercooled diesel.
• by Phil Reed Craig Russell starts the A-service with chassis greasing. Among the grease points often missed are those on the engine's throttle lever, reached from beneath the vehicle. Another point which must not be omitted is that on the clutch-release bearing of all E-Series trucks. If this point is neglected, the clutch-release bearing can pick up on the first motion shaft, and clutch operation becomes juddery. It is easier to grease the clutch-release bearing when the bellhousing inspection plate is removed. With this plate removed, the clutch adjustment can also be checked.
It is important to ensure that the propshaft is in good order and that there is no sign of excessive wear in the universal joints or bearings. As a matter of course, Craig checks the four bolt fixings of the propeller-shaft universal joints with a torque wrench. The torque setting is 183Nm (135 Mt).
Also, when lubricating the propeller shaft, care should be taken to ensure that grease has penetrated all four cups in each of the universal joints. Regular care and attention to the propshaft and other parts of the clriveline will ensure a long working life. Craig Russell has found that it is advisable to pay particular attention to checking the tightness of water-hose arid pipeconnection jointing on El0 vehi cles. On versions of the El0 powered by aftercooled 10-litre engines, access is best achieved to many of these connections by working from under the vehicle. The aftercooler tends to blankoff access from above. When tightening these waterhose connections, Craig recommends that a spanner or a socket is used in preference to a screwdriver.
In this position greater control can be exercised with a spanner or socket.
Another driveline consideration is checking the oil level in the Rockwell rear axle. This is simple, as unlike some axles, there is no chance of using the wrong plug to check the level A 12mm Allen key is required to remove the level plug, which is on the side of the axle's nose casing. The pinion and hub oil seals should be examined for leaks.
Apart from this attention, at every service, the only other scheduled attention required by the Rockwell axle used in the E-Series range, is changing the oil and cleaning the breather. This is scheduled at D-service Intervals. Eaton Twin Splitter equipped E-Series vehicles need the clutch inertia brake adjusted in service. Two types of inertia brake switch are used. The first version has a switch operated by an eccentric cam. Later E-Series have more easily adjustable switch fitted to the cab's front bulkhead. To adjust the earlier version, the Allen screw, locking the cam to the spindle, has to be slackened off. The cam can then be adjusted so that it does not operate the inertia brake before the pedal reaches the clutch bump stop. Then the Allen screw is retightened. The E10-325, with its air-to-air aftercooled engine, has a larger amount of inlet air trunking than any other model in the range. The large diameter trunking carries the hot inlet air from the turbocharger to the heat exchanger (at the front of the normal radiator) and then back to the engine's inlet manifold. If performance is not to be affected, or the engine to suffer from dirt ingress problems, all connections on this part of the aftercooler system should be tight. Craig carries out a thorough inspection, checking the condition of the pipework and connector tightness. The lift-up front inspection cab flap allows access to the after cooler heat exchanger. No atten tion is required for this at the A-service apart from inspection. Craig Russell is seen here cleaning the cooling elements and checking that the fins are not obstructed or damaged. Again this is an important operation with any air-to-air aftercooled power unit, to prevent deterioration in performance, or dirt ingress into the engine. As of the Motor Show, ESeries trucks have a revised, one-piece front-flap arrangement, introduced along with the latest SP4A cab. Also under the front inspection cab flap are other items that can be checked. These include the air intake restriction indicator, the clutch-fluid reservoir level, power-steering oil level, windscreen washer reservoir, and radiator. Access is also provided to allow the two grease nipples on the steering-column universal joints and the one point on the steering column splines to be lubricated. Craig also advises greasing the pivots of the gas strut that supports the inspection flap panel and the springs of the panel's locks. A scheduled item is the greasing of the panel hinges. All Cummins engines like the one fitted to the E-Series should have coolant treatment, in order to minimise internal corrosion and liner erosion.
This treatment can be introduced to the coolant by a Cummins DCA spin-on cannister, containing the necessary chemicals, or by the addition of liquid chemical to the cooling system.
Where DCA only is used for coolant treatment, then the strength can be checked with a DCA test kit. To do this a small amount of coolant is removed from the radiator and collected in a clean container. A measured mixture of the coolant and clean tap water is treated with red dye. Then using a dropper, 10 drops of a further chemical are added to the mixture. After this, more chemical is added till the mixture turns blue. A chart in the kit shows, from the number of drops added, whether the DCA cannister should be changed. NB: Where a mixture of coolant additives is in the cooling system Cummins recommends that the DCA cannister is changed at each oil change, or an equivalent amount of extra coolant additive is used.
In addition to checking the tightness of alternator and starter electrical contacts, Craig also believes that it is worthwhile to check the fuel pipe connectors for tightness. With plastic pipes he does this by gently twisting them with his fingers, near each connection. If the fuel pipes twist, it is a sure sign that the olive is loose and the connection requires tightening.
As part of the electrical checking procedures, the battery connections and battery fixings should be inspected and all lights and other electrical equipment tested for correct operation. Lining to drum clearance and the remaining thickness of linings are checked through the back-plate inspection hatches. Also each axle should be jacked up in turn, so that the brakes can be adjusted. At the same time, hub-bearing adjustment can be checked and rectified as required. At the D-service the brake chambers should be checked for damage, and the foot valve, variable load valve, and relay valves should be tested using the built-in test points. Another brake test item at the D-service is a check on the operation of the hand-control valve. In the A-service all steering joints, the column, draglink and track-rod ends are examined for wear and security. Other steering checks include examination of the power-steering pump, pipework and steering box for leaks. The fluid level for the power-steering is checked and topped up using the cab's front panel. At the C-service, U-bolt nut tightness should be checked and the condition of springs, shackles, pins, bearings and the like inspected. Frame bolts, with spring-hanger bracket fixings should be tightness tested at the D-service. At the front end of the engine, the E10-325 has a number of heavy-duty support brackets for the radiator/after-cooler and heat-exchanger assemblies. These have to be checked and tightened as required. Also at the front end of the engine, it must be ensured that the fan-drive unit and fins are in good condition at the D-service. At this service all engine drive belts should be inspected for condition and tightness.
Another front end engine inspection involves a visual check of the air compressor, again at the D-service. The cab guide-plates, tilt ram-pins and the top of the cab rear shock absorber assembly, where the cab locks down, benefit from regular greasing. In addition, Craig lubricates the socket for the remotecontrol gearchange mechanism, while at the side of the engine the crankcase breather should be inspected and cleaned/renewed. The 10-litre has a recommended oil and filter change interval of 16,000Iun. The threads of the two oil filters are different, to prevent main and bypass being confused by the filter. The ERF full-air management system is often fitted to E-series vehicles; the streamlining results in better fuel consumption. By necessity, this structure is large and has to be well supported.
At service intervals Craig has got into the habit of checking that the air management's support bracketry is completely tightened. Also involving the cab, the cab tilt pump, tilt rams and pipes have to be inspected and the hydraulic system topped up as required. The fifth-wheel plate should be lubricated every service.