What the papers say
Page 53
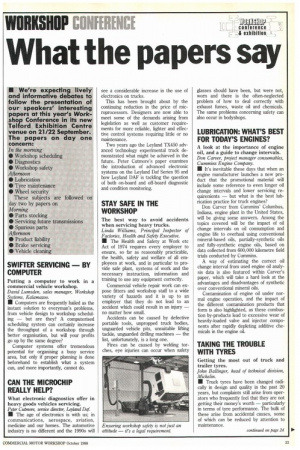
Page 54
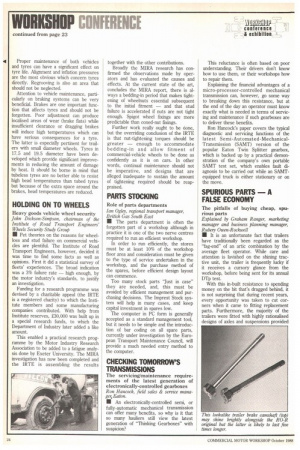
Page 55
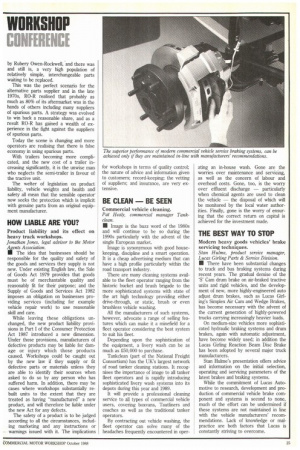
If you've noticed an error in this article please click here to report it so we can fix it.
SWIFTER SERVICING BY COMPUTER
Putting a computer to work in a commercial vehicle workshop.
David Lumsden, sales manager, Workshop Systems, Kalamazoo_ • Computers are frequently hailed as the instant solution to everyman's problems, from vehicle design to workshop scheduling — but are they? A computerised scheduling system can certainly increase the throughput of a workshop through better organisation, but will your profits go up by the same degree?
Computer systems offer tremendous potential for organising a busy service area, but only if proper planning is done beforehand to establish what a system can, and more importantly, cannot do.
CAN THE MICROCHIP REALLY HELP?
What electronic diagnostics offer in heavy goods vehicles servicing. Peter Cutniore, service director, Leyland Daf ▪ The age of electronics is with us; in communications, aerospace, aviation, medicine and our homes. The automotive industry is no different and the 1990s will
see a considerable increase in the use of electronics on trucks.
This has been brought about by the continuing reduction in the price of microprocessors. Designers are now able to meet some of the demands arising from legislation as well as customer requirements for more reliable, lighter and effective control systems requiring little or no maintenance.
Two years ago the Leyland TX450 advanced technology experimental truck demonstrated what might be achieved in the future. Peter Cutmore's paper examines the introduction of advanced electronic systems on the Leyland Daf Series 95 and how Leyland DAF is tackling the question of both on-board and off-board diagnostic and condition monitoring.
STAY SAFE IN THE WORKSHOP
The best way to avoid accidents when servicing heavy trucks.
Linda Williams, Principal Inspector of Factories, Health and Safety Executive. • The Health and Safety at Work etc Act of 1974 requires every employer to ensure, so far as reasonably practicable, the health, safety and welfare of all employees at work, and in particular to provide safe plant, systems of work and the necessary instruction, information and training to use any equipment correctly.
Commercial vehicle repair work can expose fitters and workshop staff to a wide variety of hazards and it is up to an employer that they do not lead to an accident which could result in an injury — no matter how small.
Accidents can be caused by defective portable tools, unpropped truck bodies, unguarded vehicle pits, unsuitable lifting tackle, unguarded drilling machines — the list, unfortunately, is a long one.
Fires can be caused by welding torches, eye injuries can occur when safety glasses should have been, but were not, worn and there is the often-neglected problem of how to deal correctly with exhaust fumes, waste oil and chemicals. The same problems concerning safety can also occur in bodyshops.
LUBRICATION: WHAT'S BEST FOR TODAY'S ENGINES?
A look at the importance of engine oil, and a guide to change intervals. Don Carver, project manager consumables, Cummins Engine Company.
• It's inevitable these days that when an engine manufacturer launches a new pro duct that the promotional material will include some reference to even longer oil change intervals and lower servicing requirenients — but what is the best lubrication practice for truck engines?
Don Carver from Cummins' Columbus, Indiana, engine plant in the United States, will be giving some answers. Among the topics covered will be the impact of oil change intervals on oil consumption and engine life to overhaul using conventional mineral-based oils, partially-synthetic oils and fully-synthetic engine oils, based on data collected from 600,000 kilometre field trials conducted by Cummins.
A way of estimating the correct oil change interval from used engine oil analy sis data is also featured within Carver's paper, which will take a hard look at the advantages and disadvantages of synthetic over conventional mineral oils.
Contamination of engine oil under normal engine operation, and the impact of the different contamination products that form is also highlighted, as these combustion by-products lead to excessive wear of heavily-loaded valve and injector components after rapidly depleting additive chemicals in the engine oil.
TAKING THE TROUBLE WITH TYRES
Getting the most out of truck and trailer tyres.
John Ballinger, head of technical division, Michelin.
• Truck tyres have been changed radically in design and quality in the past 20 years, but complaints still arise from operators who frequently feel that they are not getting their money's worth — particularly in terms of tyre performance. The bulk of these arise from accidental causes, some of which can be reduced by attention to maintenance. Proper maintenance of both vehicles and tyres can have a significant effect on tyre life. Alignment and inflation pressures are the most obvious which concern tyres directly. Regrooving is also an area that should not be neglected.
Attention to vehicle maintenance, particularly on braking systems can be very beneficial. Brakes are one important function that affects tyres and should not be forgotten. Poor adjustment can produce localised areas of wear (brake flats) while insufficient clearance or dragging brakes will induce high temperatures which can have serious consequences for a tyre. The latter is especially pertinent for trailers with small diameter wheels. Tyres in 17.5 and 19.5 diameter have been developed which provide significant improvements in reducing the amount of damage by heat. It should be borne in mind that tubeless tyres are no better able to resist high bead temperatures than tubed tyres but because of the extra space around the brakes, head temperatures are reduced.
HOLDING ON TO WHEELS
Heavy goods vehicle wheel security John Dickson-Simpson, chairman of the Institute of Road Transport Engineers' Wheels Security Study Group • Pet theories on the reasons for wheelloss and stud failure on commercial vehicles are plentiful. The Institute of Road Transport Engineers, however, decided it was time to find some facts as well as opinions. First it did a statistical survey of fleets' experiences. The broad indication was a 3% failure rate — high enough, by the motor industry's standards, to justify an investigation.
Funding for a research programme was devised by a charitable appeal (the IRTE is a registered charity) to which the Institute members and some manufacturing companies contributed. With help from Institute reserves, 2.30,000 was built up in a special research funds, to which the Department of Industry later added a like amount.
This enabled a practical research programme by the Motor Industry Research Association to be added to a fatigue analysis done by Exeter University. The MIRA investigation has now been completed and the IRTE is assembling the results together with the other contributions.
Broadly the MIRA research has confirmed the observations made by operators and has evaluated the causes and effects. At the current state of the art, concludes the MIRA report, there is always a bedding-in period that makes tightening of wheelnuts essential subsequent to the initial fitment — and that stud failure is accelerated if nuts are not tight enough. Spigot wheel fixings are more predictable than coned-nut fixings.
Further work really ought to be done, but the overriding conclusion of the IRTE is that nut-tightening torques should be greater — enough to accommodate bedding-in and allow fitment of commercial-vehicle wheels to be done as confidently as it is on cars. In other words, continual maintenance should not be imperative, and designs that are alleged inadequate to sustain the amount of tightening required should be reappraised.
PARTS STOCKING
Role of parts departments Ian Ogley, regional transport manager, British Gas South East • The parts department is often the forgotten part of a workshop although in practice it is one of the two nerve centres required to run an efficient workshop.
In order to run efficiently, the stores must be at least 10% of the workshop floor area and consideration must be given to the type of service undertaken in the workshop, and the purchase method of the spares, before efficient design layout can commence.
Too many stock parts "Just in case" they are needed, and, this must be avoided by efficient management and purchasing decisions. The Imprest Stock system will help in many cases, and keep capital investment in spares low.
The computer in PC form is generally accepted as a standard management tool, but it needs to be simple and the introduction of bar coding on all spare parts, currently under investigation by the European Transport Maintenance Council, will provide a much needed entry method to the computer.
CHECKING TOMORROW'S TRANSMISSIONS
The servicing/maintenance requirements of the latest generation of electronically-controlled gearboxes Ron Hancock, field sales & service manager, Eaton.
• An electronically-controlled semi, or fully-automatic mechanical transmission can offer many benefits, so why is it that so many hauliers still view the latest generation of "Thinking Gearboxes" with suspicion? This reluctance is often based on poor understanding. Their drivers don't know how to use them, or their workshops how to repair them.
Explaining the financial advantages of a micro-processor-controlled mechanical transmission can, however, go some way to breaking down this resistance, but at the end of the day an operator must know exactly what is needed in terms of servicing and maintenance if such gearboxes are to deliver these benefits.
Ron Hancock's paper covers the typical diagnostic and servicing functions of the latest Semi-Automated-MechanicalTransmission (SAMT) version of the popular Eaton Twin Splitter gearbox, which is backed up by a practical demonstration of the company's own portable SAMT test set, which enables fault diagnosis to be carried out while an SAMTequipped truck is either stationary or on the move.
SPURIOUS PARTS A FALSE ECONOMY
The pitfalls of buying cheap, spurious parts Explained by Graham Ranger, marketing manager and business planning manager, Rubery Owen-Rockwell • It is an unfortunate fact that trailers have traditionally been regarded as the "fag-end" of an artic combination by the average fleet operator. While care and attention is lavished on the shining tractive unit, the trailer is frequently lucky if it receives a cursory glance from the workshop, before being sent for its annual DTp test.
With this in-built resistance to spending money on the bit that's dragged behind, it is not surprising that during recent years, every opportunity was taken to cut corners when it came to fitting replacement parts. Furthermore, the majority of the trailers were fitted with highly rationalised designs of axles and suspensions provided
by Rubery Owen-Rockwell, and there was and still is, a very high population of relatively simple, interchangeable parts waiting to be replaced.
This was the perfect scenario for the alternative parts supplier and in the Late 1970s, RO-R realised that probably as much as 80% of its aftermarket was in the hands of others including many suppliers of spurious parts. A strategy was evolved to win back a reasonable share, and as a result RO-R has gained a wealth of experience in the fight against the suppliers of spurious parts.
Today the scene is changing and more operators are realising that there is false economy in using spurious parts.
With trailers becoming more complicated, and the new cost of a trailer increasing significantly, it is the unwise man who neglects the semi-trailer in favour of the tractive unit.
The welter of legislation on product liability, vehicle weights and health andl safety all mean that the sensible operator now seeks the protection which is implicit: with genuine parts from an original equipment manufacturer.
HOW LIABLE ARE YOU?
Product liability and its effect on heavy truck workshops.
Jonathan Jones, legal advisor to the Motor 4. ents Association.
• The idea that businesses should he responsible for the quality and safety of the goods and services they supply is not new. Under existing English law, the Sale of Goods Act 1979 provides that goods must be of merchantable quality and reasonably fit for their purpose; and the Supply of Goods and Services Act 1982 imposes an obligation on businesses providing services (including for example vehicle repair work) to use reasonable skill and care.
While leaving these obligations unchanged, the new product liability provisions in Part I of the Consumer Protection Act 1987 introduced a new dimension. Under those provisions, manufacturers of defective products may be liable for damage or injury which those products caused. Workshops could be caught out by the new law if they supply or fit defective parts or materials unless they are able to identify their sources when asked to do so by any person who has suffered harm. In addition, there may be cases where workshops substantially rebuilt units to the extent that they are treated as having "manufactured" a new product, and will therefore be liable under the new Act for any defects.
The safety of a product is to be judged according to all the circumstances, including marketing and any instructions or — warnings issued with it. The implications for workshops in terms of quality control; the nature of advice and information given to customers; record-keeping; the vetting of suppliers; and insurance, are very extensive.
BE CLEAN BE SEEN
Commercial vehicle cleaning.
Pat Healy, commercial manager Tankclean.
• Image is the buzz word of the 1980s and will continue to be so during the 1990s particularly with the advent of the single European market.
Image is synonymous with good housekeeping, discipline and a smart operation. It is a cheap advertising medium that can have a high profile particularly within the road transport industry.
There are many cleaning systems available to the fleet operator ranging from the historic bucket and brush brigade to the more sophisticated systems with state of the art high technology providing either drive-through, or static, brush or even brushless vehicle washing.
All the manufacturers of such systems, however, advocate a range of selling features which can make it a minefield for a fleet operator considering the best system to suit his fleet.
Depending upon the sophistication of the equipment, a livery wash can be as much as £50,000 to purchase.
Tankclean (part of the National Freight Consortium) has the UK's largest network of road tanker cleaning stations. It recognises the importance of image to all tanker fleet operators and is rapidly introducing sophisticated livery wash systems into its depots during this year and 1989.
It will provide a professional cleaning service to all types of commercial vehicle users, covering boxvans, Tautliners and coaches as well as the traditional tanker operators.
By contracting out vehicle washing, the fleet operator can solve many of the headaches frequently encountered in oper ating an in-house wash. Gone are the worries over maintenance and servicing, as well as the concern of labour and overhead costs. Gone, too, is the worry over effluent discharge — particularly when chemical agents are used to clean the vehicle — the disposal of which will be monitored by the local water authorities. Finally, gone is the worry of ensuring that the correct return on capital is achieved for the investment made.
THE BEST WAY TO STOP
Modern heavy goods vehicles' brake servicing techniques.
Stan Hulme, product service manager, Lucas Girling Parts & Service Division.
• There have been substantial changes to truck and bus braking systems during recent years. The gradual demise of the 'S' Cam drum brake on air-braked tractive units and rigid vehicles, and the development of new, more highly-engineered auto adjust drum brakes, such as Lucas Girling's Simplex Air Cam and Wedge Brakes, has become necessary with the advent of the current generation of highly-powered trucks carrying increasingly heavier loads.
On medium-size vehicles more sophisticated hydraulic braking systems and drum brakes, again with automatic adjustment, have become widely used; in addition the Lucas Girling Reaction Beam Disc Brake has been adopted by several major truck manufacturers.
Stan Hultne's presentation offers advice and information on the initial selection, operating and Servicing parameters of the latest brakes and braking systems.
While the commitment of Lucas Automotive to research, development and production of commercial vehicle brake component and systems is second to none, much of the effort can be undermined if these systems are not maintained in line with the vehicle manufacturers' recommendations. Lack of knowledge or malpractice are both factors that Lucas is constantly striving to overcome.