Turbine Progress Depends on Mechanical Details
Page 96
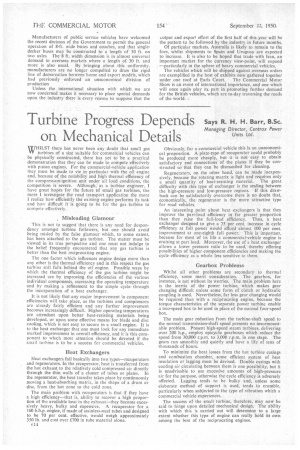
If you've noticed an error in this article please click here to report it so we can fix it.
Says R. H. H. Barr, B.Sc.
Managing Director, Centrax Power Units Ltd.
WHILST there has never been any doubt that small gas turbines of a size suitable for commercial vehicles can be physically constructed, there has yet to be a practical demonstration that they can be made to compete effectively with piston engines. For the commercial-vehicle application they must be made to vie in particular with the oil engine and, because of the reliability and high thermal efficiency of the compression-ignition unit under all load conditions, the competition is severe. Although, as a turbine engineer, I have great hopes for the future of small gas turbines, the more 1 investigate the road transport application the more I realize how efficiently the existing engine performs its task and how difficult it is going to be for the gas turbine to compete effectively.
Misleading Glamour
This is not to suggest that :here is any need for despondency amongst turbine followers, but one should avoid being misled by the false glamour which, to some extent, has been attached to the gas turbine. The matter must be viewed in its true perspective and one must not indulge in the belief frequently encountered that any gas turbine is better than the best reciprocating engine.
The one factor which influences engine design more than any other is the thermal efficiency and in this respect the gas turbine still falls behind the oil engine, Possible ways by which the thermal efficiency of the gas turbine might be increased are by improving the efficiencies of the various individual components, Increasing the operating temperature and by making a refinement to the simple cycle through the incorporation of a heat exchanger.
It is not likely that any major improvement in component efficiencies will take place, as the turbines and compressors are already fairly efficient and any further improvement becomes increasingly difficult. Higher operating temperatures are attendant upon better heat-resisting materials being developed, or upon some effective means for blade and disc cooling, which is not easy to secure in a small engine. It is to the heat exchanger that one must look for any immediate marked improvement in overall efficiency, and it is this component to which most attention should be devoted if the small turbine is to be a success for commercial vehicles.
Heat Exchangers
Heat exchangers fall basically into two types—recuperators and regenerators. In the recuperator, heat is transferred from the hot exhaust to the relatively cold compressed air directly through the thin walls of a cluster of tubes or plates. In the regenerator, the heat transfer takes place by continuously moving a heat-absorbing matrix, in the shape of a drum or disc, from the hot zone to the cold zone.
The main problem with recuperators is that if they have a high efficiency—that is, ability to recover a high proportion of thz available heat in the exhaust—they become excessively heavy, bulky and expensive. A recuperator for a 160 b.h.p. engine, if made of stainless-steel tubes and designed to be 70 per cent. effective, would weigh approximately 350 lb. and cost over £700 in tube material alone.
c14 Obviously, for a commercial vehicle this is an uneconomical proposition. A plate-type of recuperator could probably be produced more cheaply, but it is not easy to obtain satisfactory end connections of the plates if they be constructed so that they can be dismantled for cleaning.
Regenerators, on the other hand, can be made inexpensively, because the rotating matrix is light and requires only a small quantity of heat-resisting material. The great difficulty with this type of exchanger is the sealing between the high-pressure and low-pressure regions. If this drawback can be satisfactorily overcome there is no doubt that. economically, the regenerator is the more attractive type for road vehicles.
An interesting point about heat exchangers is that they Improve the part-load efficiency in far greater proportion than they raise the full-load efficiency. Thus, a heat exchanger designed to give a 25 per cent. increase in cycle efficiency at full power would afford almost 100 per cent. improvement at one-eighth full power. This is important. because for most of its life a commercial-vehicle engine is cruising at part load. Moreover, the use of a heat exchanger allows. a lower pressure ratio to be used. thereby offering possibilities of higher component efficiencies and making the cycle efficiency as a whole less sensitive to them.
Gearbox Problems,
Whilst all other problems are secondary to thermal efficiency, some merit consideration. The gearbox, for instance, is not without its worries. The main problem here is the inertia of the power turbine, which makes gear changing difficult unless some form of clutch or hydraulic coupling is used. Nevertheless, far less gear changing would be required than with a reciprocating engine, because the torque characteristics of the separate power turbine enable a two-speed box to be used in place of the normal four-speed box.
The main gear reduction from the turbine-shaft speed to the normal transmission-shaft speed presents no insurmountable problem. Present high-speed steam turbines, delivering over 200 h.p.. employ epicyclic gearboxes which reduce the speed from 30,000 r.p.m. to 3,000 r.p.m. in one stage. The gears run smoothly and quietly and have a life of tens of thousands of hours.
To minimize the heat losses from the hot turbine casings and combustion chamber, some efficient system of heat insulation or lagging must be devised. Double casings with cooling air circulating between them is one possibility, but it is unadvisable to use excessive amounts of high-pressure air for the purpose, otherwise the cycle efficiency is adversely affected. Lagging tends to be bulky and, unless some elaborate method of support is used, tends to crumble. particularly when subjected to the type of vibration which a commercial vehicle experiences.
The success of the small turbine, therefore, may now be said to hinge upon detailed mechanical design. The ability with which this is carried out will determine to a large extent whether this type of engine can really hold its own among the best of the reciprocating engines.