Novel Pit Design in Fleet Workshops
Page 43
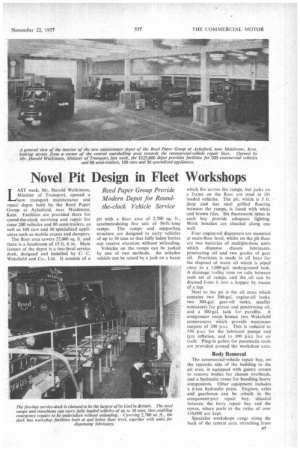
Page 44
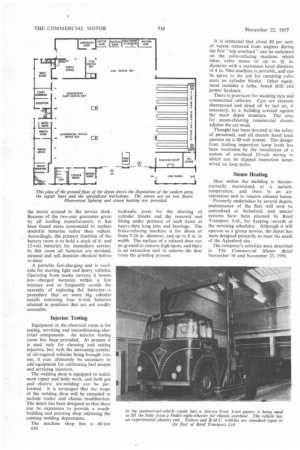
If you've noticed an error in this article please click here to report it so we can fix it.
Reed Paper Group Provide Modern Depot for Roundthe-clock Vehicle Service
LAST week. Mr. Harold Watkinson, Minister of Transport, opened a new transport maintenance and repair depot built by the Reed Paper Group at Aylesford, near Maidstone, Kent. Facilities are provided there for round-the-clock servicing and repair for some 200 vehicles and 80 semi-trailers, as well as 100 cars and 50 specialized appliances such as mobile cranes and dumpers.
The floor area covers 27,000 sq. ft. and there is a headroom of 15 ft. 6 in. Main feature of the depot is a two-level service dock, designed and installed by C. C. Wakefield and Co., Ltd. It consists of a
pit with a floor area of 2,700 sq. ft., accommodating five sets of 30-ft.-long ramps. The ramps and supporting structure are designed to carry vehicles of up to 30 tons so that fully laden lorries can receive attention without unloading.
Vehicles on the ramps can be jacked by one of two methods. An unladen vehicle can be raised by a jack on a beam which fits across the ramps, but jacks on a frame on the floor are used to lift loaded vehicles. The pit, which is 5 ft. deep and has steel grilled flooring between the ramps, is faced with white and brown tiles. Six fluorescent tubes in each bay provide adequate lighting. Work benches are situated along one wall.
Four engine-oil dispensers are mounted at main-floor level, whilst on the pit floor are two batteries of multiple-hose units which dispense chassis lubricants. penetrating oil and two grades of gear oil. Provision is made in all bays for the disposal of waste oil which is piped away to a 1.000-gal. underground tank. A drainage trolley runs on rails between each set of ramps. and the oil can be drained from it into a hopper by means of a tap.
Next to the pit is the oil store which contains two 500-gal. engine-oil tanks. two 300-gal. gear-oil tanks, smaller containers for grease and penetrating oil. and a 300-gal. tank for paraffin. A compressor room houses two Wakefield compressors which provide maximum outputs of 200 p.s.i. This is reduced to 150 p.s.i. for the lubricant pumps and tyre inflation, and to 100 p.s.i. for air tools. Plug-in points for pneumatic tools are provided around the workshop area.
Body Removal
The commercial-vehicle repair bay, on the opposite side of the building to the pit area, is equipped with gantry cranes to remove bodies for chassis overhauls, and a hydraulic crane for handling heavy components. Other equipment includes a 6-ton hydraulic press. Engines, axles and gearboxes can be rebuilt in the component-part repair bay. situated between the lorry repair bay and the stores, where parts to the value of over /10,000 are kept.
Specialist workshops range along the back of the central area. stretching from
the stores around to the service dock. Because of the two-year guarantee given by all leading manufacturers, it has been found more economical to replace doubtful batteries rather than replate. Accordingly, the primary function of the battery room is to hold a stock of 6and 12-volt batteries for immediate service. In this room all batteries are serviced, cleaned and cell densities checked before re-issue.
A portable fast-charging unit is available for starting light and heavy vehicles. Operating from mains current, it boosts low charged batteries within a few minutes and so frequently avoids the necessity of replacing flat batteries—a procedure that on some big vehicles entails removing four 6-volt batteries situated in positions that are not readily accessible.
Injector Testing
Equipment in the electrical room is for testing, servicing and reconditioning electrical components. An injector testing room has been provided. At present it is used only for cleaning and testing injectors, but, with the increasing number of oil-engined vehicles being brought int() use, it may ultimately be necessary to add equipment for calibrating fuel pump), and servicing injectors.
The welding shop is equipped to tackle most repair and body work, and both gas and electric arc-welding can be performed. It is envisaged that the scope of the welding shop will be extended to include trailer and chassis modification. The depot has been designed so that there can be expansion to provide a coachbuilding and painting shop adjoining the existing welding department.
The machine shop has a 60-ton 810 hydraulic press for the sleeving of cylinder blocks and the removal and fitting under pressure of such items as heavy-duty king pins and bearings. The brake-refacing machine is for shoes of from 7-24 in. diameter, and up to 8 in. in width. The surface of a refaced shoe can be ground to remove high spots, and there is an extraction unit to remove the dust from the grinding process. It is estimated that about 80 per cent of valves removed from engines during the first "top overhaul" can be reclaimed on the valve-refacing machine, which takes valve stems of up to +I in. diameter with a maximum head diameter of 4 in. This machine is portable, and can be taken to the job for recutting valve seats on cylinder blocks. Other equipment includes a lathe, bench drill and power hacksaw.
There is provision for washing cars and commercial vehicles. Cars are cleaned, shampooed and dried off by hot air, if necessary, in a building erected against the main depot structure. The area for steam-cleaning commercial chassis adjoins the car wash.
Thought has been devoted to the safety of personnel, and all electric hand tools operate on a 50-volt system. The danger from trailing inspection lamp leads has been overcome by the installation of a system of overhead 12-volt wiring to which can be clipped inspection lamps wired on long poles.
Steam Healing
Heat within the building is thermostatically maintained at a suitabl: temperature, and there is an airextraction unit to remove exhaust fumes.
Formerly undertaken by several depots, maintenance of the fleet will now be centralized at Aylesford, and special systems have been planned by Reed Transport, Ltd., for keeping records of the servicing schedules. Although it will operate as a group service, the depot has been designed primarily to meet the needs of the Aylesford site.
The company's activities were described in The Commercial Motor dated November 16 and November 23, 1956.