PROGRESS WITH THE DIESEL ENGINE.
Page 130
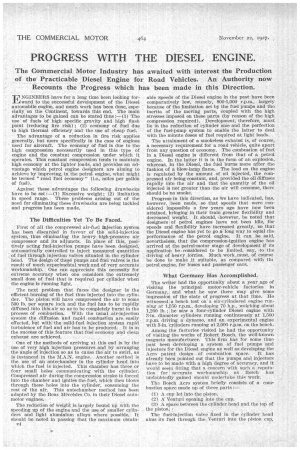
Page 131
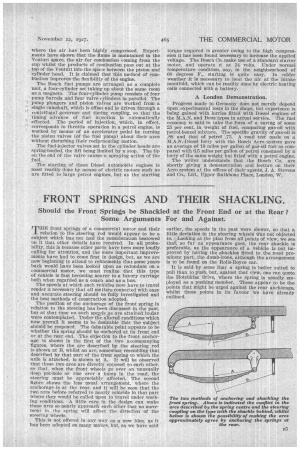
If you've noticed an error in this article please click here to report it so we can fix it.
The Commercial Motor. Industry has awaited with interest the Production of the Practicable Diesel Engine for Road Vehicles. An Authority now Recounts the Progress which has been made in this Direction.
T:iNGINEERS have for a long time been looking for
ward to the successful development of the Diesel automobile engine, and much work has been clone, especially on the Continent, towards this end. The main advantages to be gained can be stated thus:—(1) The use of fuels Of high specific gravity and high flash point (reducing fire risk) ; (2) economy of fuel due to high thermal efficiency and the use of cheap fuel.
The advantage of a reduction in fire risk applies generally, but more specifically in the case of engines used for aircraft. The economy of fuel is due to the high compression necessarily used in this type of engine and the constant compression under which it operates. This constant compression tends to maintain high economy at the lighter loads, and provides an advantage which petrol engine designers are aiming to achieve by improving, in the petrol engine, what might he termed "road fuel economy" (i.e., miles per gallon of fuel).
Against these advantages the following drawbacks have to be set :--(1) Excessive weight ; (2) limitation in speed range. These problems arising out of the need for eliminating these drawbacks are being tackled and progress has been made.
The Difficulties Yet To Be Faced. •
First of all the compressed air-fuel injection system has been discarded in favour of the solid-injection system, thus eliminating the heavy high-pressure air compressor and its adjuncts. In place of this, positively acting fuel-injection pumps have been designed, automatically controlled to inject measured quantities of fuel through injection valves situated in the cylinder head. The design of these Pumps and fuel valves is the result of much experimental work and of very accurate workmanship. One can appreciate this necessity for extreme accuracy when one considers •the extremely small dose of fuel that is required per cylinder when the engine is running light.
The next problem that faces the designer is the efficient burning of the fuel thus injected into the cylinder. The piston will have compressed the air to some 500 lb. per square inch and the fuel has to be rapidly diffused into this air so as to be completely burnt in the process of combustion. With the usual air-injection systen) the cliffusiOn and rapid combustion are easily effected, hut with' the solid-fuel injection system rapid turbulence of fuel and air has to be produced. It is in the success of this feature that fuel economy and clean exhaust are achieved.
One of the methods of arriving at this end is by the use of very high injection pressures and by arranging the angle of injection so as to cause the air to swirl, as is -instanced in the M.A:N. engine. Another method is the use of an antechamber in the cylinder head into which the fuel is injected. This chamber has three or four small holes .communicating with the cylinder. Compressed air during the compression stroke is forced into the chamber and ignites the fuel, which then blows through these holes into the cylinder, consuming the rest of the air. This antech Wilber method has been adopted by the Benz Wrcedes Co. in their Diesel automotor engines.
The reduction of weight is largely bound M.) with the speeding up of the engine and the use of smaller cylinders and light aluminium alloys where possible. It should be noted in passing that the maximum obtain
r4 able speeds of the' Diesel engine in the past have been comparatively low, namely, 800-1,000 r.p.m., largely because of the limitation set by the fuel pumps and the inertia of the moving parts, coupled with the high stresses imposed on these parts (by reason of the high compression required). Development, therefore, must lie in the reduction of cylinder size and the perfection of the fuel-pump system to enable the latter to deal with the minute doses of fuel required at light loads.
The attainment of a smokeless exhaust is, of course, a necessary requirement for a road vehicle, quite apart from any question of economy. The combustion of fuel In a Diesel engine is different from that of a petrol engine. In the latter it is in the form of an explosion, whereas, in the Diesel, the fuel burns more after the fashion of a blow-lamp flame. The load on the engine is regulated by the amount of oil injected, the compressed air being constant, and, provided the oil diffuses rapidly into the air and that the quantity of the oil injected is not greater than the air will consume, there should be no smoke.
Progress in this direction, as we have indicated, has, however, been made, so that speeds that were considered impossible a few years ago have now been attained, bringing in their train greater flexibility and decreased weight. It should, however, be noted that designers of petrol engines have not been idle, for speeds and flexibility have increased greatly, so that the Diesel engine has yet to go a long way to equal the performance of the petrol engine. It can, be said, nevertheless, that the compression-ignition engine has arrived at tile petrol-motor stage of development if its application he considered to be limited, say, to the driving of heavy lorries. Much work , must, of course be done to make it suitable, as compared with fig petrol engine, for buses and passenger cars.
What Germany Has Accomplished. .
The writer had the opportunity about a year ago of visiting the principal motor-vehicle factories in Germany, and what he saw there may give some impression of the state of progress at that time. He witnessed a bench test on a six-cylindered engine runninz at 1,250 r.p.m., developing 70 hal., weighing about 1,200 lb.; he saw a four-cylinder Diesel engine with 3-in. diameter cylinders running continuously at 1,500 r.p.m. driving a dynamo, and an. experimental engine with 3-in. 'cylinders running at 2,000 r.p.m. on the bench.
Among the factories visited he had the opportunity of visiting the works of Robert Bosch, the well-known magneto manufacturer. This firm has for some time past been developing a system of fuel pumps and injectors for the Diesel engine as well as developing the Acre patent design of combustion space. It has already been pointed out that the pumps and injectors have to be made with a high degree of accuracy, and it would seem fitting that a concern with such a reputation for accurate workmanship as Bosch has undoubtedly gained should undertake this work.
The Bosch Acre system briefly consists of a combustion space made up of three parts :— (1) A cup let into the piston.
(2) 4' Venturi opening into the cup.
(3) A space between the cylinder head and the top a the piston.
The fuel-injection valve fixed in• the Cylinder, head aims its fuel through the Venturi into the piston cup, where the air has been highly compressed. Experiments have shown that the flame is maintained in the Venturi space, the air for combustion coming from the cup whilst the products of combustion pass out at the top of the Venturi into the space between the piston and cylinder head. It is claimed that this method of corabtistion improves the flexibility of the engine.
The Bosch fuel pumps are arranged as a complete unit, a four-cylinder set taking up about the same room as a magneto. The four-cylinder pump consists of four pump barrels and four valve cylinders in parallel. The pump plungers and piston valves are worked from a single camshaft, which is offset and is driven through a centrifugal governor and timing coupling, so that the timing advance of fuel injection is automatically effected. The period of injection, which, in effect, corresponds to throttle operation in a petrol engine, is worked by means of an accelerator pedal by turning the piston valves (of the fuel pump) about their axes without disturbing their reciprocating motion.
The fuel-injector valvee set in the cylinder heads are spring-loaded, the lift being limited by a stop. The tip on the end of the valve cauSes a spraying action of the fuel.
The starting of these Diesel autoraobile engines is most readily done by means of electric motors such as are fitted to large petrol engines, but as the starting
torque required is greater owing to the high dompression it has been found necessary to increase the applied voltage. The Bosch Co. make use of a standard starter motor, and operate it at 24 volts. Under normal temperature condition, say, in the neighbourhood of 60 degrees F., starting is quite easy. In colder weather It is necesSary to heat the air at the intake manifold, which can be readily done by electric heating coils connected with a battery.
A London Demonstration.
Progress made in Germany does not merely depend upon experimental tests in the shops, but experience is being gained with lorries fitted with Diesel engines of• the M.A.N. and Benz types in actual service. The fuel economy is said to take the form of a saving of some 25 per cent. in weight of fuel, comparing gas-oil with petrol-benzol mixture. The specific gravity of gas-oil is .88 and that of petrol .75. A road test made on a M.A.N.-Diesel lorry with the Bosch Acro system gave an average of 10 miles per gallon of gas-oil fuel-as compared with 6.5 miles per gallon of petrol. consumed by a lorry of the same weight but fitted with a petrol engine.
The writer understands that the Bosch Co, are shortly giving a demonstration and lecture on their Acro system at the offices of their agents, J. A. Stevens and Co., Ltd., Upper Rathbone Place, London, W.