WORKING ON THE FRONT LINE...
Page 130

Page 131
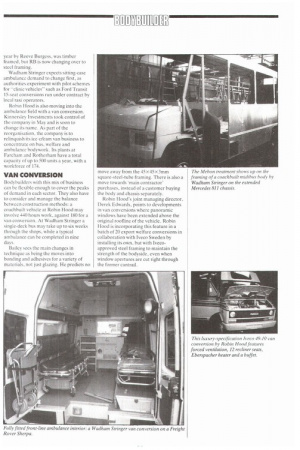
If you've noticed an error in this article please click here to report it so we can fix it.
• Mebon Coachguard anti-corrosion treatment on welded square-section steel framing is proving itself a key to the success of two south-of-England builders of buses, welfare vehicles and ambulances. Wadham Stringer Coachbuilders of Waterlooville, Hants has not had a single rust-warranty claim since it changed to the Mebon system seven years ago. "It stops electrolytic action too," says managing director Geoff Bailey.
The Mebon system is also in use at Robin Hood Vehicle Builders of Fareham. The problem, both bodybuilders find, is that applying the coating produces an atmosphere intolerable to the other workers. Robin Hood uses a separate shed for the process; at Wadham Stringer they apply the coating at night after the main workforce has left.
It seems that the result — a grey, 100micron coating designed to maintain the vehicle frame throughout its life without
rust problems is worth the trouble. Both bodybuilders rely on a mix of van conversion and coachbuilt body production, though Wadham Stringer builds extensively on larger single-deck bus and coach chassis, as well as vanderived midis and minis.
Wadham Stringer employs 250 people on two sites to produce around 500 units a year. Bodywork production, excluding the value of chassis, was worthI7 million in 1988, and the company has recently extended its range to include the Winchester 39-seater coach on the Leyland Bus Swift chassis. This uses the framing of Wadham Stringers Vanguard Two bus, but with new styling, trim and equipment. About half the body parts are shared by the coach and bus.
Wadham Stringer is also a major producer of front-line ambulances. The market for these is probably between 600 and 700 a year, and from time to time there are major export orders too. Hong Kong, for example, has adopted the distinctive British form of the ambulance, but Bailey says the company is reluctant to invest heavily in new designs till it becomes clear who will be buying what in future.
Coachbuilt front-line ambulances are glass fibre on steel framing. The competing Hanlon design, acquired last year by Reeve Burgess, was timber framed, hut RB is now changing over to steel framing.
Wadham Stringer expects sitting-case ambulance demand to change first, as authorities experiment with pilot schemes for "clinic vehicles" such as Ford Transit 15-seat conversions run under contract by local taxi operators.
Robin Hood is also moving into the ambulance field with a van conversion. Kinnersley Investments took control of the company in May and is soon to change its name. As part of the reorganisation. the company is to relinquish its ice-crseam van business to concentrate on bus, welfare and ambulance bodywork. Its plants at Fareham and Rotherham have a total capacity of up to 500 units a year, with a workforce of 174.
Bodybuilders with this mix of business can be flexible enough to cover the peaks of demand in each sector. They also have to consider and manage the balance between construction methods: a coachbuilt vehicle at Robin Hood may involve 440 hours work, against 180 for a van conversion. At Wadham Stringer a single-deck bus may take up to six weeks through the shops, while a typical ambulance can be completed in nine days.
Bailey sees the main changes in technique as being the moves into bonding and adhesives for a variety of materials, not just glazing. He predicts no move away from the 45 x 45 x 3mm square-steel-tube framing. There is also a move towards 'main contractor' purchases, instead of a customer buying the body and chassis separately.
Robin Hood's joint managing director. Derek Edwards, points to developments in van conversions where panoramic windows have been extended above the original roofline of the vehicle. Robin Hood is incorporating this feature in a batch of 20 export welfare conversions in collaboration with iveco Sweden by installing its own, but with Ivecoapproved steel framing to maintain the strength of the bodyside, even when window apertures are cut right through the former cantrail.