Care & Maintenance
Page 56
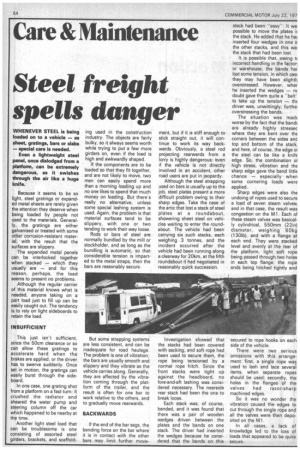
If you've noticed an error in this article please click here to report it so we can fix it.
Steel freight spells danger
WHENEVER STEEL is being loaded on to a vehicle — as sheet, gratings, bars or slabs — special care is needed.
Even a lightweight steel panel, once dislodged from a platform, can be extremely dangerous, as it swishes through the air like a huge knife.
Because it seems to be so light, steel gratings or expanded metal sheets are rarely given the attention they deserve when being loaded by people not used to the materials. Generally, the gratings are either galvanised or treated with some other corrosion-resistant material, with the result that the surfaces are slippery.
The expanded metal panels can be interlocked together when stacked — which they usually are — and for this reason, perhaps, the load seems to present no problems.
Although the regular carrier of this material knows what is needed, anyone taking on a part load just to fill up can be easily caught out. The tendency is to rely on light sideboards to retain the load.
INSUFFICIENT This just isn't sufficient, since the 50cm clearance or so can allow these gratings to accelerate hard when the brakes are applied, or the driver has to swerve suddenly. Once set in motion, the gratings can easily burst through the sideboard.
In one case, one grating shot from a platform on a fast turn: It crushed the radiator and sheared the water pump and steering column off the car which happened to be nearby at the time.
Another light steel load that can be troublesome is one consisting of assorted steel girders, brackets, and scaffold ing used in the construction industry. The objects are fairly bulky, so it always seems worth while trying to put a few more girders on, even if the load is high and awkwardly shaped.
If the components are to be loaded so that they fit together, and are not likely to move, two men can easily spend more than a morning loading up and no one likes to spend that much money on loading. But there's really no alternative, unless some special lashing system is used. Again, the problem is that material surfaces tend to be slippery, with one or two tending to work their way loose.
Rods or bars of steel are normally bundled by the mill or stockholder, and as long as the bundling is automatic, so that considerable tension is imparted to the metal straps, then the bars are reasonably secure.
But some strapping systems are less consistent, and can be inadequate for road haulage. The problem is one of vibration; the bars are usually smooth and slippery and they vibrate as the vehicle carries along. Generally, they are affected by the vibration coming through the platform of the trailer, and the result is often for one bar to work relative to the others, and to gradually move rearwards.
BACKWARDS If the end of the bar sags. the bending force on the bar where it is in contact with the other bars may limit further move
ment, but if it is stiff enough to stick straight out, it will continue to work its way backwards. Obviously, a steel rod projecting rearwards from a lorry is highly dangerous: even if the vehicle is not directly involved in an accident, other road users are put in jeopardy.
Although the steel strapping used on bars is usually up to the job, steel plates present a more difficult problem owing to their sharp edges. Take the case of the artic that lost a stack of steel plates at a roundabout, showering sheet steel on vehicles waiting to enter the roundabout. The vehicle had been carrying six such stacks, each weighing 3 tonnes, and the incident occurred after the vehicle had been running along a clearway for 20km, at the fifth roundabout it had negotiated in reasonably quick succession.
Investigation showed that the stacks had been covered with sacking, and soft rope had been used to secure them, the rope being tensioned by a normal rope hitch. Since the front stacks were tight up against the headboard, no fore-and-aft lashing was considered necessary. The nearside rear stack had been the one to break loose.
Each stack was, of course, banded, and it was found that there was a pair of wooden wedges driven between the plates and the bands on one stack. The driver had inserted the wedges because he considered that the bands on this stack had been "easy": it wa: possible to move the plates it the stack. He added that he haE inserted four wedges in one o the other stacks, and this wal the stack that had been lost.
It is possible that, owing tE incorrect handling in the facton or warehouse, the bands hac lost some tension, in which casE they may have been slightl) overstressed. However, wher he inserted the wedges — nc doubt gave them quite a -belt" to take up the tension — thE driver was, unwittingly, furthei overstressing the bands.
The situation was mad( worse by the fact that the band: are already highly stressec where they are bent over the corners between the sides anc top and bottom of the stack, and here, of course, the edge oi the steel can be like a knife edge. So, the combination ol high stress, vibration and the sharp edge gave the band little chance — especially when some cornering loads were applied.
Sharp edges were also the undoing of ropes used to secure a load of seven steam valves-, and in that case, the result was congestion on the Ml. Each of these steam valves was basically cylindrical, 550mm (22in) diameter, weighing 60kg (1301b), and with a flange at each end. They were stacked level and evenly at the rear of the platform, light soft rope being passed through two holes in each top flange, the rope ends being hitched tightly and
secured to rope hooks on each side of the vehicle.
There were two serious omissions with this arrangement: 'first, a single rope was used to lash and lace several items, when separate ropes should be used; secondly, the holes in the flanges of the valves had razor-sharp machined edges.
So it was no wonder the vibration caused the edges to cut through the single rope and all the valves were then deposited on the Ml.
In all cases, a lack of knowledge led to the loss of loads that appeared to be quite secure.