NICKEL DEPOSITION SAVES BUYING NEW PARTS.
Page 25
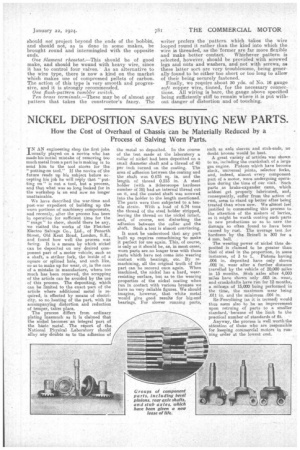
If you've noticed an error in this article please click here to report it so we can fix it.
How the Cost of Overhaul of Chassis can be Materially Reduced by a Process of Salving Worn Parts.
IN AN engineering shop the first joke asually. played on a novice who' has made his initial mistake of removing too much metal from a part he is making is to send him to the tool stores for the " putting-on 'tool." If the novice of the future reads up his subject before accepting his job he will reply that "putting on" is not a tool, but a process, and that, what was so long looked for in the workshop is an end now no longer unattainable.
We have described the war-time and post-war expedient of building up the worn portions of machinery components, and recently, after the process has been in operation for sufficient time for the " snags " to show, should there be any, we visited the works of the Fletcher Electro Salvage Co., LW. of PenarthStreet, Old Kent Road, London, S.K, and found how well the process was faring. It is a means by which nickel can be deposited on any desired component part of a. motor vehicle, such as a shaft, a striker fork, the inside of a square or splined hole, and such like, so as to make up for wear, or, in the case of a mistake in manufacture, where too much has been removed, the scrapping of the article can be avoided by the use of this process. The depositing, which can he limited to the exact part of the article where additional metal is required, is effected by means of electricity, so no heating of the part, with its accompanying distortion and reduction of temper, takes place.
The process differs from ordinary plating inasmuch as it is claimed that the nickel becomes an integral part of the basic metal. The report of the National Physical Laboratory should allay any doubts as to the adhesion of the metal so deposited. In the course of the test made at the laboratory a. collar of nickel had been deposited on a small diameter shaft and a thread of 40 per inch turned on the coating. The area of adhesion between the coating and the shaft was 0.675 sq. in. and the length of thread 0.215 in. A steel holder (with a Scleroscope hardness number of 28) had an internal thread cut on it, and the coated shaft was screwed into the holder to the length mentioned. The parts were then subjected to a tensile strain. With a load of 6.74 tons the thread of the steel holder stripped, 'leaving the thread on the nickel intact, and, of course, not disturbing the adhesion between the collar and the shaft. Such a test is almost convincing.
It must be understood that a-ny part built up requires remachining to make it perfect for use again. This, of course, is only as it should be, as, in most cases, worn parts are no longer true with those parts which have not come into wearing contact with bearings, etc. By remachining, all the original truth of the part can be secured once again. When machined, the nickel has a hard, wearresisting surface, but as to the wearing properties of the nickel coating when run in contact with various bronzes we have no very reliable figures. We should imagine, however, that white metal would give good results for big-end bearings. For slower running parts,
such as axle sleeves and stub-ends, no doubt bronze would be beat.
A great variety of articles was shown • to us, including the crankshaft of a large gas engine. Pistons which have become slack, universal joints, selector forks, and, indeed, almost every component part of a motor, were undergoing operation during the time of our visit. Such parts as brake-expander cams, which seldomi get properly lubricated, and, consequently, sutler from the action of rust, seem to stand up better after being treated than when new. We almost feel justified in commending this process to the attention of the makers of lorries, as it might be worth coating such parts in new productions so as to save the damage so often found to have been caused by rust.. The average test for hardness by the Brinell is 300 for a 4 mm. ball.
The wearing il power of nickel thus deposited is claimed to be greater than that of steel in the proportion, in some
instances, of 3 to 1. Pistons having .904 in. deposited have only shown .002 in, wear after a further distance travelled by the vehicle of 20,030 miles in 15 months. Stab axles after 4,000. miles have shown only .003 in. wear, and crankshafts have run for 12 months, a mileage of 15,000 being performed in the time, the maximum wear being .011 in. and the minimum .004 in.
Re-Fescolizing (as it is termed) would thus seem also to he an improvement upon retruing of parts to a smaller standard, because of the limit to the practical number of standards of fit.
Anyway, the process is well worth the attention of those who are responsible for keeping commercial motors in running order at the lowest cost.