Plastic pits
Page 47
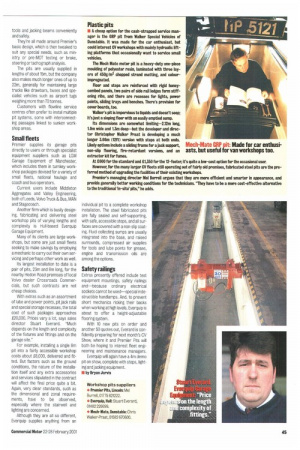
If you've noticed an error in this article please click here to report it so we can fix it.
• A cheap option for the cash-strapped service manager is the GRP pit from Walker Special Vehicles of Dunstable. It was made for the car enthusiast, but could interest CV workshops with mainly hydraulic lifting platforms that occasionally want to service small vehicles.
The Mech Mate motor pit is a heavy-duty one-piece moulding of polyester resin, laminated with three layers of 450g/m2 chopped strand matting, and colourimpregnated.
Floor and steps are reinforced with rigid honeycombed panels, two pairs of side rail ledges form stiffening ribs, and there are recesses for lights, power points, sliding trays and benches. There's provision for cover boards, too.
Walker's pit is impervious to liquids and doesn't seep; it's just a sloping floor with an easily emptied sump.
Its dimensions are somewhat limiting-212m long, 1.0m wide and 1.3m deep—but the developer and director Christopher Walker Praat is developing a much longer 3.66m (12ft) version with steps at both ends. Likely options include a sliding frame for a jad support, non-slip flooring, fire-retardant versions, and an extractor kit for fumes.
At £600 for the standard and £1,350 for the 12-footer, it's quite a low-cost option for the occasional user. However, for the many larger CV fleets still operating out of fairly old premises, fabricated steel pits are the preferred method of upgrading the facilities of their existing workshops.
Premier's managing director Mel Burrell argues that they are more efficient and smarter in appearance, and provide generally better working conditions for the technicians. "They have to be a more cost-effective alternative to the traditional 'in-situ' pits." he adds.