How Modern Equipment Reduces Maintenance Costs
Page 83
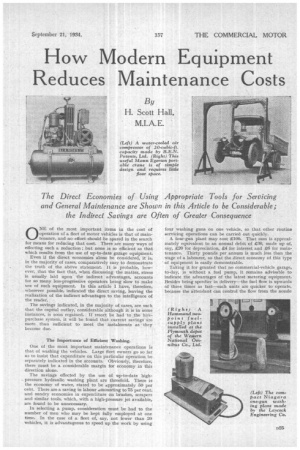
Page 84
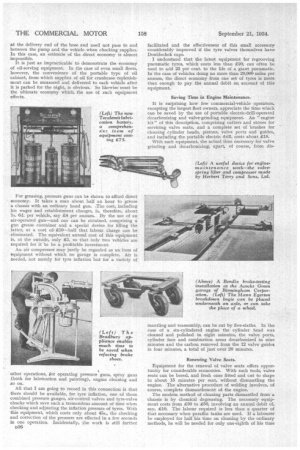
Page 85
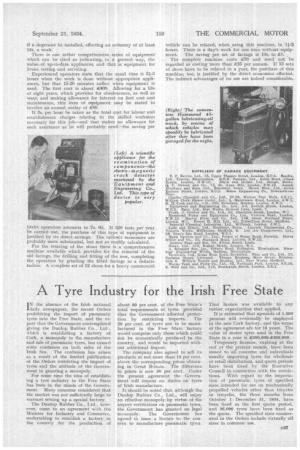
If you've noticed an error in this article please click here to report it so we can fix it.
The Direct Economies of Using Appropriate Tools for Servicing and General Maintenance are Shown in this Article to be Considerable; the Indirect Savings are Often of Greater Consequence
ONE of the most important items in the cost of operation of a fleet of motor vehicles is that of maintenance, and no effort should be spared in the search for means for reducing that cost There are many ways of effecting such a reduction ; but none is so efficient as that which results from the use of up-to-date garage equipment. Even if the direct economies alone be considered, it is, in the majority of cases, comparatively easy to demonstrate the truth of . the above statement. It is probable, however, that the fact that, when discussing the matter, stress is usually laid upon the indirect advantages, accounts for so many less-progressive operators being slow to make use of such equipment. In this article I have, therefore, wherever possible, indicated the direct saving, leaving the realization of the indirect advantages to the intelligence of the reader.
The savings indicated, in the majority of cases, are such that the capital outlay, considerable although it is in Some instances, is soon regained. If resort be had to the hirepurchase system, it will be found that current savings are snore than sufficient to meet the instalments as they become due.
The Importance of Efficient Washing.
One of the most important maintenance operations is that of washing the vehicles. Large fleet owners go so far as to insist that expenditure on this particular operation be separately indicated in the accounts. Obviously, therefore, there must be a considerable margin for economy in this direction alone.
The savings effected by the use of up-to-date highpressure hydraulic washing plant are threefold. There is the economy of water, stated to be approximately 50 per cent. There are a saving in labour amounting to 75 per cent. and sundry economies in expenditure on brushes, scrapers and similar tools, which, with a high-pressure jet available, are found to be unnecessary.
In selecting a pump, consideration must be had to the number of men who may be kept fully employed at one time. In the case of a fleet of, say, not fewer than 20 vehicles, it is advantageous to speed up the work by using four washing guns on one vehicle, so that other routine servicing operations can be carried out quickly.
A four-gun plant may cost 2100. That sum is approximately equivalent to an annual debit of £m made up of, say, 220 for depreciation, 24 for interest and 28 for maintenance. Thirty pounds per annum is much less than the wage of a labourer, so that the direct economy of this type of equipment is easily demonstrable.
Taking it for granted that no commercial-vehicle garage, to-day, is without a fuel pump, it remains advisable to indicate the advantages of the latest metering equipment. Besides being speedier in delivery—the fuel flow is upwards of three times as fast—such units are quicker to operate, because the attendant can control the flow from the nozzle at the delivery end of the hose and need not pass to and between the pump and the vehicle, when checking supplies. In this case, an estimate of the direct economy is almost impossible.
It is just as impracticable to demonstrate the economy of oil-serving equipment. In the case of even small fleets, however, the convenience of the portable type of oil cabinet, from which supplieS of oil for crankcase replenishment can be measured and delivered to each vehicle after it is parked for the night, is obvious: So likewise must be the ultimate economy which., the use of such equipment effects.
For greasing, pressure guns can be shown to afford direct economy. It takes a man about half an hour to grease a chassis with an ordinary hand gun. The cost, including his wages and establishment charges, is, therefore, about 1.s. 0<1. per vehicle, say £4 per annum. By the use of an air-operated gun—and one can be obtained, comprising a gun grease container and a special device for filling the latter, at a cost of £10—half that labour charge can be eliminated. The equivalent annual cost of this equipment is, at the outside, only £3, so that only two vehicles are required for it-to be a profitable investment.
An air compressor may justly be regarded as an item of equipment without which no garage is complete. Air is needed, not merely for tyre inflation but for a variety of other operations, for operating pressure guns, spray guns (both for lubrication and painting), engine cleaning and so on.
All that I am going to record in this connection ii that there should be available, for tyre inflation, one of those combined pressure gauges, air-control valves and tyre-valve chucks which save such a tremendous amount of time when checking and adjusting the inflation pressure of tyres. With this equipment, which costs only about 43s., the checking and correction of the pressure are effected in a few seconds in one operation. Incidentally, the work is still further D2B facilitated and the effectiveness of this small accessory considerably improved if the tyre valves themselves have Doublechek caps.
I understand that the latest equipment for regrooving pneumatic tyres, which costs less than £20, can often be used to add 25 per cent. to the life of a, giant pneumatic. In the case of vehicles doing no more than 20,000 miles per annum, the direct economy from one set of tyres is more than enough to pay the annual debit on account of this equipment.
Saving Time in Engine Maintenance,
It is surprising how few commercial-vehicle operators, excepting the largest fleet owners, appreciate the time which can he saved by the use of portable electric-drill-operated decarbonizing and valve-grinding equipment. An "engine kit" of this description, comprising cutters and stones for servicing valve seats, and a complete set of brushes for cleaning cylinder heads, pistons, valve ports and guides, and including the portable electric drill, costs about £18.
With such equipment, the actual time necessary for valve grinding and decarbonizing; apart, of course, from dis
mantling and reassembly, can be cut by five-sixths. In the case of a six-cylindered engine the cylinder head was cleaned and polished in eight minutes, the valve ports, cylinder face and combustion areas decarbonized in nine minutes and the carbon removed from the 12 valve guides in four minutes, a total of just over 20 minutes.
Renewing Valve Seats,
Equipment for the renewal of valve seats offers opportunity for cOnsiderahle economies. With such tools, valve seats can be bored, and fresh ones fitted and cut to shape in about 15 minutes per seat, without dismantling the engine. The alternative procedure of welding involves, of course, complete dismantlement of the engine.
The modern Method of cleaning parts dismantled from a chassis is by chemical degreasing. The necessary equipment costs from £30 to £50, involving an annual debit of, say, MAI The labour required is less than a quarter of that necessary when paraffin tanks are used. If a labourer be employed for half his time on cleaning by the ordinary methods, he will be needed for only one-eiglith of his time
if a degreaser be installed, effecting an economy of at least 15s. a week.
There is one rather comprehensive series of equipment which can he cited as indicating, in a general way, the valne,of up-to-date appliances, and that is equipment for brake testing and servicing.
Experienced operators state that the usual time is 2i-8 hours when the work is done without appropriate appliances, but that 15-20 minutes suffice when equipment is used. The first cost is about £400. Allowing for a life of eight years, which provides for obsolescence, as well as wear, and making allowance for interest on first cost and maintenance, this item of equipment may be stated to involve an annual outlay of £80.
If 3s. per hour he taken as the total cost for labour and establishment charges relating to the skilled workman necessary for this job—and that makes no allowance for such assistance as he will probably need—the saving per brake operation amounts to :7s. 6d. If 220 tests per year be carried out, the purchase of this type of equipment is justified by its direct savings. The indirect economies are probably more substantial, but not so readily calculated.
For the refacing of the, shoes there is a comprehensive machine available which provides for the removal of the old facings, the drilling and fitting of the new, completing the operation by grinding the fitted facings to a definite raditis. A complete set of 12 shoes for a heavy commercial
• vehicle can be refaced, when using this machine, in 14-2 hours. There is a day's work for one man without-_eq-nip
ment. The saving per set of facings is 18s. to Ll.
The complete machine costs £70 and need not be regarded as costing more than £15 per annum. If 15 sets of shoes have to be refaced in a year, the purchase of this machine, too, is justified by the direct economies effected. The indirect advantages of its use are indeed considerable.
E. P. Bairns, Ltd., 55, Upper Thames Street, London, E.C.4. Bendix, Ltd., Tyseley, Birmingham. B.E.N.Patents, Ltd., Cent Road, Chase
'Estate, London, N.W.10. Black and Decker, Ltd., Slough, Bricks. ;•,,, E. Bowser and Co., 72, St. Anne Hill, Loudon, S.W.18. Joseph Bradbury and Sons, Ltd., Braintree, F.ssex. Brown Bros. Ltd., .Great Eastern Street, London, E.C..2. Buma Engineering Cm, :1tiewcastle.etie Tyne.
Charles Churchill and Co., Ltd., 27-34, . Walnut Tree Walk, S.E./1„ William Clark 'Spare Parts), Ltd. 5, Marshaisea Road, London, &W.1.
R. H. Cook and Co., Ltd,, 209, Broadway, Hendon. London, N.W.9. • Equipment and Engineering Co., Ltd., 2-5, Norfolk Street, London, W.C.2. Epee, Ltd., Star Works. Skinner Lane, Leeds, 7.
Fredk. 3. Gordon and Co., Ltd.; 92, Charlotte Street, London, W.1. Hammond Pump and Equipment Co,, Ltd., Victoria Road, London, N.W.10. Harvey Frost and Co. Ltd., 148, Great Portland Street, London, W.1. Ernest H. Hill, Lid., 62, Fitzwilliam Street, Sheffield. Truperial Chemical Industries, Ltd., Millbank, London, S.W.1. Lake and Elliott, Ltd., Braintree, Essex. Laycock Engineering Co.. Victoria Works, Millhouses, Sheffield, S. Leo Air threpreascrs, Ltd., 28, Gray's Irm Read, London, W.C.1.•
Marin .Egerion and Co., Ltd., Prince ol Wales Road, Norwich. Henry Millerand Co., 23, Standard Rand, London, N.w.io.
• Andrew Page and Son, 99, Albion Street, Leeds.
Rotal, Ltd., 519,. Regent Street, London, W.1. A. Schrader Son, Inc., Tyburn Road, Erdingtom Birmingham. Simpkins' Engineering Works, Gedling, Nottingham. Tecaleinit, Lid., Great West Read, Brentiord. Theo and Co., Ltd., 32, Tarleton Street, Liverpool. MTLS013 Brothers, Mom Street, Birming ham 4. Witham Turner and Brother, Ltd., Eyre Works, Sheffield.
Wayne Tank and Pump Co., Ltd., 42, Newlands Park, London, S.E.26.
S. Well and Co., Ltd., 115, Southwark Street, London, £I.E.1.