The Properties of Elektron Reviewed
Page 64
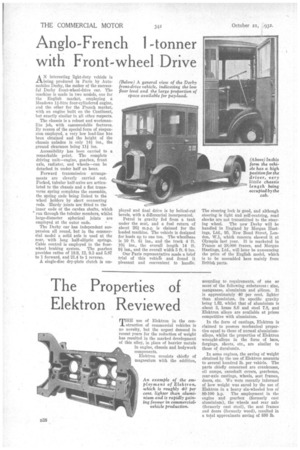
Page 65
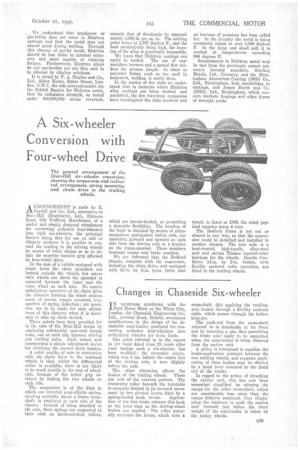
If you've noticed an error in this article please click here to report it so we can fix it.
MHE use of Elektron in the con struction of commercial vehicles is no novelty, but the urgent demand in recent years for the reduction of weight has resulted in the marked development of this alloy, in place of heavier metals in engine, chassis and bodywork components.
Elektron consists chiefly of magnesium with the addition, according to requirements, of one or more of the following substances : zinc, manganese, aluminium and silicon. It is approximately 40 per cent, lighter than aluminium, its specific gravity being 1.82, whilst that of aluminium is about 3, brass S.6 and steel 7.8, and Elektron alloys are available at prices competitive with aluminium.
In the form of castings, Elektron is claimed to possess mechanical properties equal to those of normal aluminiumalloys whilst the properties of Elektron wrought-alloys in the form of bars, forgings sheets, etc., are similar to those of duralumin.
In some engines, the saving of weight obtained by the use of Elektron amounts to several hundred lb. per vehicle. The parts chiefly concerned are crankcases, oil sumps, camshaft covers, gearboxes, rear-axle castings, wheels, seat frames, doors, etc. We were recently informed of how weight was saved by the use of Elektron in a heavy six-wheeled bus of 80-100 b.p. The employment in the engine and gearbox (formerly cast aluminium), the wheels and rear axle (formerly cast steel), the seat frames and doors (formerly wood), resulted in a total approximate saving of 880 lb. We understand that speckiness or pin-holing does not occur in Elektron castings and that the metal does not absorb gases during melting. Through this absence of specky metal, Elektron should be less liable to internal corrosion and more capable of resisting fatigue. Furthermore, Elektron alloys do not age-harden nor are they said to be affected by alkaline solutions.
It is stated by F. A. Islug,hes and Co., Ltd., Abbey House, Baker Street, London, N.W.1, the sole coneessionnaire for the British Empire for Elektron metal, that its endurance strength, as tested under 400,000,000 stress reversals, exceeds that of duralumin by approximately 3,000.1b. per sq. in. The melting point being at 1,197 degrees F., and the heat conductivity being high, the burning of the alloy is practically impossible.
We learn that Elektron castings can easily be welded. The use of oxyacetylene burners and a special flux renders the process simple. In sheet or extruded forms, such as are used in bodywork, welding is easily done.
In the matter of fire risks we understand that in factories where Elektron alloy castings are being worked and machined, the fire insurance companies have investigated the risks involved and no increase of premium has been called for. In the foundry the metal is being constantly raised to over 1,300 degrees F. In the forge and sheet mill it is worked at temperatures exceeding 900 degrees F.
Requirements in Elektron metal may be met from the previously named concern's licensed suppliers, Sterling Metals, Ltd., Coventry, and the Birmingham Aluminium Casting (1903) Co., Ltd., Birmingham, both specializing in castings, and James Booth and Co. (1915), Ltd., Birmingham, which concern markets forg,ings and other forms of wrought goods.