Meeting the customer more than half way
Page 27
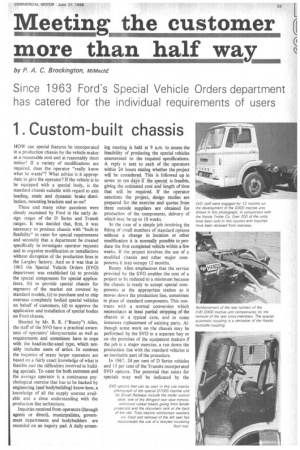
Page 28
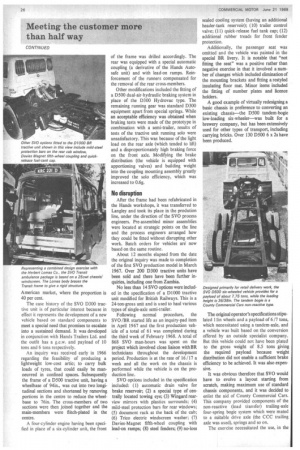
Page 29
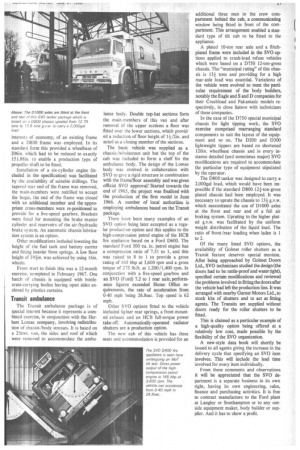
Page 30
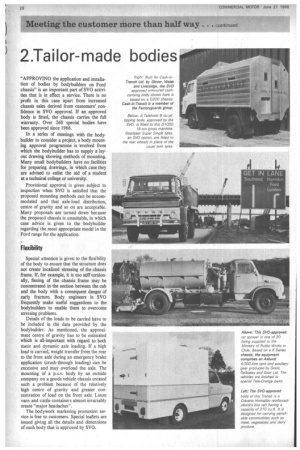
If you've noticed an error in this article please click here to report it so we can fix it.
by P. A. C. Brockington, MIMechE
Since 1963 Ford's Special Vehicle Orders department has catered for the individual requirements of users
1. Custom-built chassis
HOW can special features be incorporated in a production chassis by the vehicle maker at a reasonable cost and at reasonably short notice? If a variety of modifications are required, does the operator "really know what he wants"? What advice is it appropriate to give the operator? If the vehicle is to be equipped with a special body, is the standard chassis suitable with regard to axle loading, static and dynamic brake distribution, mounting brackets and so on?
These and many other questions were closely examined by Ford in the early design stages of the D Series and Transit ranges. It was decided that, first, it was necessary to produce chassis with "built-in flexibility" to cater for special requirements and secondly that a department be created specifically to investigate operator requests and to organize modification or installations without disruption of the production lines in the Langley factory, And so it was that in 1963 the Special Vehicle Orders (SVO) department was established (a) to provide the special components for special applications. (b) to provide special chassis for segments of the market not covered by standard models, (c) to purchase and to ship overseas completely bodied special vehicles on behalf of customers, (d) to approve the application and installation of special bodies on Ford chassis.
Headed by Mr. B. R. ("Bunny") Allen, the staff of the SVO have a practical awareness of operators' idiosyncrasies as well as requirements and sometimes have to cope with the head-in-the-sand type, which notably includes users of artics. In contrast the inquiries of many larger operators are based on a fairly exact knowledge of what is feasible and the difficulties involved in building specials. To cater for both extremes and the average operator is a continuous psychological exercise that has to be backed by engineering (and bodybuilding) know-how, a knowledge of all the supply sources available and a close understanding with the production-line technicians.
Inquiries received from operators (through agents or direct), municipalities, government departments and bodybuilders are recorded on an inquiry pad. A daily screen
ing meeting is held at 9 a.m. to assess the feasibility of producing the special vehicles enumerated to the required specifications. A reply is sent to each of the operators within 24 hours stating whether the project will be considered. This is followed up in seven to ten days if the special is feasible, giving the estimated cost and length of time that will be required. If the operator sanctions the project, design studies are prepared for the exercise and quotes from three outside suppliers are obtained for production of the components, delivery of which may be up to 18 weeks.
In the case of a simple job involving the fitting of small numbers of standard options without a change in location or other modification it is normally possible to produce the first completed vehicle within a few weeks. If the project involves the use of a modified chassis and other major components it may occupy 12 months.
Bunny Allen emphasizes that the service provided by the SVO enables the cost of a project to be reduced to a minimum because the chassis is ready to accept special components at the appropriate station as it moves down the production line, sometimes in place of standard components. This contrasts with a normal conversion which necessitates at least partial stripping of the chassis in a typical case, and in some instances replacement of existing parts. Although some work on the chassis may be performed by the SVO in a separate bay or on the premises of the equipment makers if the job is a major exercise, a run down the production line with the standard vehicles is an inevitable part of the procedure.
In 1967, 24 per cent of D Series vehicles and 13 per cent of the Transits incorporated SVO options. The potential that exists for specials may well be indicated by the American market, where the proportion is 40 per cent.
The case history of the SVO D300 tractive unit is of particular interest because in effect it represents the development of a new vehicle based on standard components to meet a special need that promises to escalate into a sustained demand. It was developed in conjunction with Hands Trailers Ltd. and the outfit has a g.c.w. and payload of 10 tons and 6 tons respectively.
An inquiry was received early in 1966 regarding the feasibility of producing a lightweight low-cost artic; to carry bulk loads of tyres, that could easily be manoeuvred in confined spaces. Subsequently the frame of a D500 tractive unit, having a wheelbase of 94in., was cut into two longitudinal sections and shortened by removing portions in the centre to reduce the wheelbase to 76in. The cross members of two sections were then joined together and the main-members were llitch-plated in the centre.
A four-cylinder engine having been specified in place of a six cylinder unit, the front of the frame was drilled accordingly. The rear was equipped with a special automatic coupling (a derivative of the Hands Autosafe unit) and with lead-on ramps. Reinforcement of the runners compensated for the removal of the rear cross-members.
Other modifications included the fitting of a 1)500 dual-air-hydraulic braking system in place of the D300 Hy drovac type. The remaining running gear was standard D300 equipment apart from special springs. While an acceptable efficiency was obtained when braking tests were made of the prototype in combination with a semi-trailer, results of tests of the tractive unit running solo were unsatisfactory. This was because of the light load on the rear axle (which tended to lift) and a disproportionately high braking force on the front axle. Modifying the brake distribution (the vehicle is equipped with apportioning valves) and building weight into the coupling mounting assembly greatly improved the solo efficiency, which was increased to 0.6g.
No disruption
After the frame had been refabricated in the Hands workshops, it was transferred to Langley and took its place in the prodution line, under the direction of the SVO process engineers. Pre-assembled minor assemblies were located at strategic points on the line and the process engineers arranged how they could be fitted without disrupting other work. Batch orders for vehicles are now based on the same routine.
About 12 months elapsed from the date the original inquiry was made to completion of the first SVO production model in March 1967. Over 200 D300 tractive units have been sold and there have been further inquiries, including one from Zambia.
No less than 14 SVO options were included in the specification of a D1000 tractive unit modified for British Railways. This is a 24-ton-gross unit and is used to haul various types of single-axle semi-trailer.
Following normal procedure, the SVO /BR started life as an inquiry-pad item in April 1967 and the first production vehicle of a total of 61 was completed during the third week of February 1968. A total of 868 SVO man-hours was spent on the project which involved close liaison with BR technicians throughout the development period. Production is at the rate of 16/17 a week and all the work on the chassis is performed while the vehicle is on the production line.
SVO options included in the specification included: (1) automatic drain valve for brake reservoir; (2) a special type of centrally located towing eye; (3) Wingard rearview mirrors with plastics surrounds; (4) mild-steel protection bars for rear windows;
(5) document rack at the back of the cab;
(6) Trico electric windscreen washer; (7) Davies-Magnet fifth-wheel coupling with lead-on ramps; (8) steel fenders; (9) no-loss
sealed cooling system (having an additional header-tank reservoir); (10) trailer control valve; (11) quick release fuel tank cap; (12) additional rubber treads for front fender protection.
Additionally, the passenger seat was omitted and the vehicle was painted in the special BR livery. It is notable that "not fitting the seat" was a positive rather than negative exercise in that it involved a number of changes which included elimination of the mounting brackets and fitting a restyled insulating floor mat. Minor items included the fitting of number plates and licence holders, A good example of virtually redesigning a basic chassis in preference to converting an existing chassis—the D500 tandem-bogie low-loading six-wheeler—was built for a brewery company, but has been extensively used for other types of transport, including carrying bricks. Over 130 D500 6 x 2s have been produced.
The original operator's specifications stipulated 1 lin wheels and a payload of 6 /7 tons, which necessitated using a tandem-axle, and a vehicle was built based on the conversion offered by an outside specialist company. But this vehicle could not have been plated to the gross weight of 8.5 tons giving the required payload because weight distribution did not enable a sufficient brake efficiency to be achieved. It was also expensive.
It was obvious therefore that SVO would have to evolve a layout starting from scratch, making maximum use of standard chassis components, and it was decided to enlist the aid of County Commercial Cars. This company provided components of the non-reactive (load transfer) trailing-axle four-spring bogie system which were mated to a suitable drive axle (the CCC trailing axle was used), springs and so on.
The exercise necessitated the use, in the interests of economy, of an existing frame and a 0800 frame was employed. In its standard form this provided a wheelbase of 206in. which had to be reduced to exactly 151.88in. to enable a production type of propeller shaft to be fitted.
Installation of a six-cylinder engine (included in the specification) was facilitated by the availability of suitable drillings. The tapered rear end of the frame was removed, the main-members were redrilled to accept the bogie, the end of the frame was closed with an additional member and the appropriate cross-members were re-positioned to provide for a five-speed gearbox. Brackets were fitted for mounting the brake master cylinder and reservoirs of the air /hydraulic brake system. An automatic chassis lubrication system is an option.
Other modifications included lowering the height of the fuel tank and battery carrier and fitting heavier front springs. A low floor height of 39+in was achieved by using 16in. wheels.
From start to finish this was a 12-month exercise, completed in February. 1967. One batch of chassis is equipped with bottlecrate-carrying bodies having open sides enclosed by plastics curtains.
Transit ambulance The Transit ambulance package is of special interest because it represents a combined exercise, in conjunction with the Herbert Lomas company, involving redistribution of chassis/body stresses. It is based on a 25cwt. van, the sides and roof of which were removed to accommodate the ambu lance body. Double top-hat sections form the main-members of this van and after removal of the upper sections a floor was fitted over the lower sections, which provided a reduction of floor height of 1+/2in. and acted as a closing member of the sections.
The basic vehicle was supplied as a chassis /windscreen unit but the top of the cab was included to form a shelf for the ambulance body. The design of the Lomas body was evolved in collaboration with SVO to give a rigid structure in combination with the frame/floor assembly and was given official SVO approval!' Started towards the end of 1965, the project was finalized with the production of the first model in June 1966. A number of local authorities is employing ambulances based on the Transit package.
There have been many examples of an SVO option being later accepted as a regular production option and this applies to the high-compression petrol engine of the HCB fire appliance based on a Ford D600. The standard Ford 300 Cu. in. petrol engine has a compression ratio of 7.51 to 1, and this was raised to 8 to 1 to provide a gross rating of 165 bhp at 3,600 rpm and a gross torque of 275 lb.ft. at 1,200/1,400 rpm. In conjunction with a five-speed gearbox and an SW) (Ford) 7.2 to 1 rear axle, performance figures exceeded Home Office requirements, the rate of acceleration from 0-40 mph being 26.8sec. Top .speed is 62 mph.
Other SVO options fitted to the vehicle included lighter rear springs, a front-mounted exhaust and an HCB full-torque power take-off. Automatically-operated radiator shutters are a production option.
The new cab of this vehicle has three seats and accommodation is provided for an
additional three men in the crew compartment behind the cab, a communicating window being fitted in front of the compartment. This arrangement enabled a standard type of tilt cab to be fitted to the appliance.
A plated 10-ton rear axle and a flitchplated frame were included in the SVO options applied to crush-load refuse vehicles which were based on a D750 12-ton-gross chassis. The "municipal rating" of this chassis is 13+ tons and providing for a high rear-axle load was essential. Variations of the vehicle were evolved to meet the particular requirement of the body builders, notably the Eagle and S and D companies for their Crushload and Pakamatic models respectively, in close liaison with technicians of these companies.
In the case of the D750 special municipal chassis for light tipping work, the SVO exercise comprised rearranging Standard components to suit the layout of the equipment and so on. The D200 and D300 lightweight tippers are based on shortened 120in. wheelbase chassis and in every instance detailed (and sometimes major) SVO modifications are required to accommodate the particular type of equipment stipulated by the operator.
The D800 tanker was designed to carry a 2,000gal load, which would have been impossible if the standard D800 124-ton-gross plated chassis had been employed. It was necessary to uprate the chassis to 13f g.v.w. which necessitated the use of D1000 axles at the front and rear and of a full air braking system. Uprating to the higher plated g.v.w. was facilitated by the uniform weight distribution of the liquid load. The ratio of front/rear loading when laden is 1 to 2.
Of the many listed SVO options, the availability of Golmet roller shutters as a Transit feature deserves special mention. After being approached by Golmet Doors Ltd., SVO technicians studied the design (the doors had to be rattle-proof and water tight), specified certain modifications and reviewed the problems involved in fitting the doors after the vehicle had left the production line. It was arranged with nearby Garner Motors Ltd., to stock kits of shutters and to act as fitting agents. The Transits are supplied without doors ready for the roller shutters to be fitted.
This is claimed as a particular example of a high-quality option being offered at a relatively low cost, made possible by the flexibility of the SVO organization.
A new-style data book will shortly be issued to all agents giving the increase in the delivery cycle that specifying an SVO item involves. This will include the lead time involved for every item individually.
From these comments and observations it will be appreciated that the SVO department is a separate business in its own right, having its own engineering, sales, finance and purchasing activities. It is free to contract manufacture to the Ford plant at Langley or Southampton or to any outside equipment maker, body builder or supplier. And it has to show a profit. "APPROVING the application and installation of bodies by bodybuilders on Ford chassis" is an important part of SVO activities that is in effect a service. There is no profit in this case apart from increased chassis sales derived from customers' confidence in SVO approval. If an approved body is fitted, the chassis carries the full warranty. Over 260 special bodies have been approved since 1966.
In a series of meetings with the bodybuilder to consider a project, a body mounting approval programme is 'evolved from which the bodybuilder has to supply a layout drawing showing methods of mounting. Many small bodybuilders have no facilities for preparing drawings, in which case they are advised to enlist the aid of a student at a technical college or university.
Provisional approval is given subject to inspection when SVO is satisfied that the proposed mounting methods can be accommodated and that axle-load distribution, centre of gravity and so on are acceptable. Many proposals are turned down because the proposed chassis is unsuitable, in which case advice is given to the bodybuilder regarding the most appropriate model in the Ford range for the application.
Flexibility
Special attention is given to the flexibility of the body to ensure that the structure does not create localized stressing of the chassis frame. If, for example, it is too stiff torsionally, flexing of the chassis frame may be concentrated in the section between the cab and the body with a consequent danger of early fracture. Body engineers in SVO frequently make useful suggestions to the bodybuilders to enable them to overcome stressing problems.
Details of the loads to be carried have to be included in the data provided by the bodybuilder. As mentioned, the approximate centre of gravity has to be estimated which is all-important with regard to both static and dynamic axle loading. If a high load is carried, weight transfer from the rear to the front axle during an emergency brake application (crush-through loading) can be excessive and may overload the axle. The mounting of a p.s.v. body by an outside ,company on a goods vehicle chassis created such a problem because of the relatively high centre of gravity and greater concentration of load on the front axle. Luton vans and cattle containers almost invariably create "major headaches".
• The bodywork marketing promotion service is free to customers. Special leaflets are issued giving all the details and dimensions of each body that is approved by SVO.