R-SERIES
Page 18
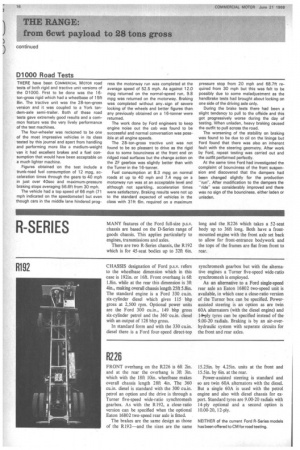
Page 22
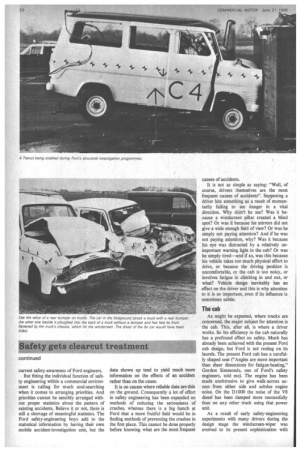
Page 23
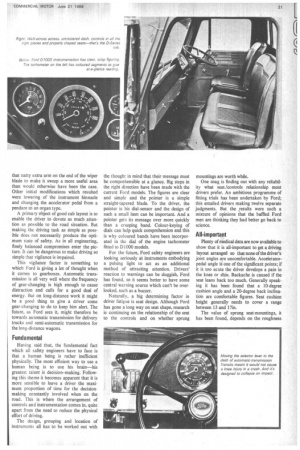
Page 24
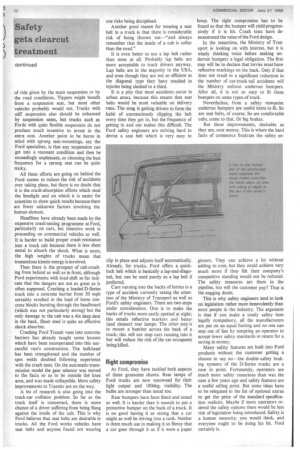
If you've noticed an error in this article please click here to report it so we can fix it.
MANY features of the Ford full-size p.s.v. chassis are based on the D-Series range of goods chassis. This applies particularly to engines, transmissions and axles.
There are two R-Series chassis, the R192 which is for 45-seat bodies up to 32ft 6in. long and the_R226 which takes a 52-seat body up to 36ft long. Both have a frontmounted engine with the front axle set back to allow for front-entrance bodywork and the tops of the frames are flat from front to rear.
R192
CHASSIS designation of Ford p.s.v. refers to the wheelbase dimension which in this case is 192in. or 16ft. Front overhang is 6ft 1.8in. while at the rear this dimension is 3ft 4in., making overall chassis length 25ft 5.8in. The standard engine is a Ford 330 cu.in. six-cylinder diesel which gives 115 bhp gross at 2,500 rpm. Optional power units are the Ford 300 cu.in., 149 bhp gross six-cylinder petrol and the 360 'cu.in. diesel with an output of 128 bhp gross.
In standard form and with the 330 min. diesel there is a Ford four-speed direct-top synchromesh gearbox but with the alternative engines a Turner five-speed wide-ratio synchromesh is employed.
As an alternative to a Ford single-speed rear axle an Eaton 16802 two-speed unit is available, in which case a close-ratio version of the Turner box can be specified. Powerassisted steering is an option as are twin 60A alternators (with the diesel engine) and 140ply tyres can be specified instead of the 9.00-20 radials. Braking is by an air-overhydraulic system with separate circuits for the front and rear axles.
R225
FRONT overhang on the R226 is 6ft 2in. and at the rear the overhang is 3ft 3in. which with the 18ft 10in, wheelbase makes overall chassis length 2811 4in. The 360 cu.in. diesel is standard with the 300 cu.in. petrol an option and the drive is through a Turner five-speed wide-ratio synchromesh gearbox. As with the R192, a close-ratio version can be specified when the optional Eaton 16802 two-speed rear axle is fitted.
The brakes are the same design as those of the R192—and the sizes are the same 15.25in. by 4.25in. units at the front and 15.5in. by 6in. at the rear.
Power-assisted steering is standard and so are twin 60A alternators with the diesel. But a single 60A is used with the petrol engine and also with diesel chassis for export. Standard tyres are 9.00-20 radials with 14-ply optional and a second option is 10.00-20, 12-ply.
NEITHER of the current Ford R-Series models has been offered to CM for road testing.
current safety-awareness of Ford engineers.
But fitting the individual function of safety engineering within a commercial environment is calling for much soul-searching when it comes to arranging priorities. And priorities cannot be sensibly arranged without proper statistics about the pattern of existing accidents. Believe it or not, there is still a shortage of meaningful statistics. The Ford safety-engineering boys add to the statistical information by having their own mobile accident-investigation unit, but the data shown up tend to yield much more information on the effects of an accident rather than on the cause.
It is on causes where reliable data are thin on the ground. Consequently a lot of effort in safety engineering has been expended on methods of reducing the seriousness of crashes, whereas there is a big hunch at Ford that a more fruitful field would be in finding methods of preventing the crashes in the first place. This cannot be done properly before knowing what are the most frequent causes of accidents.
It is not as simple as saying: "Well, of course, drivers themselves are the most frequent causes of accidents". Supposing a driver hits something as a result of momentarily failing to see danger in a vital direction. Why didn't he see? Was it because a windscreen pillar created a blind spot? Or was it because his mirrors did not give a wide enough field of view? Or was he simply not paying attention? And if he was not paying attention, why? Was it because his eye was distracted by a relatively unimportant warning light in the cab? Or was he simply tired—and if so, was this because his vehicle takes too much physical effort to drive, or because the driving position is uncomfortable, or the cab is too noisy, or involves fatigue in climbing in and out, or what? Vehicle design inevitably has an effect on the driver and this is why attention to it is so important, even if its influence is sometimes subtle.
The cab As might be expected, where trucks are concerned, the major subject for attention is the cab. This, after all, is where a driver works. So his efficiency in the cab naturally has a profound effect on safety. Much has already been achieved with the present Ford cab design, but Ford is not resting on its laurels. The present Ford cab has a carefully shaped seat ("Angles are more important than sheer dimensions for fatigue-beating," Gordon Simmonds, one of Ford's safety engineers, told me). The engine has been made unobtrusive to give walk-across access from either side and subdue engine noise. On the D1000 the noise of the V8 diesel has been damped more successfully than on any other truck using that power unit.
As a result of early safety-engineering experiments with many drivers during the design stage the windscreen-wiper was evolved to its present sophistication with that natty extra arm on the end of the wiper blade to make it sweep a more useful area than would otherwise have been the case. Other initial modifications which resulted were lowering of the instrument binnacle and changing the accelerator pedal from a pendant to an organ type.
A primary object of good cab layout is to enable the driver to devote as much attention as possible to the road situation. But making the driving task as simple as possible does not necessarily produce the optimum state of safety. As in all engineering, finely balanced compromises enter the picture. It can be dangerous to make driving so simple that vigilance is impaired.
This vigilance factor is something to which Ford is giving a lot of thought when it comes to gearboxes. Automatic transmission is all very well where the frequency of gear-changing is high enough to cause distraction and calls for a good deal of energy. But on long-distance work it might be a good thing to give a driver some gear-changing to do to keep him alert. The future, as Ford sees it, might therefore be towards automatic transmission for delivery trucks and semi-automatic transmission for the long-distance wagons.
Fundamental
Having said that, the fundamental fact which all safety engineers have to face is that a human being is rather inefficient physically. The most efficient way to use a human being is to use his brain—his greatest talent is decision–making. Following this theme it becomes apparent that it is more sensible to leave a driver the maximum proportion of time for the decisionmaking constantly involved when on the road. This is where the arrangement of controls and instrumentation comes in, quite apart from the need to reduce the physical effort of driving.
The design, grouping and location of instruments all has to be worked out with the thought in mind that their message must be comprehensible at a glance. Big steps in the right direction have been made with the current Ford models. The figures are clear and simple and the pointer is a simple straight-tapered blade. To the driver, the pointer is his dial-sensor and the design of such a small item can be important. And a pointer gets its message over more quickly than a creeping band. Colour-keying of dials can help quick comprehension and this is why coloured bands have been incorporated in the dial of the engine tachometer fitted to Dl 000 models.
For the future, Ford safety engineers are looking seriously at instruments embodying a pulsing light to act as an additional method of attracting attention. Drivers' reaction to warnings can be sluggish, Ford has found, so it seems better to have some central warning source which can't be overlooked, such as a buzzer.
Naturally, a big determining factor in driver fatigue is seat design. Although Ford has gone a long way on seat shape, research is continuing on the relationship of the seat to the controls and on whether sprung mountings are worth while.
One snag is finding out with any reliability what seat /controls relationship most drivers prefer. An ambitious programme of fitting trials has been undertaken by Ford; this entailed drivers making twelve separate judgments. But the fesults were such a mixture of opinions that the baffled Ford men are thinking they had better go back to science.
All-important
Plenty of medical data are now available to show that it is all-important to get a driving layout arranged so that none of the driver's joint angles are uncomfortable. Acceleratorpedal angle is one of the significant points; if it is too acute the driver develops a pain in the knee or shin. Backache is caused if the seat leans back too much. Generally speaking it has been found that a 10-degree cushion angle and a 20-degree back inclination are comfortable figures. Seat cushion height generally needs to cover a range between 13 and 17in.
The value of sprung seat-mountings, it has been found, depends on the roughness of ride given by the main suspension or by the road conditions. Tippers might benefit from a suspension seat, but most other vehicles probably would not. Trucks with stiff suspension also should be enhanced by suspension seats, but trucks such as Fords with quite flexible suspension do not produce much incentive to invest in the extra cost. Another point to be borne in mind with sprung seat-mountings, say the Ford specialists, is that any suspension can get into a resonant condition and then be exceedingly unpleasant, so choosing the best frequency for a sprung seat can be quite tricky.
All these efforts are going on behind the Ford scenes to reduce the risk of accidents ever taking place, but there is no doubt that it is the crash-absorption efforts which steal the limelight and on which it is easier for scientists to show quick results because there are fewer unknown factors involving the human element.
Headlines have already been made by the expensive crash-testing programme at Ford, particularly on cars, but intensive work is proceeding on commercial vehicles as well. It is harder to build proper crash resistance into a truck cab because there is less sheet metal to absorb the shock. What is more, the high weights of trucks mean that tremendous kinetic energy is involved.
Then there is the prospect of cab-crushing from behind as well as in front, although Ford experiments with load-shift so far indicate that the dangers are not -so great as is often supposed. Crashing a loaded D-Series truck into a concrete barrier from 20 mph certainly resulted in the load of loose concrete blocks bursting through the headboard (which was not particularly strong) but the only damage to the cab was a 4in deep dent in the back. Sheet steel is quite an effective shock absorber.
Crashing Ford Transit vans into concrete barriers has already taught some lessons which have been incorporated into this successful van's construction. The bulkhead has been strengthened and the number of spot welds doubled following experience with the crash tests. On the automatic-transmission model the gear selector was moved to the facia so as to be outside the knee area, and was made collapsible. More safety improvements to Transits are on the way.
A lot of research is also going into the truck-car collision problem. So far as the truck itself is concerned, there is more chance of a driver suffering from being flung against the inside of the cab. This is why Ford believes that seat belts are desirable in trucks. All the Ford works vehicles have seat belts and anyone found not wearing one risks being disciplined.
Another good reason for wearing a seat belt in a truck is that there is considerable risk of being thrown out—"and always remember that the inside of a cab is softer than the road."
It is even better to use a lap belt rather than none at all. Probably lap belts are more acceptable to truck drivers anyway. Lap belts are in the majority in the USA, and even though they are not so efficient as the diagonal type they have resulted in injuries being slashed to a third.
It is a pity that most accidents occur in urban areas, because this means that seat belts would be most valuable on delivery vans. The snag is getting drivers to form the habit of unconsciously clipping the belt every time they get in, but the frequency of getting in and out makes this difficult. The Ford safety engineers are striving hard to devise a seat belt which is very easy to clip in place and adjusts itself automatically. Already, for trucks, Ford offers a quicklock belt which is basically a lap-and-diagonal, but can be used purely as a lap belt if preferred.
Cars running into the backs of lorries is a type of accident currently taxing the attention of the Ministry of Transport as well as Ford's safety engineers. There are two steps under consideration. One is to make the backs of trucks more easily spotted at night; this entails reflective markers and better (and cleaner) rear lamps. The other step is to mount a bumber across the back of a truck; this will not stop cars running into it but will reduce the risk of the car occupants being killed.
Right compromise
At Ford, they have tackled both aspects of these gruesome shunts. Rear lamps of Ford trucks are now renowned for their light output and 180deg. visibility. The bulbs are stronger than usual too.
Rear bumpers have been fitted and tested as well. It is harder than it sounds to put a protective bumper on the back of a truck. It is no good having it so strong that a car might as well be driving into a tank. Neither is there much use in making it so flimsy that a car goes through it as if it were a paper hoop. The right compromise has to be found so that the bumper will yield progresssively if it is hit. Crash tests have demonstrated the value of the Ford design.
In the meantime, the Ministry of Transport is looking on with interest, but it is wisely thinking twice before making underrun bumpers a legal obligation. The first step will be to declare that lorries must have reflective markings on the back. Only if that does not result in a significant reduction in the number of car-truck-tail accidents will the Ministry enforce underrun bumpers. After all, it is not so easy to fit these bumpers on some types of truck.
Nevertheless, from a safety viewpoint underrun bumpers are useful items to fit. So are seat belts, of course. So are comfortable cabs, come to that. Or big brakes.
But these improvements, desirable as they are, cost money. This is where the hard facts of commerce frustrate the safety en gineers. They can achieve a lot without adding to cost, but they could achieve very much more if they felt their company's competitive standing would not be reduced. The safety measures are there in the pipeline, but will the customer pay? That is the nagging doubt.
This is why safety engineers tend to look on legislation rather more benevolently than most people in the industry. The argument is that if you make a costly safety item legally compulsory, all the manufacturers are put on an equal footing and no one can step out of line by tempting an operator to accept lower safety standards in return for a saving in money.
Many safety features are built into Ford products without the customer getting a chance to say no—the double-safety braking systems of the D-Series trucks are a case in point. Fortunately, operators are much more safety conscious than was the case a few years ago and safety features are a useful selling point. But some ideas have to be relegated to the list of optional extras to get the price of the standard specification realistic. Maybe if more operators ordered the safety options there would be less risk of legislation being introduced. Safety is a human necessity, you would think, and everyone ought to be doing his bit. Ford certainly is.