IPC CONFERENCE REPORT
Page 137
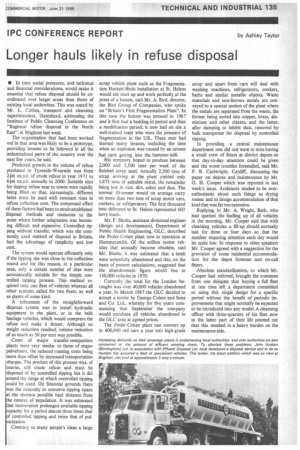
If you've noticed an error in this article please click here to report it so we can fix it.
Longer hauls likely in refuse disposal
by Ashley Taylor • In time social pressures, and technical and financial considerations, would make it essential that refuse disposal should be coordinated over larger areas than those of existing local authorities. This was stated by Mr. L. Collins, transport and cleansing superintendent, Gateshead, addressing the Institute of Public Cleansing Conference on "Regional refuse disposal in the North East", at Brighton last Week.
The organization that had been worked Out in that area was likely to be a prototype, providing lessons to be followed in all the industrialized parts of the country over the next few years, he said.
Predicted growth in the volume of refuse produced in Tyneside-Wearside was from 21-m cu.yd. of crude refuse in year 1971 to 6+rn cu.yd. annually in 2000. Suitable sites for tipping refuse near to towns were rapidly being filled so that, increasingly, different holes must be used with constant rises in refuse collection cost. The compound effect of these factors had been to strain established disposal methods and resources to the point where further adaptation was becoming difficult and expensive. Controlled tipping without transfer, which was the commonly used method of disposal in Britain, had the advantage of simplicity and low cost.
The system would operate efficiently only if the tipping site was close to the collection round and for this reason, in a particular area, only a certain number of sites were economically suitable for the simple controlled tipping process. This method required only one fleet of vehicles whereas all other systems called for two fleets, as well as plants of some kind.
A refinement of the straightforward disposal system was to install hydraulic equipment in the plant, or in the bulk haulage vehicles, which would compress the refuse and make it denser. Although no weight reduction resulted, volume reduction of as much as 50 per cent was possible.
Costs of major transfer-compaction plants were very similar to those of major pulverizers, the reduced running costs being more than offset by increased transportation charges. The product of this process was, of course, still crude refuse and must be disposed of by controlled tipping but it did extend the range at which controlled tipping could be used. On financial grounds there was the necessity to conserve tipping space at the shortest possible haul distance from he centres of population. It was estimated hat incineration prolonged available tipping apacity for a period almost three times that f controlled tipping and twice that of pulerization.
Contrary to many people's ideas a large
scrap vehicle plant such as the Fragmentation fleckett-Birds installation at St. Helens would not start up and work perfectly at the press of a button, said Mr. A. Bird, director, the Bird Group of Companies, who spoke on "Britain's First Fragmentation Plant". In this case the button was pressed in 1967 and it first had a bedding-in period and then a modification period; it now had on site a well-trained team who were the pioneers of fragmentation in the UK. These men had learned many lessons, including the time when an explosion was caused by an unseen fuel tank getting into the hammer-mill.
His company hoped to produce between 2,000 and 2,500 tons per week of the finished scrap steel. Actually 2,500 tons of scrap arriving at the plant yielded only 1,875 tons of saleable metal, the remainder being lost in rust, dirt, ashes and dust. The normal 10-tonner would on average carry no more than two tons of scrap motor cars, cookers, or refrigerators. The first thousand tons delivered to St. Helens represented 603 lorry loads.
Mr. F. Shults, assistant divisional engineer (design and development), Department of Public Health Engineering, GLC, described the Proler-Cohen plant now in operation at Hammersmith. Of the million motor vehicles that annually became obsolete, said Mr. Shults, it was estimated that a tenth were unlawfully abandoned and this, on the basis of present calculations, suggested that the abandonment figure would rise to 150,000 vehicles in 1970.
Currently the total for the London boroughs was over 40,000 vehicles abandoned a year. In March 1967 the GLC decided to accept a tender by George Cohen and Sons and Co. Ltd., whereby for five years commencing that September the company would purchase all vehicles abandoned in the GLC area at agreed prices.
The Proler-Cohen plant can convert up to 400,000 old cars a year into high-grade scrap and apart from cars will deal with washing machines, refrigerators, cookers, baths and similar metallic objects. Waste materials and non-ferrous metals are conveyed to a special section of the plant where the metals are separated from the waste, the former being sorted into copper, brass, aluminium and other classes, and the latter, after damping to inhibit dust, removed by bulk transporter for disposal by controlled tipping.
In providing a central maintenance department one did not want to miss having a small crew of fitters at district depots so that day-to-day attention could be given and the worst troubles forestalled, said Mr. P. B. Cartwright, Cardiff, discussing the paper on depots and maintenance by Mr. G. H. Cooper which was reported in last week's issue. Architects tended to be overenthusiastic about such things as drying rooms and to design accommodation of that kind that was far too extensive.
Replying to Mr. A. Wright, Bath, who had queried the fuelling up of all vehicles in the morning, Mr. Cooper said that with cleansing vehicles a fill-up should normally last for three or four days so that the number requiring attention each day would be quite low. In response to other speakers Mr. Cooper agreed with a suggestion for the provision of some residential accommodation for the depot foreman and on-call fitters.
Absolute standardization, to which Mr. Cooper had referred, brought the comment from one delegate that buying a full fleet at one time left a department committed to using this single design for a specific period without the benefit of periodic improvements that might normally be expected to be introduced into any model. A cleansing officer with three-quarters of his fleet now in the latter part of their life pointed out that this resulted in a heavy burden on the maintenance side.