NO WHEELS ON MY WAGGON!
Page 96
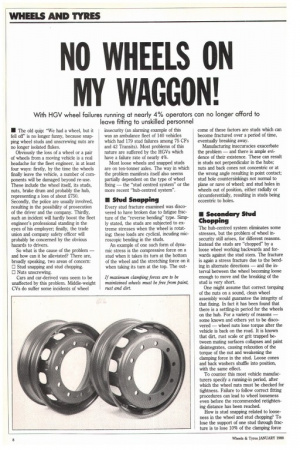
Page 97
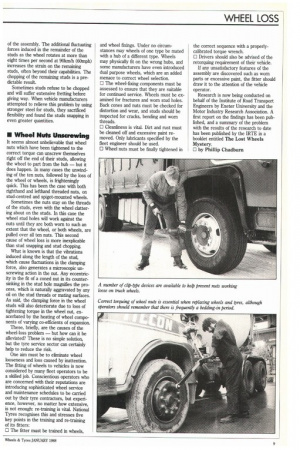
If you've noticed an error in this article please click here to report it so we can fix it.
With HGV wheel failures running at nearly 4% operators can no longer afford to leave fitting to unskilled personnel • The old quip: "We had a wheel, but it fell off' is no longer funny, because snapping wheel studs and unscrewing nuts are no longer isolated flukes.
Obviously the loss of a wheel or a pair of wheels from a moving vehicle is a real headache for the fleet engineer, in at least four ways: firstly, by the time the wheels finally leave the vehicle, a number of components will be damaged beyond re-use. These include the wheel itself, its studs, nuts, brake drum and probably the hub, representing a loss of about £750. Secondly, the police are usually involved, resulting in the possibility of prosecution of the driver and the company. Thirdly, such an incident will hardly boost the fleet engineer's professional standing in the eyes of his employer; finally, the trade union and company safety officer will probably be concerned by the obvious hazards to drivers.
So what is the cause of the problem — and how can it be alleviated? There are, broadly speaking, two areas of concern: 1:1 Stud snapping and stud chopping. El Nuts unscrewing.
Cars and car-derived vans seem to be unaffected by this problem. Middle-weight CVs do suffer some incidents of wheel insecurity (an alarming example of this was an ambulance fleet of 140 vehicles which had 179 stud failures among 75 CFs and 42 Transits). Most problems of this nature are suffered by the HGVs which have a failure rate of nearly 4%.
Most loose wheels and snapped studs are on ten-tonner axles. The way in which the problem manifests itself also seems partially dependent on the type of wheel fixing — the "stud centred system" or the more recent "hub-centred system".
• Stud Snapping
Every stud fracture examined was discovered to have broken due to fatigue fracture of the "reverse bending" type. Simply stated, the studs are subjected to extreme stresses when the wheel is rotating; these loads are cyclical, incuding microscopic bending in the studs.
An example of one such form of dynamic stress is the compressive force on a stud when it takes its turn at the bottom of the wheel and the stretching force on it when taking its turn at the top. The out come of these factors are studs which can become fractured over a period of time, eventually breaking away.
Manufacturing inaccuracies exacerbate the problem — and there is ample evidence of their existence. These can result in studs not perpendicular in the hubs; nuts and back cones not concentric or at the wrong angle resulting in point contact; stud hole countersinkings not normal to plane or nave of wheel; and stud holes in wheels out of position, either radially or circumferentially, resulting in studs being eccentric to holes.
• Secondary Stud Chopping
The hub-centred system eliminates some stresses, but the problem of wheel insecurity still arises, for different reasons. Instead the studs are "chopped" by a loose wheel working backwards and forwards against the stud stem. The fracture is again a stress fracture due to the bending in alternate directions — and the interval between the wheel becoming loose enough to move and the breaking of the stud is very short.
One might assume that correct torquing of the nuts on a sound, clean wheel assembly would guarantee the integrity of that fixing. In fact it has been found that there is a settling-in period for the wheels on the hub. For a variety of reasons — some known and others yet to be discovered — wheel nuts lose torque after the vehicle is back on the road. It is known that dirt, rust scale or grit trapped between mating surfaces collapses and paint disintegrates, causing relaxation of the torque of the nut and weakening the clamping force in the stud. Loose cones and back washers shuffle into position, with the same effect.
To counter this most vehicle manufacturers specify a running-in period, after which the wheel nuts must be checked for tightness. Failure to follow correct fitting procedures can lead to wheel looseness even before the recommended retightening distance has been reached.
How is stud snapping related to looseness in the wheel and stud chopping? To lose the support of one stud through fracture is to lose 10% of the clamping force of the assembly. The additional fluctuating forces induced in the remainder of the studs as the wheel rotates at more than eight times per second at 901anfh (60mph) increases the strain on the remaining studs, often beyond their capabilities. The chopping of the remaining studs is a predictable result.
Sometimes studs refuse to be chopped and will suffer extensive fretting before giving way. When vehicle manufacturers attempted to relieve this problem by using stronger steel for studs, they sacrificed flexibility and found the studs snapping in even greater quantities.
• Wheel Nuts Unscrewing
It seems almost unbelievable that wheel nuts which have been tightened to the correct torque can unscrew themselves right off the end of their studs, allowing the wheel to part from the hub — but it does happen. In many cases the unwinding of the ten nuts, followed by the loss of the wheel or wheels, is frighteningly quick. This has been the case with both righthand and lefthand threaded nuts, on stud-centred and spigot-mounted wheels.
Sometimes the nuts stay on the threads of the studs, even with the wheel clattering about on the studs. In this case the wheel stud holes will work against the nuts until they are both worn to such an extent that the wheel, or both wheels, are pulled over all ten nuts. This second cause of wheel loss is more inexplicable than stud snapping and stud chopping.
What is known is that the vibrations induced along the length of the stud, which cause fluctuations in the clamping force, also generates a microscopic unscrewing action in the nut. Any eccentricity in the fit of a coned nut in its countersinking in the stud hole magnifies the process, which is naturally aggravated by any oil on the stud threads or mating surfaces. As said, the clamping force in the wheel studs will also deteriorate due to loss of tightening torque in the wheel nut, exacerbated by the heating of wheel components of varying co-efficients of expansion.
These, briefly, are the causes of the wheel-loss problem — but how can it be alleviated? These is no simple solution, but the tyre service sector can certainly help to reduce the risk.
One aim must be to eliminate wheel looseness and loss caused by inattention. The fitting of wheels to vehicles is now considered by many fleet operators to be a skilled job. Conscientious operators who are concerned with their reputations are introducing sophisticated wheel service and maintenance schedules to be carried out by their tyre contractors, but experience, however, no matter how extensive, is not enough: re-training is vital. National Tyres recognises this and stresses five key points in the training and re-training of its fitters: 0 The fitter must be trained in wheels, and wheel fixings. Under no circumstances may wheels of one type be mated with a hub of a different type. Wheels may physically fit on the wrong hubs, and some manufacturers have even introduced dual purpose wheels, which are an added menace to correct wheel selection. 0 The wheel-fixing components must be assessed to ensure that they are suitable for continued service. Wheels must be examined for fractures and worn stud holes. Back cones and nuts must be checked for distortion and wear, and studs should be inspected for cracks, bending and worn threads.
0 Cleanliness is vital. Dirt and rust must be cleaned off and excessive paint removed. Only lubricants specified by the fleet engineer should be used.
0 Wheel nuts must be finally tightened in the correct sequence with a properlycalibrated torque wrench.
0 Drivers should also be advised of the retorquing requirement of their vehicle.
If any unsatisfactory features of the assembly are discovered such as worn parts or excessive paint, the fitter should draw it to the attention of the vehicle operator.
Research is now being conducted on behalf of the Institute of Road Transport Engineers by Exeter University and the Motor Industry Research Association. A first report on the findings has been published, and a summary of the problem with the results of the research to date has been published by the IRTE in a booklet entitled The Lost Wheels Mystery.
0 by Philip Chadburn