An Important Contrl tiott to
Page 58
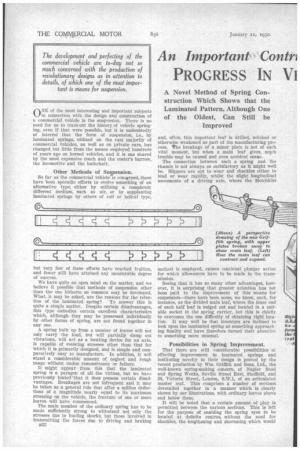
Page 59
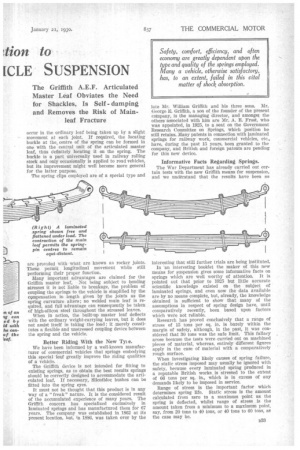
If you've noticed an error in this article please click here to report it so we can fix it.
PROGRESS IN VI ECU SUSPENSION
ONE of the most interesting and important subjects in connection with the design and construction of a commercial vehicle is the suspension. There is no need for us to trace out the history of vehicle springing, even if that were possible, but it is undoubtedly of interest that the form of suspension, i.e., by laminated springs, utilized on the vast majority of connnercial vehicles, as well as on private cars, has changed but little from the means employed hundreds of years ago on horsed vehicles, and it is one shared by the most expensive coach and the coster's barrow, the locomotive and the batlichair.
Other Methods of Suspension.
So far as the commercial vehicle is concerned, there have been sporadic efforts to evolve something of an alternative type, either by utilizing a completely different medium, such as air, or by supplanting laminated springs by others of coil or helical type,
but very few of these efforts have reached fruition, and fewer still have attained any measurable degree of success.
We have quite an open mind on the matter, and we believe it possible that methods of suspension other than the one hitherto so common may be developed. What, it may be asked, are the reasons for the reten tion of the laminated spring? To answer this is quite a simple matter, Despite certain disadvantages, this type embodies certain excellent characteristics which, although they may be possessed individually by other forms of spring, are not found together in any one.
A spring built up from a number of leaves will not only carry the load, but will partially damp out vibrations, will act as a locating device for an axle, is capable of resisting stresses other than that for which it is primarily designed, and is simple and comparatively easy to manufacture. In addition, it will stand a considerable amount of neglect and rough usage without undue remonstranCe or failure.
It might appear from this that • the laminated spring is a paragon of all the virtues, but we have previously hinted-that it does possess certain disadvantages. Breakages are not infrequent and it may be taken as a general rule that after a million deflections of a magnitude nearly equal to its maximum stressing on the vehicle, the fracture of one or more leaves will have commenced.
The main member of the ordinary spring has to be made sufficiently strong to withstand not only the stresses due to loading shocks, but those involved in transmitting the forces due to driving and braking 3332 and, often, this important leaf is drilled, notched or otherwise weakened as part of the manufacturing pro cess. he breakage of a minor plate is not of such vital moment, but when a main leaf gives, much trouble may be caused and even accident ensue.
The connection between such a spring and the chassis is not always so satisfactory as it might well be. Slippers are apt to wear and shackles either to bind or wear rapidly, whilst the slight longitudinal movements of a driving axle, where the Hotchkiss method is employed, causes continual plunger action for which allowances have to be made in the transmission.
Seeing that it has so many other advantages, however, it is surprising that greater attention has not been paid to the improvement of this means for suspension—there have been some, we know, such, for instance, as the divided main leaf, where the inner end of each half leaf is bulged out and located in a suitable socket in the spring carrier, but this is chiefly to overcome the one difficulty of obtaining rigid location. It may well be that inventors are inclined to look upon the laminated spring as something approaching finality and have therefore turned their attention to something more unusual.
Possibilities in Spring Improvement.
That there are still considerable possibilities oi effecting improvement in laminated springs and instituting novelty in their design is proved by the recent production by Wm. Griffith and Sons, Ltd., the well-known spring-making concern, of Napier Steel and Spring Works, Saville Street East, Sheffield, and 38, Victoria Street, London, S.W.1, of an articulated master leaf. This comprises a number of sections dovetailed together in a manner which is clearly shown by our illustrations, with ordinary leaves above and below them.
It will be noted that a certain amount of play is permitted between the various sections. This is left for the purpose of 'enabling the spring eyes to be located at definite centres, without the need for shackles, the lengthening and shortening which would
occur in the ordinary leaf being taken up by a slight movement at each joint. If required, the locating buckle at the centre of the spring can be formed in one with the central unit of the articulated master leaf, thus definitely locating it on the spring. The buckle is a part universally used in railway rolling stock and only occasionally is applied to road vehicles, but it improvement might well become more general for the latter purpose.
The spring clips employed are of a special type and
are provided with what are known as rocker joints. These permit longitudinal movement while still performing their proper function.
Many important advantages are claimed for the Griffith master leaf, Not being subject to bending stresses it is not liable to breakage, the problem of coupling the springs to the vehicle is simplified by the compensation in length given by the joints as the spring curvature alters ; no welded main leaf is required, and full advantage can consequently be taken of high-silicon steel throughout the stressed leaves.
When in action, the built-up master leaf deflects with the ordinary weight-carrying leaves, but it does not assist itself in taking the load ; it merely constitutes a flexible and unstressed coupling device between the spring and the vehicle. •
Better Riding With the New Tp:e.
We have been informed by a well-known manufacturer of commercial vehicles that springs embodying this special 'leaf greatly improve the riding qualities of a vehicle.
The Griffith device is not intended for fitting to existing springs, as •to obtain the best results springs should be correctly designed to accommodate the articulated leaf. If necessary, Silentbloc bushes can be fitted into the spring eyes.
It must not be thought that this product is in any way of a "freak" nature. It is the considered result of the accumulated experience of Many years. The Griffith concern has specialized exclusively in laminated springs and has manufactured them for 67 years. The company was established in 1862 at its present location, but in 1886, was taken over by the late Mr. William Griffith and his three sons. Mr. George E. Griffith, a son of the founder of the present company, is the managing director, and amongst the others associated with him are Mr. A. E. Frost, who was appointed, in 1925, to a seat on the Government Research Committee on Springs, which position he still retains. Many patents in connection with laminated springs for railway work, commercial vehicles, etc., have, during the past 15 years, been granted to the company, and British and foreign patents are pending for this new device.
Informative Facts Regarding Springs.
The War Department has already carried out certain tests with the new Griffith means for suspension, and we understand that the results have been so interesting that still further trials are being instituted.
In an interesting booklet the maker of this new means for suspension gives some informative facts on springs which are well worthy of attention. It is pointed out that prior to 1925 but little accurate scientific knowledge existed on the subject of laminated springs, and even now the data available are by no means complete, but, already, the knowledge obtained is sufficient to show that many of the assumptions in respect of spring design have, until comparatively recently, been based upon factors which were not reliable.
Research has proved conclusively that a range of stress of 15 tons per .sq. in. is barely within the margin of safety, although, in the past, it was considered that 30 tons was the safe limit. This fallacy arose because the tests were carried out on machined pieces of material, whereas, entirely different figures apply in the case of material with a comparatively rough surface.
When investigating likely causes of spring failure, the static stress imposed may usually be ignored with safety, because every laminated spring produced in a reputable British works is stressed to the extent of 66 tons per sq. in., which is in excess of any demands likely to be imposed in service.
Range of stress is the important factor which determines spring life. Static stress is the amount calculated from zero to a maximum point as the spring is deflected, whilst range of stress is the amount taken from a minimum to a maximum point, say, from 20 tons to 40 tons, or 40 tons to 60 tons, as the case may be.