ENGINEER'S
Page 30
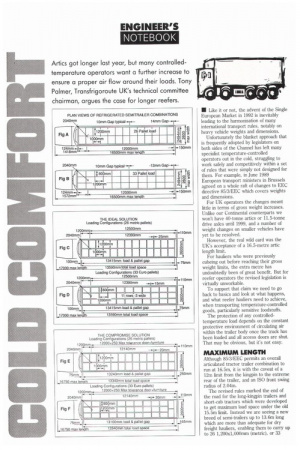
Page 31
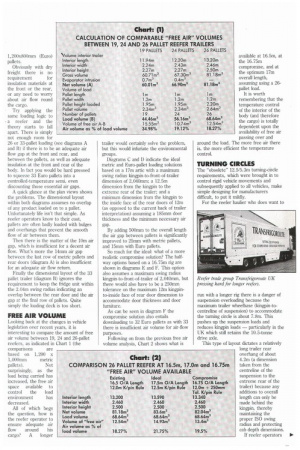
Page 32
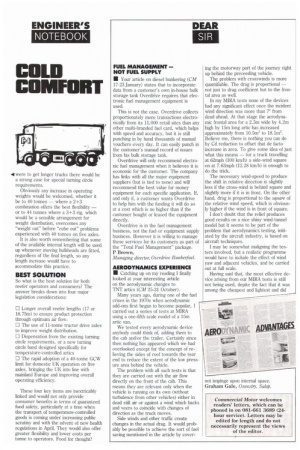
If you've noticed an error in this article please click here to report it so we can fix it.
NOTEBOOK
• Like it or not, the advent of the Single European Market in 1992 is inevitably leading to the harmonisation of many international transport rules, notably on heavy vehicle weights and dimensions.
Unfortunately the blanket approach that is frequently adopted by legislators on both sides of the Channel has left many specialist temperature-controlled operators out in the cold, struggling to work safely and competitively within a set of rules that were simply not designed for them. For example, in June 1989 European transport ministers in Brussels agreed on a whole raft of changes to EEC directive 85/3/EEC which covers weights and dimensions.
For UK operators the changes meant little in terms of gross weight increases. Unlike our Continental counterparts we won't have 40-tonne artics or 11.5-tonne drive axles until 1999, and a number of weight changes on smaller vehicles have yet to be resolved.
However, the real wild card was the UK's acceptance of a 16.5-metre artic length limit.
For hauliers who were previously cubeing out before reaching their gross weight limits, the extra metre has undoubtedly been of great benefit. But for reefer operators the revised legislation is virtually unworkable.
To support that claim we need to go back to basics and look at what happens, and what reefer hauliers need to achieve, when transporting temperature-controlled goods, particularly sensitive foodstuffs.
The protection of any controlledtemperature load depends on the constant protective environment of circulating air within the trailer body once the truck has been loaded and all access doors are shut. That may be obvious, but it's not easy.
MAXIMUM LENGTH
Although 85/3/EEC permits an overall articulated tractor trailer combination to run at 16.5m, it is with the caveat of a 12m limit from the kingpin to the extreme rear of the trailer, and an ISO front swing radius of 2.04m.
The revised rules marked the end of the road for the long-kingpin trailers and short-cab tractors which were developed to get maximum load space under the old 15.5m limit. Instead we are seeing a new breed of semi-trailers up to 13.6m long which are more than adequate for dry freight hauliers, enabling them to carry up to 26 1,200x1,000mm (metric), or 33 1,200x800mm (Euro) pallets.
Obviously with dry freight there is no requirement for insulation materials at the front or the rear, or any need to worry about air flow round the cargo.
Try applying the same loading logic to a reefer and the theory starts to fall apart. There is simply not enough room for 26 or 33-pallet loading (see diagrams A and B) if there is to be an adequate air flow gap at the front and rear, and between the pallets, as well as adequate insulation at the front and rear of the body. In fact you would be hard pressed to squeeze 33 Euro pallets into a controlled-temperature semi, even discounting those essential air gaps.
A quick glance at the plan views shows the problems. The dimensional layout within both diagrams assumes no overlap of any product loaded on to a pallet. Unfortunately life isn't that simple. As reefer operators know to their cost, pallets are often badly loaded with bulges and overhangs that prevent the smooth flow of air between them.
Then there is the matter of the 10m air gap, which is insufficient for a decent air flow. What's more the 14mm air gap between the last row of metric pallets and rear doors (diagram A) is also insufficient for an adequate air flow return.
Finally the dimensional layout of the 33 pallet trailer (diagram B) ignores the requirement to keep the fridge unit within the 2.04m swing radius indicating an overlap between the rear door and the air gap at the final row of pallets. Quite simply the loading deck is too short.
FREE AIR VOLUME
Looking back at the changes in vehicle legislation over recent years, it is interesting to compare the amount of free air volume between 19, 24 and 26-pallet reefers, as indicated in Chart 1 (the comparisons are based on 1,200 x 1,000mm metric pallets). Not surprisingly, as the load being carried has increased, the free air space available to control the load environment has decreased.
All of which begs the question, how is the reefer operator to ensure adequate air flow around his cargo? A longer trailer would certainly solve the problem, but this would infuriate the environmental groups.
Diagrams C and D indicate the ideal metric and Euro-pallet loading solutions based on a 17m artic with a maximum swing radius kingpin-to-front-of-trailer dimension of 2,040mm; a 12.5m dimension from the kingpin to the extreme rear of the trailer; and a minimum dimension from the kingpin to the inside face of the rear doors of 12m (as opposed to the current back of trailer interpretation) assuming a 185mm door thickness and the minimum necessary air gap.
By adding 500min to the overall length the air gap between pallets is significantly improved to 25mm with metric pallets, and 15min with Euro pallets.
So much for the ideal: what of a more realistic compromise solution? The halfway options based on a 16.75m rig are shown in diagrams E and F. This option also assumes a maximum swing radius kingpin-to-front-of-trailer of 2,040mm, but there would also have to be a 250min tolerance on the maximum 12m kingpinto-inside face of rear door dimension to accommodate door thickness and door furniture.
As can be seen in diagram F the compromise solution also entails downloading to 32 Euro pallets as with 33 there is insufficient air volume for air-flow purposes.
Following on from the previous free air volume analysis, Chart 2 shows what is
run with a longer rig there is a danger of suspension overloading because the maximum trailer wheelbase (kingpin-tocentreline of suspension) to accommodate the turning circle is about 7.8m. This pushes up the suspension loads and reduces kingpin loads particularly in the UK which still retains the 10.5-tonne drive axle.
This type of layout dictates a relatively
long trailer rear overhang of about 4.2m (a dimension taken from the centreline of the suspension to the extreme rear of the trailer) because any additions to overall length can only be made behind the kingpin, thereby maintaining the proper ISO swing radius and protecting cab depth dimensions. If reefer operators
• were to get longer trucks there would be a strong case for special turning circle requirements.
Obviously any increase in operating weights would be welcomed, whether it be to 40 tonnes — where a 2+3 combination offers the best flexibility — or to 44 tonnes where a 3+3 rig, which would be a sensible arrangement for weight distribution, overcomes any "weight out" before "cube out" problems experienced with 40 tonnes on five axles.
It is also worth remembering that some of the available internal length will be used up whenever moving bulkheads are fitted, regardless of the final length, so any length increase would have to accommodate this practice.
So what is the best solution for both reefer operators and consumers? The answer breaks dawn into four major legislation considerations:
El Longer overall reefer lengths (17 or 16.75m) to ensure product protection through optimum air flow.
D The use of 11-tonne tractor drive axles to improve weight distribution.
LI Dispensation from the existing turning circle requirements, or a new turning circle band designed specifically for temperature-controlled artics ID The rapid adoption of a 40-tonne GCW limit for domestic UK operation on five axles, bringing the UK into line with mainland Europe and improving overall operating efficiency.
These four key items are inextricably linked and would not only provide consumer benefits in terms of guaranteed food safety, particularly at a time when the transport of temperature-controlled goods is coming under increasing public scrutiny and with the advent of new health regulations in April. They would also offer greater flexibility and lower costs per tonne to operators. Food for thought? • Your article on diesel bunkering (CM 17-23 January) states that to incorporate data from a customer's own in-house bulk storage tank Overdrive requires that electronic fuel management equipment is used.
This is not the case. Overdrive collects proportionately more transactions electronically from its 11,000 retail sites than any other multi-branded fuel card, which helps with speed and accuracy, but it is still punching in by hand thousands of manual vouchers every day. It can easily punch in the customer's manual record of issues from his bulk storage tank.
Overdrive will only recommend electronic fuel management when it believes it is economic for the customer. The company has links with all the major equipment suppliers (but is tied to none) and will recommend the best value for money equipment for each specific application. If, and only if, a customer wants Overdrive to help him with the funding it will do so at a cost which is no higher than if the customer bought or leased the equipment directly.
Overdrive is in the fuel management business, not the fuel or equipment supply business. However it is willing to manage these services for its customers as part of the "Total Fuel Management" package. P Brown, Managing director, Overdrive Bunketfuel.
AERODYNAMICS EXPERIENCE
• Catching up on my reading I finally looked at your interesting article on the aerodynamic changes to TNT artics (CM 25-31 October).
Many years ago, during one of the fuel crises in the 1970s when aerodynamic add-ons first began to become popular, I carried out a series of tests at MIRA using a one-fifth scale model of a 15m artic van.
We tested every aerodynamic device anybody could think of, adding them to the cab and/or the trailer. Certainly since then nothing has appeared which we had overlooked except for the concept of relieving the sides of roof towards the rear end to reduce the extent of the low pressure area behind the vehicle.
The problem with all such tests is that they are carried out with the air flow directly on the front of the cab. This means they are relevant only when the vehicle is running on its own (without turbulence from other vehicles) either in dead still air or against a wind which backs and veers to coincide with changes of direction as the truck moves.
Side winds and other traffic create changes in the actual drag. It would probably be possible to achieve the sort of fuel saving mentioned in the article by cover ing the motorway part of the journey right up behind the preceeding vehicle.
The problem with crosswinds is more quantifiable. The drag is proportional — not just to drag coefficient but to the frontal area as well.
In my MIRA tests none of the devices had any significant effect once the incident wind direction was more than r from dead ahead. At that stage the aerodynamic frontal area for a 2.5m wide by 4.2m high by 15m long artic has, increased approximately from 10.5m2 to 18.1m2. Believe me, there is nothing you can do by Cd reduction to offset that de facto increase in area. To give some idea of just what this means — for a truck travelling at 62mph (100 lan/h) a side-wind square on at 7.63mph (12.28 km/h) is enough to do the trick.
The necessary wind-speed to produce the shift in relative direction is slightly less if the cross-wind is behind square and slightly more if it is in front. On the other hand, drag is proportional to the square of the relative wind speed, which is obviously higher if the wind is in front of square.
I don't doubt that the relief produces good results on a nice shiny wind-tunnel model but it seems to be part of the problem that aerodynamics testing, initiated by the aircraft industry, is based on aircraft techniques.
I may be somewhat maligning the testers involved, but a realistic programme would have to include the effect of wind yaw and adjacent vehicles, and be carried out at full scale.
Having said that, the most effective device arising from our MIRA tests is still not being used, depite the fact that it was among the cheapest and lightest and did