s the carrot big enough?
Page 55
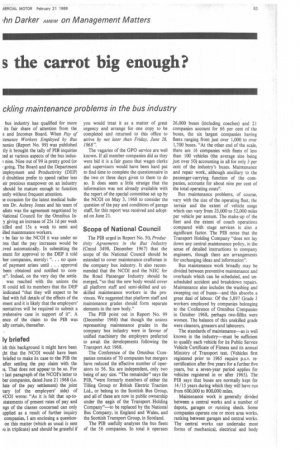
Page 56
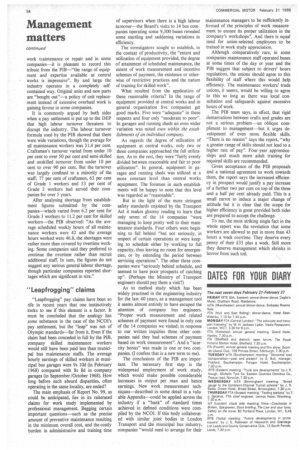
If you've noticed an error in this article please click here to report it so we can fix it.
ckling maintenance problems in the bus industry
bus industry has qualified for more its fair share of attention from the s and Incomes Board. When Pay of lenance Workers Employed by Bus 'antes (Report No. 99) was published tly it brought the tally of PIB inquiries ted at various aspects of the bus indus: nine. Nine out of 99 is pretty good (or I going. The Board and the Department ,inployment and Productivity (DEP) S doubtless prefer to spend rather less eir precious manpower on an industry should be mature enough to function ently without frequent attention.
ie occasion for the latest medical bulleom Dr. Aubrey Jones and his team of alias was the agreement negotiated by 4ational Council for the Omnibus Iny giving an increase of 25s Id per week killed and 15s a week to semi and died maintenance workers.
be fair to the NCOI it was under no Dm that the pay increases would be Dyed automatically. In submitting the meat for approval to the DEP it told bar companies, sternly: ". . . no quesof payment arises until . . . approval been obtained and notified to come. Indeed, on the very day the settle
was reached with the unions the )I could tell its members that the DEP indicated "that they will expect to be lied with full details of the effects of the anent and it is likely that the employers' :sentatives will be required to submit a arehensive case in support of it". A ence of the claim to the PIE was ally certain, thereafter.
ly briefed
ith this background it might have been dht that the NCOI would have been briefed to make its case to the PIB the after settling the pay claim with the is. That does not appear to be so. For : last paragraph of the NCOI's letter to ber companies, dated June 21 1968 (i.e. late of the pay settlement) the joint Lary (of the employers' side) of 4C01 wrote: "As it is felt that up-tostatements of present rates of pay and ngs of the classes concerned can only applied as a result of further inquiry companies, I am enclosing a questionon this matter (which as usual is sent ai in triplicate) and should be grateful if you would treat it as a matter of great urgency and arrange for one copy to be completed and returned to this office to arrive by not later than Friday, June 18, 1968".
The vagaries of the GPO service are well known. If all member companies did as they were bid it is a fair guess that wages clerks and supervisors would have been hard put to find time to complete the questionnaire in the two or three days given to them to do so. It does seem a little strange that the information was not already available with the report of the special committee set up by the NCOI on May 3, 1968 to consider the question of the pay and conditions of garage staff, for this report was received and adopted on June 21.
Scope of National Council
The PIB urged in Report No. 50, Productivity Agreements in the Bus Industry (Cmnd 3498, December 1967) that the scope of the National Council should be extended to cover maintenance craftsmen in the company bus industry. It also recommended that the NCOI and the NJIC for the Road Passenger Industry should be merged, "so that the new body would cover all platform staff and semi-skilled and unskilled maintenance workers in the provinces. We suggested that platform staff and maintenance grades should form separate elements in the new body."
The PIE point out in Report No. 99 (December 1968) that though the unions representing maintenance grades in the company bus industry were in favour of unified machinery the employers preferred to await the developments following the Transport Act 1968.
The Conference of the Omnibus Companies consists of 70 companies but mergers have reduced the effective number of operators to 56. Six are independent, only two being of any size, "The remainder" says the PIE, "were formerly members of either the Tilling Group or British Electric Traction Ltd., or belong to the Scottish Bus Group, and all of these are now in public ownership under the aegis of the Transport Holding Company"—to be replaced by the National Bus Company, in England and Wales, and the Scottish Transport Group, in Scotland.
The PIB usefully analyses the bus fleets of the 56 companies. In total it operates
26,000 buses (including coaches) and 21 companies account for 66 per cent of the buses, the six largest companies having fleets ranging from just over 1,000 to over 1,700 buses. "At the other end of the scale, there are 16 companies with fleets of less than 100 vehicles (the average size being just over 50) accounting in all for only 3 per cent of the industry's buses. Maintenance and repair work, although ancillary to the passenger-carrying function of the companies, accounts for about nine per cent of the total operating costs".
Bus maintenance problems, of course, vary with the size of the operating fleet, the terrain and the extent of vehicle usage which can vary from 23,000 to 52,000 miles per vehicle per annum. The make-up of the fleet and the extent of coach operations compared with stage services is also a significant factor. The PIE notes that the Transport Holding Company "does not lay down any central maintenance policy, in the sense of detailed instructions to company engineers, though there are arrangements for exchanging ideas and information".
Bus maintenance work broadly may be divided between preventive maintenance and overhauls which can be scheduled, and unscheduled accident and breakdown repairs. Maintenance also includes the washing and sweeping out of buses—and this absorbs a great deal of labour. Of the 5,897 Grade 3 workers employed by companies belonging to the Conference of Omnibus Companies in October 1968, perhaps two-fifths were women. The balance of this unskilled grade were cleaners, greasers and labourers.
The standards of maintenance—as is well known in the industry—must be sufficient to qualify each vehicle for its Public Service Vehicle Certificate of Fitness and its annual Ministry of Transport test. (Vehicles first registered prior to 1965 require p.s.v. recertification after five years for a further five years, but a seven-year period applies for vehicles registered in or after 1965). The PIE says that buses are normally kept for 14/15 years during which they will have run from 600,000 to 800,000 miles.
Maintenance work is generally divided between a central works and a number of depots, garages or running sheds. Some companies operate one or more area works, ranking between garages and central works. The central works can undertake most forms of mechanical, electrical and body work maintenance or repair and in some companies—it is pleasant to record this tribute from the PIB—"the range of equipment and expertise available at central works is impressive". By and large the industry operates in a completely selfcontained way. Original units and new parts are "bought out"—a policy of unit replacement instead of extensive overhaul work is gaining favour in some companies.
It is commonly argued by both sides when a pay settlement is put up to the DEP that high labour turnover threatens to disrupt the industry. The labour turnover formula used by the PIB showed that there were wide variations, though the average for all maintenance workers was 31.4 per cent. Craftsmen's turnover varied from under 10 per cent to over 50 per cent and semi-skilled and unskilled turnover from under 10 per cent to over 90 per cent. But the turnover was largely confined to a minority of the staff; 77 per cent of craftsmen, 63 per cent of Grade 1 workers and 53 per cent of Grade 2 workers had served their companies for over 5 years.
After analysing shortage from establishment figures submitted by the companies—which varied from 6.2 per cent for Grade 3 workers to 11.2 per cent for skilled workers—the PIB observed: "As the average scheduled weekly hours of all maintenance workers were 42 and the average hours worked were 46.8, the shortages were rather more than covered by overtime working. Some companies said they preferred to continue the overtime rather than recruit additional staff. In sum, the figures do not suggest any serious general labour shortage, though particular companies reported shortages which are significant in size."
"Leapfrogging" claims
"Leapfrogging" pay claims have been so rife in recent years that one instinctively looks to see if this element is a factor. It must be concluded that the analogy has some substance in the case of the NCOI's pay settlement, but the "leap" was not of Olympic standards—far from it. Even if the claim had been conceded in full by the PIB, company skilled maintenance workers would still have been paid less than municipal bus maintenance staffs. The average hourly earnings of skilled workers in municipal bus garages were 9s 10d (in February 1968) compared with 8s 8d in company garages (in September/October 1968). How long before such absurd disparities, often operating in the same locality, are ended?
The main emphasis of Report No. 99, as could be anticipated, lies in its reiterated claims for work study implemented by professional management. Begging certain important questions—such as the precise amount of preventive maintenance resulting in the minimum overall cost, and the costly burden in administrative and training time of supervisors when there is a high labour turnover—the Board's visits to 14 bus com panies operating some 9,300 buses revealed some startling and saddening variations in efficiency.
The investigators sought to establish, in the context of productivity, the "extent and utilization of equipment provided, the degree of attainment of scheduled maintenance, the extent of work measurement and incentive schemes of payment, the existence or otherwise of restrictive practices and the nature of training for skilled work".
What resulted from the application of these reasonable criteria? In the range of equipment provided at central works and in general organization five companies get
good marks. Five were "adequate" in these respects and four only "moderate to poor". In garages and running sheds an even wider variation was noted even within the establishments of an individual company.
As regards the degree of utilization of equipment at central works, only two or three companies approached the full utilization. As to the rest, they were "fairly evenly divided between reasonable and fair to poor utilization". In general, equipment in garages and running sheds was utilized at a more constant level than central works equipment. The foremen in such establishments will be happy to •note that this level was regarded as "reasonable".
But in the light of the more stringent safety standards enjoined by the Transport Act it makes gloomy reading to learn that only seven of the 14 companies "were managing to keep pretty well to their maintenance standards. Four others were beginning to fall behind "but not seriously, in respect of certain operations or were keeping to schedule either by working to full capacity, thus leaving no room for emergencies, or by extending the period between servicing operations". The other three companies were "seriously behind schedule, and seemed to have poor prospects of catching up". (Perhaps the Ministry of Transport engineers should pay them a visit?) As to method study which has been widely practised in the engineering industry for the last 40 years, as a management tool it seems almost entirely to have escaped the attention of company bus engineers. "Proper work measurement and related schemes of payment were found in only one of the 14 companies we visited; in response to our written inquiries three other companies said they had schemes of payment based on work measurement". And a "scarcity bonus" was made in one or two companies. (I confess that is a new term to me).
The conclusions of the PIB are important. The necessary first step is the widespread employment of work study, which would make possible considerable increases in output per man and hence earnings. New work measurement techniques—described in some detail in a valuable Appendix—could be applied across the industry if a "bank" of standard times achieved in defined conditions were compiled by the NCOI. If this body collaborated with similar joint bodies in London Transport and the municipal bus industry, companies "would need to arrange for their maintenance managers to be sufficiently informed of the principles of work measurement to ensure its proper utilization in the company's workshops". And there is equal need for union-selected employees to be trained in work study appreciation.
Although comparatively rare, in some companies maintenance staff operated buses at some times of the day or year and the KB suggest that subject to drivers' hours regulations, the unions should agree to this flexibility of staff where this would help efficiency. The maintenance workers' trade unions, it seems, would be willing to agree to this so long as there was local consultation and safeguards against excessive hours of work.
The PIB team says, in effect, that rigid demarcations between crafts and grades are not a serious problem—an oblique compliment to management—but it urges development of even more flexible skills. "There is no reason" says the report, "why a greater range of skills should not lead to a higher rate of pay". Four-year apprenticeships and much more adult training for required skills are recommended.
Given acceptance of the PIB proposals and a national agreement to work towards them,, the report says the increased efficiency in prospect would justify a pay increase of a further two per cent on top of the three and a half per cent already paid. This is a small carrot to induce a major change of attitude but it is clear that the scope for higher efficiency is great provided both sides are prepared to accept the challenge.
To me, the most striking single fact in the whole report was the revelation that some workers are allowed to put in more than 43 hours a week overtime. They deserve every penny of their £35 plus a week. Still more they deserve management which shrinks in horror from such toil.