What are the Chances of Low-compression Oil Engines?
Page 46
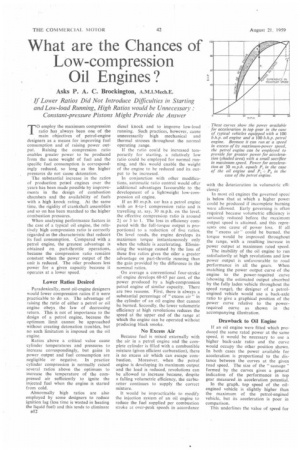
Page 47
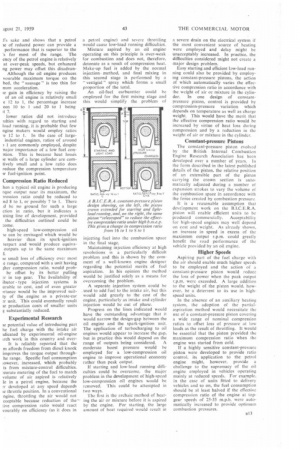
If you've noticed an error in this article please click here to report it so we can fix it.
Asks P. A. C. Brockington, A.M.I.Mech.E.
If Lower Ratios Did Not Introduce Di.,(ficulties in Starting and Low-load Running, High Ratios would be Unnecessary : Constant-pressure Pistons Might Provide the Answer TO employ the maximum compression ratio has always been one of the main objectives of petrol-engine designers as a means for improving fuel consumption and of raising power output. Raising the compression ratio enables greater power to be produced from the same weight of fuel and the specific fuel consumption is correspondingly reduced, so long as the higher pressures do not cause detonation. The substantial increase in the ratios of production petrol engines over the years has been made possible by improvements in the design of combustion chambers and the availability of fuels with a high knock rating. At the same time, the rigidity of crankshaft assemblies and so on has been matched to the higher combustion pressures. When analysing performance factors in the case of a typical oil engine, the relatively high compression ratio is correctly regarded as the characteristic that reduces its fuel consumption. Compared with a petrol engine, the greatest advantage is obtained on part-throttle operations, because the compression ratio remains constant when the power output of the unit is reduced. The oiler produces less power for a given capacity because it operates at a lower speed.
Lower Ratios Desired • Paradoxically, most oil-engine designers would lower compression ratios if it were practicable to do so. The advantage of raising the ratio of either a petrol or oil engine obeys the law of decreasing return. This is not of importance to the design of a petrol engine, because the optimum limit cannot be approached without creating detonation troubles, but no such limitation is imposed on the oil engine.
Ratios above a critical value cause cylinder temperatures and pressures to increase correspondingly, but gains in power output and fuel consumption are negligible or negative. In practice cylinder compression is normally raised several ratios above the optimum to increase the temperature of the compressed air sufficiently to ignite the injected fuel when the engine is started from cold. Abnormally high ratios are also employed by some designers to reduce ignition lag (less time is wasted in heating the liquid fuel) and this tends to eliminate B12 diesel knock and to improve low-load running. Such practices, however, cause unnecessarily high mechanical and thermal stresses throughout the normal operating range. If the ratio could be increased temporarily for starting, a relatively low ratio could be employed for normal running, and this would enable the weight of the engine to be reduced and its output to be increased. In conjunction with other modifications, automatic ratio control would offer additional advantages favourable to the development of a lightweight low-compression oil engine.
If an 80 m.p.h. car has a petrol engine with an 8-to-1 compression ratio and is travelling at, say, 30 m.p.h. on the level, the effective compression ratio is around 2; or 3 to 1. The Toss in efficiency compared with the full-torque output is proportional to a reduction of five ratios. On level roads, the engine develops its maximum torque instantaneously only when the vehicle is accelerating. Eliminating the wastage caused by the loss of these five ratios gives the oiler a greater advantage on part-throttle running than the gain provided by the difference in the nominal ratios.
On average a conventional four-stroke oil engine develops 60-65 per cent. of the power produced by a high-compression petrol engine of similar capacity. There are two reasons. First, there is always a substantial percentage of "excess air" in the cylinder of an oil engine that cannot be burned. Secondly. the lower volumetric ev ev efficiency at high revolutions reduces the speed at the upper end of the range at which the engine can be operated without producing black smoke.
No Excess Air
Because fuel is mixed externally with the air in a petrol engine and the complete cylinder is filled with a combustible mixture (given efficient carburation), there is no excess air which can escape combustion. Moreover, when the petrol engine is developing its maximum output and the load is reduced, revolutions can be allowed to increase because, despite a falling volumetric efficiency, the carburetter continues to supply the correct mixture.
It would he impracticable to modify the injection system of an oil engine to reduce the fuel supplied per combustion stroke at over-peak speeds in accordance with the aeterioration in volumetric effi. ciency. In most oil engines the governed speed is below that at which a higher power could be produced if incomplete burning wece allowed. Early governing is often required because volumetric efficiency is seriously reduced before the maximum output speed is attained, and this represents one cause of power loss. If all the "excess air could be burned, the torque would be improved throughout the range, with a resulting increase in power output at maximum rated speed.
The inability of the oil engine to run satisfactorily at high revolutions and low power output is unfavourable to road performance in all the gears. When matching the power output curve of the engine to the power-required curve (showing the estimated output absorbed by the fully laden vehicle throughout the speed range), the designer of a petrolengined vehicle would use a back-axle ratio to give a graphical position of the power curve relative to the powerrequired curve as shown in the accompanying illustration.
Drawback to Oil Engine
n
If an oil engine were fitted which produced the same rated power at the same speed, it would be necessary to use a axle ratio and th higher back-e curve would occupy the other position shown. In both cases the power available for acceleration is proportional to the distance between the curves at the given road speed. The size of the " sausage " formed by the curves gives a general indication of the performance in top gear measured in acceleration potential. In the graph, top speed of the oilengined vehicle is slightly higher than the maximumof the petrol-engined vehicle, but its acceleration is poor in comparison.
This underlines the value of speed for Ts sake and shows that a petrol se of reduced power can provide a performance that is superior to the 's for most of the range. The ency of the petrol engine is relatively at over-peak speeds, but enhanced rig power may offset this disadvan Although the oil engine produces vourable maximum torque on the bed, the " sausage " is too thin for num acceleration.
le gain in efficiency by raising the of an oil engine is relatively small e 12 to I, the percentage increase een 10 to l and 20 to I being tt 7, lower ratios did not introduce 'ulties with regard to starting and load running, it is probable that few nine makers would employ ratios e 12 to I. In the case of largeindustrial engines, ratios of around )I are commonly employed, despite najor importance of a low fuel con)tion. This is because heat losses le walls of a large cylinder are cornLively small small and a low ratio does reduce the compression temperature w fuel-ignition point.
Compression Ratio Reduced
hen a typical oil engine is producing rque output near its maximum, the )ression ratio could be reduced to nd 8 to 1, or possibly 7 to 1. There d be no ground for such a large ction in ratio, but it indicates a using line of development, provided the difficulties outlined could be come.
high-speed low-compression oil le can be envisaged which would be heavier than its spark-ignition terpart and would produce equivaoutputs up to the same maximum re small loss of efficiency over most e range, compared with a unit having her compression ratio, would probbe offset by its better pulling :r in top gear. The availability of ibutor type injection systems is urable to cost, and of even greater 'Mance would be the improved suitty of the .engine as a private-car )r. unit. This could eventually result le production costs of smaller units substantially reduced.
Experimental Research
re potential value of introducing part tie fuel charge with the intake air idicated by experimental oil-engine Feb work in this country and over It is reliably reported that the m affords freedom from diesel knock improves the torque output throughhe range. Specific fuel consumption iowever, increased, which probably ts from mixture-control difficulties. :curate metering of the fuel to match volume of air aspired is relatively le in a petrol engine, because the :r developed at any speed depends le throttle position. In a conventional ngine, throttling the air would not cceptable because reduction of the tive compression ratio would react vourably on efficiency (as it does in a petrol engine) and severe throttling would cause low-load running difficulties.
Mixture aspired by an oil engine operating on this principle is over-weak for combustion and does not, therefore, detonate as a result of compression heat. Make-up fuel is added by the normal injection, method, and final mixing in this second stage is performed by a "vestigial" spray which forms a small proportion of the total.
An oil-fuel carburetter could be employed for the first mixing stage and this would simplify the problem of injecting fuel into the combustion space in the final stage.
Maintaining injection efficiency at high revolutions is a particularly difficult problem and this is shown by the comment of a well-known engine designer regarding the potential merits of fuel aspiration. In his opinion the method would be justified solely as a means for overcoming the problem.
A separate injection system could be . used to add fuel to the intake air, but this would add greatly to the cost of the engine, particularly as intake and cylinder injection would be out of phase.
Progress on the lines indicated would have the outstanding advantage that it would narrow the design-gap between the oil engine and the spark-ignition unit. The application of turbocharging to oil engines would appear to increase the gap, but in practice this would depend on the range of outputs being considered. A moderate boost pressure would be employed for a low-compression oil engine to improve operational economy rather than peak output.
If starting and low-load running difficulties could be overcome, the major problem in the development of high-speed low-compression oil engines would be removed. This could. be attempted in two ways.
The first is the archaic method of healing the air or mixture before it is aspired by the engine. For starting. the large amount of heat required would result in a severe drain on the electrical system if the most convenient source of heating were employed and delay might be unacceptably increased, In practice, the difficulties considered might not create a major design problem.
Easy starting and efficient low-load running could also be provided by employing constant-pressure pistons, the action of which automatically varies the effective compression ratio in accordance with the weight of air or mixture in the cylinder. In one design of constantpressure piston, control is provided by compression-pressure variation which depends on temperature as well as charge weight. This would have the merit that the effective compression ratio would be increased by virtue of heat loss during compression and by a reduction in the weight of air or mixture in the cylinder.
Constant-pressure Pistons The constant-pressure piston evolved by the British Internal Combustion Engine Research Association has been developed over a number of years. In the form described in the latest published details of the piston, the relative position of an extensible part of the piston carrying the crown section is automatically adjusted during a number of expansion strokes to vary the volume of the combustion space in accordance with the force created by combustion pressure.
It is a reasonable assumption that development work on the B.1.C.E.R.A. piston will enable efficient units to be produced commercially. Acceptability For high-speed engines may well depend on cost and weight. As already shown, an increase in speed in excess of the maximum output r.p.m. could greatly benefit the road performance of the vehicle provided by an oil engine.
Higher Speeds
Aspiring part of the fuel charge with the air should enable much higher speeds to be employed and the action of a constant-pressure piston would reduce the loss of power when the peak output r.p.m. were exceeded. A large addition to the weight of. the piston would, however, be a deterrent to its use •in highspeed units.
In the absence of an auxiliary heating system, the adoption of the partialaspiration method would necessitate the use of a constant-pressure piston covering a wide range of nominal compression ratios to offset loss of pressure at low loads as the result of throttling. It would be essential that the piston provided the maximum compression ratio when the engine was started from cold.
If a highly sensitive constant-pressure piston were developed to provide ratio control, its application to the petrol engine might, however, provide a challenge to the supremacy of the oil engine employed in vehicles operating mainly at reduced speeds. For example. in the case of units fitted to delivery vehicles and so on, the fuel consumption should be at least halved if the effective compression ratio of the engine at topgear speeds of 25-35 m.p.h. were automatically increased to provide optimum combustion pressures.