The Latest Technique in
Page 38
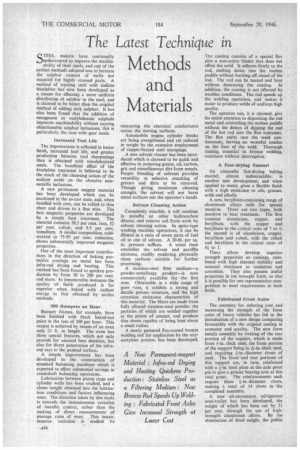
Page 41
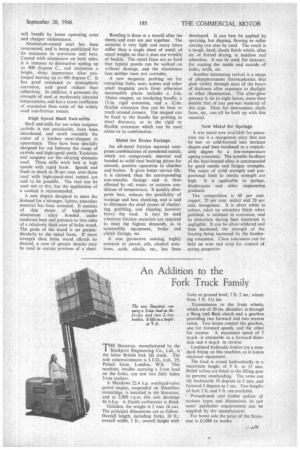
If you've noticed an error in this article please click here to report it so we can fix it.
Methods and Materials
STEEL makers have continually endeavoured to improve the machinability of their steels, and one of the earliest methods adopted was to increase the sulphur content of melts not required for highly stressed parts. A method of treating steel with sodium bisulphite has now been developed as a means for effecting a more uniform distribution of sulphur in the steel, and is claimed to be better than the original method of adding stick sulphur. It has also been found that the addition of manganese or molybdenum sulphide improves machinability without causing objectionable sulphur inclusions; this is particularly the case with gear steels.
Increased Tool Life The improvement is reflected in better finish, increased tool life, and greater production between tool sharpenings than is obtained with unsulphurized steels. The beneficial effect of the bisulphite treatment is believed to be the result of the cleansing action of the sodium oxide on the abrasive nonmetallic inclusions.
A new permanent magnet material has been developed which can be machined in the as-cast state, and, when handled with care, can be rolled to thin sheet and drawn to a fine wire. The best magnetic properties are developed by a simple heat treatment. The material contains 38.5 per cent. iron, 52 per cent, cobalt, and 9.5 per cent. vanadium. A similar composition, coldworked to 75-95 per cent, reduction, shows substantially improved magnetic properties.
One of the most important contributions in the direction of baking protective coatings on metal has been infra-red drying and heating. This method has been found to quicken production by from 50 to 200 per cent. and more. In innumerable instances the quality of finish produced is far superior when baked with radiant energy to that obtained by earlier methods.
300 Bumpers an Hour Bumper frames, for example, have been finished with black baked-out paint at the rate of 300 per hour. This output is achieved by means of an oven only 21 ft. in length. The oven has three special features, which not only provide for unusual heat densities, but also for direct penetration of the infrared rays to the painted surface.
A simple improvement has been developed in the construction of standard balancing machines which is expected to effect substantial savings in crankshaft balancing operations.
Lubrication between piston rings and cylinder walls has been studied, and a closer insight obtained into the lubrication conditions and factors influencing wear. The direction taken by this study is towards the instantaneous variation of metallic contact, rather than the making of direct measurements of average rates of wear. This instantaneous variation is studied by measuring the electrical conductance across the moving surfaces.
Automobile engine cylinder blocks are being strengthened and yet reduced in weight by the extensive employment of copper-brazed steel stampings.
A new solvent cleaner has been introduced which is claimed to be quick and effective in removing grease, oil, carbon, grit and miscellaneous dirt from metals. Proper blending of solvents provides versatility in selective attacking of greases and dirts to be removed. Though giving maximum cleaning strength, the solvent will not harm metal surfaces nor the operator's hands.
Solvent Cleaning Action Completely miscible, it will combine in paraffin or other hydrocarbon diluent, and remove soil from work by solvent cleaning action. In spray-type washing machine operations, it can be diluted in a ratio of seven parts of fuel oil to one of solvent. A 20-lb. per sq.
in. pressure suffices. A water rinse emulsifies the solvent and paraffin mixtures, readily rendering physically clean surfaces suitable for further processing.
A stainless-steel filter medium—a powder-metallurgy product—is now commercially available for the first time. Obtainable in a wide range of pore izes, it exhibits a strong and ductile porous structure, and the high corrosion resistance characteristic of this material. The filters are made from fully alloyed stainless-steel powder, the particles of which are welded together at the points of contact, and produce thin sheets capable of being bent about a small radius.
A newly patented flux-coated bronze welding rod for application by the oxyacetylene process, has been developed. The coating consists of a special flux plus a non-active binder that does not affect the weld. It adheres firmly to the rod, melting down into the molten puddle without burning off ahead of the , rod. The rod can be heated and bent without • destroying the coating. In addition, the coating is not affected by weather conditions. The rod speeds up the welding operation, and makes it easier to produce welds of uniform high quality.
The operator can, it is claimed, give his entire attention to depositing the rod metal and controlling the molten puddle without the delays of dipping the end of the hot rod into the flux container. The flux melts into the weld continuously, leaving no wasteful residue on the face of the weld. Thorough tinning, essential to bronze welding, continues without interruption.
A Fast-drying Enamel
An unusually fast-drying baking enamel, almost indestructible,' is another new development, and when applied to metal, gives a flexible finish with a high resistance to oils, greases, acids and alkalis.
A new, beryllium-containing range of aluminium alloys calls for special mention. There are two types, both sensitive to heat treatment. The first contains aluminium, copper, and beryllium, with the copper and beryllium in the critical ratio of 7 to 1; the second is of aluminium, copper, beryllium and cobalt, with the cobalt and beryllium in the critical ratio of 6i to I.
Thes5 alloys develop superior strength properties as castings, combined with high thermal stability and unusual resistance to oxidation and corrosion. They also possess useful properties in tne wrought form, so that it is possible for one representative composition to meet requirements in both fields.
Fabricated Front Axles
The necessity for reducing cost and increasing the strength of the front axles of heavy vehicles has led to the introduction of a new design comparing favourably with the original casting in economy and quality. The new form entails assembly by riveting of the rear portion of the support, which is made from 1-in. thick steel, the front portion of the support being in -P-in.-thick steel, and requiring i-in.-diameter rivets of steel. The front and rear portions of this support are, in turn, reinforced with a i-in, steel plate at the axle pivot pin to give a greater bearing area at this vital point. The reinforcements each require three 11-in.-diameter rivets, making a total of 14 rivets in the completed assembly.
A new all-aluminium refrigerator semi-trailer has been developed, the weight of which has been cut by 5I per cent. through the use of highstrength aluminium alloys. By the elimination of dead weight, the public will benefit by lower operating costs and cheaper maintenance.
Aluminium-coated steel has been resurrected, and is being publicized for its resistance to corrosion and heat. Coated with aluminium on both sides, it is immune to destructive scaling up to 800 degrees C., and maintains a bright, shiny appearance after prolonged heating up to 480 degrees C. It has good resistance to atmospheric corrosion, and good radiant heat reflectivity. In addition, it possesses the strength of steel at moderately elevated temperatures, and has a lower coefficient of.expansion than some of the widely used non-ferrous metals.
High Speed Shell End-n;ills
Shell end-mills for use when tungsten carbide is not practicable, have been introduced, and much resemble the cutter of a kitchen meat-chopper in appearance. They have been specially designed for use between the range of carbide and high-speed steels. Tantalum and tungsten are the alloying elements used. These mills work best at high speeds with rapid feeds. Speeds and feeds as much as 50 per cent, over those used with high-speed-steel cutters are said to be possible. The tool can be used wet or dry, but the application of a coolant is recommended.
A new duplex designed to meet the demand for a'stronger, lighter, smoother material has been invented. It consists of thin sheets of high-strength aluminium alloy bonded under moderate heat and pressure to two sides of a relatively thick gore of balsa wood. The grain of the wood is set perpendicularly to the metal faces. If more strength than balsa 'wood affords be desired, a core of greater density may be used in certain portions of a sheet.
Bonding is done in a mould after the sheets and core are put together. The material is very light and many times stiffer than a single sheet of metal of equal weight, so that it does not wrinkle or buckle. The metal faces are so hard that typical panels can be walked on without damage, and the aluminium face neither rusts nor corrodes.
A new magnetic probing set for extracting bolts, nuts, screws and other small magnetic parts from otherwise inaccessible places includes a i-in. Alnico magnet, an insulating handle, a 12-in, rigid extension, and a 12-in.. flexible extension that can be bent to reach around Corners. The magnet can be fixed to the handle for probing in short distances, or to the rigid or flexible extension which can be used alone or in combination.
Metal for Brake Facings
An all-metal friction material comprises combinations of powdered metals, which are compressed, sintered and bonded to solid steel backing plates for smooth, positive operation in• clutches and brakes. It gives better service life, it is claimed, than the corresponding non-metallic facings and is little affected by oil, water, or extreme conditions of temperature. It quickly dissipates heat, reduces the possibility of warpage and heat checking, and is said to eliminate the chief causes of chattering, grabbing. and slipping, however heavy the load. It may be used wherever friction materials are required to meet the highest demands, as in automobile equipment, brake and clutch facings, etc.
A new protective coating, highly resistant to petrol, oils, alcohol solutions, acids, alkalis, etc., has been developed. It can best be applied by spraying, but dipping, flowing or roller coating can also be used. The result is a tough, hard, elastic finish which, after air or forced drying, is tasteless and odourless. It can be used, for instance, for coating the inside and outside of tanks, walls, etc.
Another interesting revival is a range of phosphorescent thermoplastics that glow visibly through most of the hours of darkness after exposure to daylight or other illumination. The after-glow potency is six to eight hours, more than double that of any pre-war material of this type. Dials for instruments, clock faces, etc., can all be built up with this material.
New Metal for Springs A war metal now available for peacetime use is a manganese alloy that can be hotor cold-formed into intricate shapes and then hardened to a remarkable degree by a low-temperature ageing treatment. The notable hardness of the heat-treated alloy is accompanied by good tensile and fatigue strengths. The ratios of yield strength and proportional limit to tensile strength are high. It is applicable to springs, diaphragms and other engineering products.
The composition is 60 per cent. copper, 20 per cent, nickel and 20 per cent. manganese. It is silver white in colour, takes an attractive finish when polished is resistant to corrosion, and its distortion during heat treatment is negligible. It can be silver-soldered and then hardened, the strength of the brazing being increased by the hardening treatment. Close tolerances can be held on wire and strip for control of spring properties