THE GAS TURBINE: Vhat are its usibilities for Road Vehicles?
Page 34
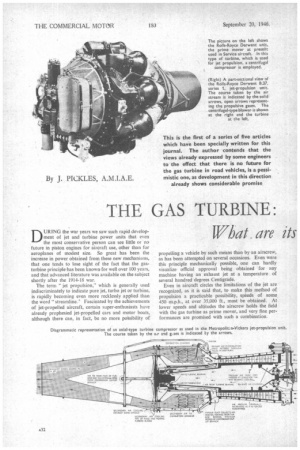
Page 35
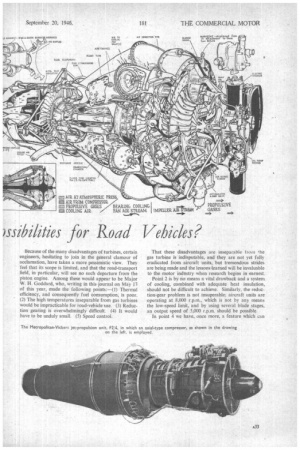
Page 36
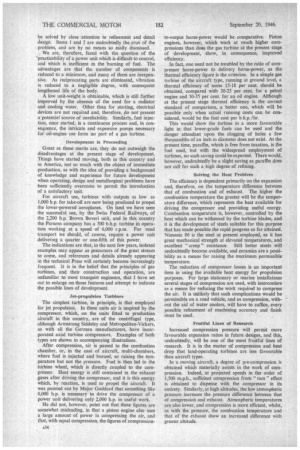
Page 37
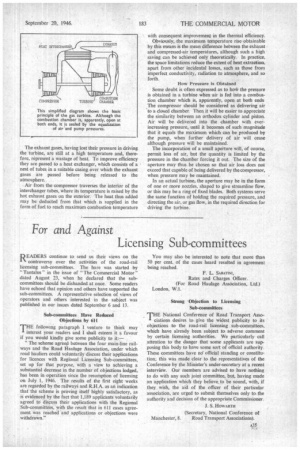
If you've noticed an error in this article please click here to report it so we can fix it.
DURING the war years we saw such rapid de‘ elopment of jet and turbine power units that even the most conservative person can see little or no future in piston engines for aircraft use, other than for aeroplanes of modest size. So great has been the increase in power obtained from these new mechanisms, that one tends to lose sight of the fact that the gasturbine principle,has been known, for well over 100 years, and that advanced literature was available on the subject shortly after the 1914-18 war.
The term "jet propulsion," which is generally used indiscriminately to indicate pure jet, turbo jet or turbine, is rapidly becoming even more recklessly applied than the word " streamline. ' Fascinated by the achievements of jet-propelled aircraft, certain super-enthusiasts have already prophesied jet-propelled cars and motor boats, although there can, in fact, be no more possibility of propelling a vehicle by such means than by an airscrew, as has been attempted on several occasions. Even were this principle mechanically possible, one can hardly visualize official approval being obtained for any machine having an exhaust jet at a temperature of several hundred degrees Centigrade.
Even in aircraft circles the limitations of the jet are recognized, as it is said that, to make this method of propulsion a practicable possibility, speeds of some 450 m.p.h., at over 35,000 ft., must be obtained. At lower speeds and altitudes the airscrew holds the field with the gas turbine as prime mover, and very fine performances are promised with such a combination.
Because of the many disadvantages of turbines, certain engineers, hesitating to join in the general clamour of acclamation, have taken a more pessimistic view. They feel that its scope is limited, and that the road-transport field, in particular, will see no such departure from the piston engine. Among these would appear to be Major W. H. Goddard, who, writing in this journal on May 17. of this year, made the following points:—(1) Thermal efficiency, and consequently fuel consumption, is poor. (2) The high temperatures inseparable from gas turbines would be impracticable for road-vehicle use. (3) Reduction gearing is overwhelmingly difficult. (4) It would have to be unduly small. (5) Speed control.
That these disadvantages are inseparable I roni 'he gas turbine is indisputable, and they are not yet fully eradicated from aircraft units, but tremendous strides are being made and the lessons-learned will be invaluable to the motor industry when research begins in earnest.
Point 2 is by no means a vital drawback and a system of cooling, combined with adequate heat insulation, should not be difficult to achieve. Similarly, the reduction-gear problem is not insuperable; aircraft units are operating at 8,000 r.p.m., which is not by any means the low-speed limit, and by using several blade stages, an output speed of 5,000 r.p.m. should be possible In point 4 we have, once more, a feature which can be solved by close attention to refinement and detail design. Items 1 and 5 are undoubtedly the crux of the problem, and are by no means so easily dismissed.
We are, therefore, faced with the question of the *practicability of a power unit which is difficult to control, and which is inefficient in the 'burning of fuel. The advantages are that the number of components is reduced to a minimum, and many of them are inexpensive. As reciprocating parts are eliminated, vibration is reduced to a negligible degree, with consequent lengthened life of the body.
A low unit-weight is obtainable, which is still further improved by the absence of the need for a radiator and cooling water. Other than for starting, electrical devices are not required and, therefore, do not present a potential source of unreliability. Similarly, fuel injection, once started, is a continuous process and, in consequence, the intricate and expensive pumps necessary for oil-engine use form no part of a gas turbine.
Development is Proceeding Great as these merits are, they do not outweigh the disadvantages at the present stage of development. Things have started moving, both in this country and in America, not so much with the object of immediate production, as with the idea of providing a background of knowledge and experience for future development when operating, design and metallurgical problems have been sufficiently overcome to permit the introduction of a satisfactory unit.
For aircraft use, turbines with outputs as low as 1,000 h.p. for take-off are now being produced to propel the lower-powered aeroplanes. On !and we have seen the successful use, by the Swiss Federal Railways, of the 2,200 h.p. Brown Boveri unit, and in this country the Parsons company has a 500 b.h.p. turbine in operation working at a speed of 6,000 r.p.m. For road transport we should, of course, require a power unit delivering a quarter or one-fifth of this power.
The indications are that, in the next few years, isolated examples may appear as precursors of the great stream to come, and references and details already appearing in the technical Press will certainly become increasingly frequent. It is in the belief that the principles of gas turbines, and their construction and operation, are unfamiliar to most transport engineers, that I have set out to enlarge on those features and attempt to indicate the possible lines of development.
Jet-propulsion Turbines The simplest turbine, in principle, is that employed for jet propulsion. In these units air is inspired by the compressor, which, on the units fitted to production aircraft in this country, are of the centrifugal type, although Armstrong Siddeley and Metropolitan-Vickers, as with all the German manufacturers, have incorporated axial turbine compressors. Examples of both types are shown in accompanying illustrations.
After compression, air is passed to the combustion chamber, or, in the case of aircraft, multi-chambers, where fuel is injected and burned, so raising the temperature but not the pressure. Fuel is then led to the turbine wheel, which is directly coupled to the compressor. Heat energy is still contained in the exhaust gases after driving the compressor, and it is this energy which, by reaction, is used to propel the aircraft. It was pointed out by Major Goddard that something like 8,000 h.p. is necessary to drive the compressor of a power unit delivering only 2,000 h.p. in useful work.
He did not, however, point out that these figures are somewhat misleading, in that a piston engine also uses a large amount of power in compressing the air, and that, with equal compression, the figures of compression s34 to-output horse-power would be comparative. Piston engines, however, which work at much higher compressions than does the gas turbine at the present stage of development, show, in consequence, improved efficiency.
In fact, one need not be troubled by the ratio of compressor horse-power to delivery horse-power, as the thermal efficiency figure is the criterion. In a simple gas turbine of the aircraft type, running at ground level, a thermal efficiency of some 15-18 per cent. should be obtained, compared with 20-25 per cent. for a petrol engine and 30-35 per cent. for an oil engine. Although at the present stage thermal efficiency is the correct standard of comparison, a better one, which will be possible only when actual running costs can be considered, would be the fuel cost per b.h.p./hr.
This would show the turbine in a more favourable light in that lower-grade fuels can be used and the danger attendant upon the clogging of holes a few thousandths of an inch in diameter does not exist. At the present time, paraffin, which is free from taxation, is the fuel used, but with the widespread employment of turbines, no such saving could be expected. There would, however, undoubtedly be a slight saving as paraffin does not call for such a high degree of refining..
Solving the Heat Problem The efficiency is dependent primarily on the expansion and, therefore, on the temperature difference between that of combustion and of exhaust. The higher the combustion temperature the greater will be the temperature difference, which represents the heat available for driving the compressor and providing useful energy. Combustion temperature is, however, controlled by the heat which can be withstood by the turbine blades, and it is the development of steels suitable for this purpose that has made possible the rapid progress so far attained. Nimonic 80 is the steel at present employed, as it has great mechanical strength at elevated temperatures, and excellent " creep " resistance. Still better steels will undoubtedly become available, and ceramics are a possibility as a means for raising the maximum permissible temperature.
The reduction of compressor losses is an important item in using the available heat energy for propulsion purposes. For large stationary or marine installations several stages of compression are used, with intercoolers as a means for reducing the work required to compress the air. It is unlikely that such complications would be permissible on a road vehicle, and as compression, without the aid of water coolers, will have to suffice, every possible refinement of machining accuracy and finish must be used.
Fruitful Lines of Research Increased compression pressure will permit more favourable expansion ratios in future designs, and this, undoubtedly, will be one of the most fruitful lines of research. It is in the matter of compression and heat drop that land-operating turbines are less favourable than aircraft types.
In a moving aircraft, a degree of pre-compression is obtained which materially assists in the work of compression. Indeed, at projected speeds in the order of 1,500 m.p.h., sufficient compression from " ram " effect is obtained to dispense with the compressor in its entirety. Similarly, at high altitudes, the low atmospheric pressure increases the pressure difference between that of compression and exhaust. Atmospheric temperatures are also lower, and compression is more efficient, whilst, as with the pressure, the combustion temperature and that of the exhaust show an increased difference with greater altitude. The exhaust gases, having lost their pressure in driving the turbine, are still at a high temperature and, therefore, represent a wastage of heat. To improve efficiency they are passed to a heat exchanger, which consists of a nest of tubes in a suitable casing over which the exhaust gases are passed before being released to the atmosphere.
Air from the compressor traverses the interior of the interchanger tubes, where its temperature is raised by the hot exhaust gases on the exterior. The heat thus added may be deducted from that which is supplied in the form of fuel to reach maximum combustion temperature with consequent improvement in the thermal efficiency.
Obviously, the maximum temperature rise obtainable by this means is the mean difference between the exhaust and compressed-air temperatures, although such a high saving can be achieved only theoretically. In practice, the space limitations reduce the extent of heat extraction. apart from other incidental losses, such as those from imperfect conductivity, radiation to atmosphere, and so forth.
How Pressure is Obtained
Some doubt is often expressed as to ho* the pressure is obtained in a turbine when air is fed into a combustion chamber which is, apparently, open at both ends The compressor should be considered as delivering air to a closed chamber. Then it will be easier to appreciate the similarity between an orthodox cylinder and piston. Air will be delivered into the chamber with everincreasing pressure, until it becomes of such magnitude that it equals the maximum which can be produced by the pump, when further delivery of air will cease although pressure will be maintained.
The incorporation of a small aperture will, of course, permit loss of air, but the quantity is limited by the pressure in the chamber forcing it out. The size of the aperture may thus be chosen so that air loss does not exceed that capable of being delivered by the compressor, when pressure may be maintained.
In an actual turbine, the aperture may be in the form of one or more nozzles, shaped to give streamline flow, or this may be a ring of fixed blades. Both systems serve the same function of holding the required pressure, and directing the air, or gas flow, in the required direction for driving the turbine.