Check electrics on new lorries
Page 56
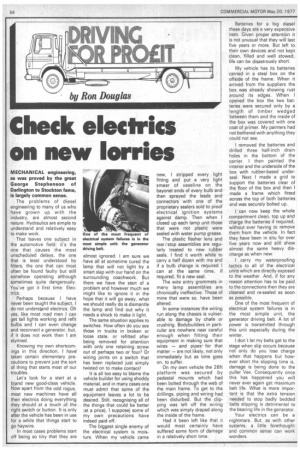
If you've noticed an error in this article please click here to report it so we can fix it.
MECHANICAL engineering, as was proved by the great George Stephenson of Darlington to Stockton fame, is largely common sense.
The problems of diesel engineering to many of us who have grown up with the industry, are almost second nature. Hydraulics are simple to understand and relatively easy, to make work.
That • leaves one subject in the automotive field; its the one that causes the most unscheduled delays, the one that is least understood by fitters, the one that can most often be found faulty but still somehow operating although sometimes quite dangerously. You've got it first time: Electrics.
Perhaps because I have never been taught the subject, I do not understand electrics. Oh yes, like most road men I can get tail lights working and refit bulbs. and I can even change and reconnect a generator, but, if it does not work then I am stymied.
Knowing my own shortcomings in this direction, I have taken certain elementary precautions to prevent just the sort of thing that starts most of our troubles.
Let's look for a start at a brand new good-class vehicle. Now apart from the odd rogue, most new machines have all their electrics doing everything they should at a touch of the right switch or button. It is only after the vehicle has been in use for a while that things start to go haywire.
In most cases problems start off being so tiny that they are almost ignored. I am sure we • have all at sometime cured the lamp that will not light by a smart slap with our hand on the surrounding coachwork. But there we have the start of a problem and however much we might like to ignore it in the hope that it will go away, what we should really do is dismantle the lamp and find out why it needs a shock to make it light.
The same situation applies to switches. How often do you see those in trucks in broken or loose state, or refitted after being removed for attention with only one retaining screw out of perhaps two or four? Or wiring joints on a switch that has been replaced just simply twisted on to make contact?
It is all too easy to blame the vehicle builder for using shoddy material, and in many cases one must admit that some of the equipment leaves a lot to be desired. Still, recognising all of the things that could be better at a price), I suppose) some of my own precautions have indeed paid off.
The biggest single enemy of the electrical system is moisture. When my vehicle came new, I stripped every light fitting and put a very light smear of vaseline on the bayonet ends of every bulb and then sprayed the leads and connectors with one of the proprietary sealers sold to proof electrical ignition . systems against damp. Then when I closed up each lamp unit those that were not plastic were sealed with water pump grease.
The plastic flasher lens and rear/stop assemblies are regularly treated to new rubber seals. I find it worth while to carry a half dozen with me and if a bulb change is required I can at the same time, if required, fit a new seal.
The wire entry grommets in many lamp assemblies are chronically ineffective. Those of mine that were so, have been altered.
In some instances the wiring run along the chassis is vulnerable to damage by chafe or crushing. Bodybuilders in particular are nowhere near careful enough when fitting their equipment in making sure that wires — and pipes for that matter -are not likely, not only immediately but as time goes on, to suffer.
On my own vehicle the 26ft platform was secured by pedestal mounts which had been bolted through the web of the main frame. To get to the drillings, piping and wiring had been disturbed. But the clipping was left off the wiring which was simply draped along the inside of the frame.
Had it been left like that it would most certainly have suffered some form of damage in a relatively short time. Batteries for a big diesel these days are a very expensive item. Given proper attention it is not unusual that they will last five years or more. But left to their own devices and not kept clean, filled and well stowed, life can be disastrously short.
My vehicle has its batteries carried in a steel box on the offside of the frame. When it arrived from the suppliers the box was already showing rust around its edges. When I opened the box the two batteries were secured only by a length of timber wedged between them and the inside of the box was covered with one coat of primer. My painters had not bothered with anything they could not see.
I removed the batteries and drilled three half-inch drain holes in the bottom of the carrier. I then painted the interior and the underside of the box with rubber-based underseal. Next I made a grid to support the batteries clear of the floor of the box and then •1 made a frame which fitted across the top of both batteries and was securely bolted up.
I can now keep the whole compartment clean, top up and charge the batteries if required, without ever having to remove them from the vehicle. In fact they have been in situ for over five years now and still show almost the same heavy discharge as when new.
I carry my waterproofing tactics to all of the electrical units which are directly exposed to the weather. And, if for any reason attention has to be paid. to the connections then they are cleaned and re-sealed as soon as possible.
One of the most frequent of electrical system failures is in the most simple unit, the generator driving belt. A lot of power is transmitted through this unit especially during the winter.
I don't let my belts get to the stage when slip occurs because not only do you lose charge when that happens but however short the slipping time is, damage is being done to the puller Vee. Consequently once this has happened you will never ever again get maximum belt life. What is more important is that the extra tension needed to stop badly bedded belts slipping is detrimental to the bearing life in the generator.
Your electrics can be a nightmare. But, as with other systems, a little forethought and common sense can work wonders.