AN ALL-B ENGINE I ZITISH OIL SERVICE
Page 54
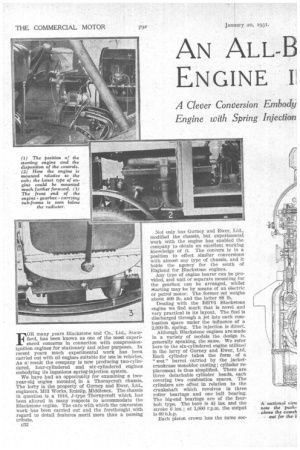
Page 55
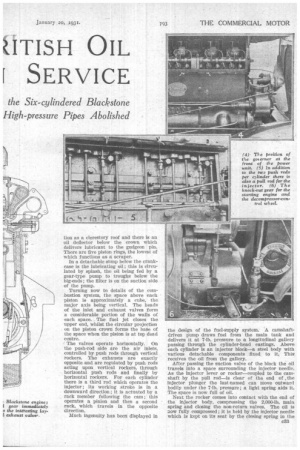
Page 56
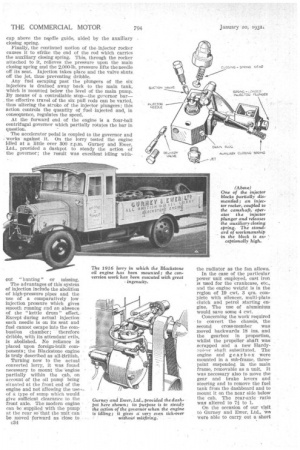
Page 57
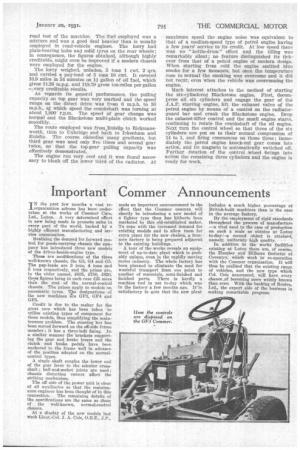
If you've noticed an error in this article please click here to report it so we can fix it.
FOR many years Blackstone and Co., Ltd., Stemford, has been known as one of the most experienced concerns in connection with compressionignition engines for stationary and other purposes. In recent years much experimental work has been carried out with oil engines suitable for use in vehicles. As a, result the company is now producing two-cylindered, four-cylindered and six-cylindered engines embodying its Ingenious spring-injection system.
We have had an opportunity for examining a twoYear-old engine mounted. in a Thornycroft chassis. The lorry is the property of Gurney and Ewer, Ltd., engineers, Mill Works, Ruislip, Middlesex. The chassis in question is a 1916, J-type Thornycroft which has been altered in many respects to accommodate the Blackstone engine. The care with which the 2onversion work has been carried out and the forethought, with regard to detail features merit more than a passing tribute.
c32 Not only has Gurney and Ewer, Ltd., modified the chassis, but experimental work with the engine has enabled the company to obtain an excellent working knowledge of it. The concern is in a position to effect similar conversions with almost any type of chassis, and it holds the agency for the south of England for Blackstone engines.
Any type of engine bearer can be provided, and unit or separate mounting for the gearbox can be arranged, whilst r.atarting may be by means of an electric or petrol motor. The former set weighs about 409 lb. and the latter 88 lb.
Dealing with the BHV6 Blackstone engine we find much that is novel and very practical in its layout. The fuel is discharged through a jet into each combustion space under the influence of a 2,000-lb. spring. The injection is direct.
Although Blackstone engines are made in a variety of models the design is, generally speaking, the same. We refer here to the six-cylindered engine utilized in the lorry of Gurney and Ewer, Ltd. Each cylinder takes the form of a " wet " barrel carried by the jacketcrankcase monobloc casting; cylinder replacement is thus simplified. There are three detachable cylinder heads, each covering two combustion spaces. The cylinders are offset in relation to the crankshaft which revolves in three roller bearings and one ball bearing. The big-end bearings are of the fourbolt type. The bore is 4 ins, and the stroke 6 ins.; at 1,000 r.p.m. the output Is 60 b.h.p.
Each piston crown has the same sec ton as a clerestory roof and there is an oil deflector below the crown which delivers lubricant to the gudgeon pin. There are five piston rings, the lowest of which functions as a scraper.
In a detachable sump below the crankcase is the lubricating oil; this is circulated by splash, the oil being fed by a gear-type pump to troughs below the big-ends; the filter is on the suction side of the pump.
Turning now to details of the combustion system, the space above each piston is approximately a cube, the major axis being vertical. The heads of the inlet and exhaust valves form a considerable portion of the walls of each space. The fuel jet closes the upper end, whilst the circular projection on the piston crown forms the base of the space when the piston is at top dead centre.
The valves operate horizontally. On the push-rod side are the air inlets, controlled by push rods through vertical rockers. The exhausts are exactly opposite and are regulated by push rods acting upon vertical rockers, through horizontal push rods and finally by horizontal rockers. For each cylinder there is a third rod which operates the injector ; its working stroke is in a downward direction ; it is actuated by a rack member following the earn; this operates a pinion and then a second rack, which travels in the opposite direction.
Much ingenuity has been displayed in the design of the fuel-supply system: A camshaftdriven pump draws fuel from the main tank and delivers it at 7-lb. pressure to a longitudinal gallery passing through the cylinder-head castings. Above each cylinder is an injector block—a steel body with various detachable components fixed to it. This receives the oil from the gallery.
After passing the suction valve of the block the oil travels into a space surrounding the injector needle. As the Injector lever or rocker—coupled to the camshaft by the pull rod—is clear of the end of • the injector plunger the last-named can Move outward bodily under the 7-lb. pressure; a light spring aids it. The space is now full of oil.
Next the rocker comes into contact with the end of the injector body, compressing the 2,000-lh. main spring and closing the non-return valves. The oil is now fully compressed; it is held by the injector needle which is kept on 'its seat by the closing spring in the
cap above the nckedle guide, aided by the auxiliary closing spring.
Finally, the continued motion of the injector rocker causes it to strike the end of the rod which carries the auxiliary closing spring. This, through the rocker attached to it, relieves the pressure upon the main closing spring and the 2,000-lb. pressure lifts the needle off its seat. Injection takes place and the valve shuts off the jet, thus, preventing dribble.
• Any fuel escaping past the plungers of the six injectors is drained away hack to tile main tank, which is mounted below the level of the main pump. By means of a controllable stop—the governor bar_ the effective travel of the six pull rods can be varied, thus altering the stroke of the injector plungers; this action controls the quantity of fuel injected and, in consequence, regulates the speed.
At the forward end, of the engine is a four-ball centrifugal governor which partially rotates the bar in question.
The accelerator pedal is coupled to the governor and works against it. On the lorry tested the engine Idled at a little over 300 r.p.m. Gurney and Ewer, Ltd., provided a dashpot to steady the action of the governor; the result was excellent idling with out "hunting" or missing.
The advantages of this system of injection include the abolition of high-pressure pipes and the use of a comparatively low injection pressure which gives smooth running and an absence of the "kettle drum" effect. Except during actual injection each needle is on its seat and fuel cannot escape into the combustion chamber ; therefore dribble, with its attendant evils, is abolished. No reliance is placed upon foreign-built components; the Blackstone engine is truly described as all-British.
Turning now to the actual converted lorry, it was found necessary to mount the engine partially within the cab, on account of the oil pumri being situated at the front end of the engine and not allowing the use of a type of sump which would give sufficient clearanee to the front axle. The modern engine can be supplied with the pump at the rear so that the unit Can be moved fortvard as .clOse to
c34 the radiator as the fan allows.
In the case of the particular power unit employed, cast iron is used for the 'crankcase, etc., and the engine weight is in the region of 19 cwt. 3 qrs. complete with silencer, multi-plate clutch and petrol starting engine. The use of aluminium would save some 4 cwt.
Concerning the work required to convert the chassis, the second cross-member was moved backwards 18 ins. and the gearbox in proportion, whilst the propeller shaft was scrapped and a new HardyNni,,er shaft substituted. The engine and gearbox were mounted in a sub-frame, threepoint suspended in the main frame, removable as a unit. It was necessary also to move the gear and brake levers and steering and to remove the fuel tank from the dashboard and to mount it on the near side below the • cab. The rear-axle ratio was altered to 7/ to 1.
On the occasion of our visit to Gurney and Ewer. Ltd., we were able to carry out a short
road test of the macuine. The fuel employed was a mixture and was a good deal heavier than is usually employed in road-vehicle engines. The lorry had plain-bearing hubs and solid tyres on the rear wheels ; in consequence, the figures obtained, although highly creditable, might even be improved if a modern chassis were employed for the engine.
The lorry weighed, unladen, 5 tons 1 cwt. 2 qrs. and carried a pay-load of 5 tons 10 cwt. It covered 16.9 miles in 54 minutes on I-4 gallon of oil fuel, which gives 11.26 m.p.g. and 118.79 gross ton-miles per gallon —very creditable results.
As regards its general performance, the pulling capacity on top gear was very marked and the speed range on the direct drive was from 6 m.p.h. to 30 m.p.h., at which speed the crankshaft was turning at about 1,800 r.p.m. The speed of gear change was normal and the Blackstone multi-plate clutch worked smoothly.
The route employed was from Ruislip to Rickmansworth, then to Uxbridge and back to Ickenham and Ruislip. The course efabodies many gradients, but third gear was used only five times and second gear twice, so that the top-gear pulling capacity was effectively demonstrated.
The engine ran very cool and it was found necessary to blank off the lower third of the radiator. At maximum speed the engine noise was equivalent to that of a medium-speed type of petrol engine having a few years' service to its credit. At low speed there was no "kettle-drum" effect and the idling was remarkably silent; no feature distinguished its tickover from that of a petrol engine of modern design. When starting from cold the engine emitted blue smoke for a few Moments, but once the temperature rose to normal the smoking was overcome and it did not recur, even when the vehicle was overrunning the engine.
Much interest attaches to the method of starting the six-cylindered Blackstone engine. First, decompress all six cylinders and engage the gear of the J.A.P. starting engine, lift the exhaust valve of the petrol engine by means of a control on the radiatorguard bar and crank the Blackstone engine. Drop the exhaust-lifter control and the small engine starts, continuing to rotate the crankshaft of the oil engine. Next turn the control wheel so that three of the six cylinders -are put on to their normal compression of 14 to 1, and firing commences on those three; immediately the petrol engine knock-out gear comes into action, and its magneto is automatically switched off. Further rotation of the control wheel trings into action the remaining three cylinders and the engine is ready for work.