Machine-shop Equipment.
Page 3
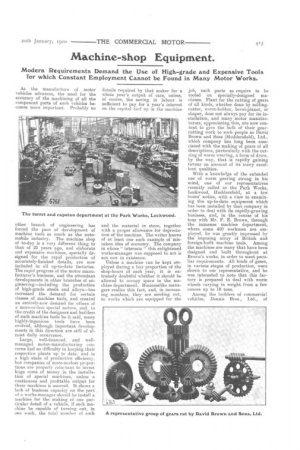
Page 4
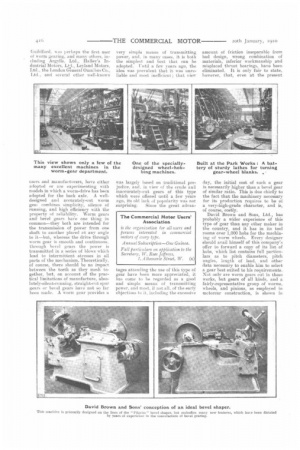
Page 5
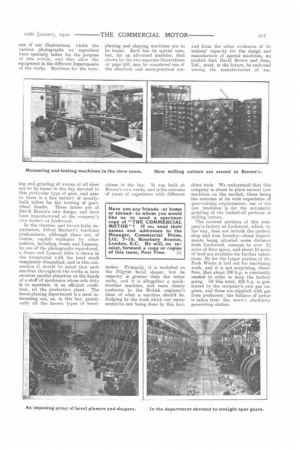
If you've noticed an error in this article please click here to report it so we can fix it.
Modern Requirements Demand the Use of High-grade and Expensive Tools for which Constant Employment Cannot be Found in Many Motor Works.
As the manufacture of motor vehicles advances, the need for the accuracy of the machining of all the component parts of such vehicles becomes more important. Probably no other branch of engineering has forced the pace of development of machine tools so much as the auto-. mobile industry. The machine shop of to-day is a very different thing to that of 25 years ago, and elaborate and expensive machines, specially designed for the rapid production of accurately-finished details, are now included in all up-to-date factories. The rapid progress of the motor manufacturer's business, and the attendant developments in other branches of engineering—including the production of high-grade steels and alloys—has increased the demand for certain classes of machine tools, and created an entirely-new demand for others of a more-or-less special nature. and, to the credit of the designers and builders of such machine tools be it said, many highly-ingenious tools have been evolved, although important developments in this direction are still of almost daily occurrence. Large, well-financed, and wellmanaged motor-manufacturing concerns find no difficulty in keeping their respective plants up to date, and in a high state of productive efficiency, but companies of more-modest proportions are properly reluctant to invest huge sums of money in the installation of special machines, unless a continuous and profitable output for these machines is assured. Tt shows a lack of business capacity on the part of a works-manager should he install a. machine for the making of one particular detail of a vehicle, if such machine be capable of turning out, in one week, the total number of such
details required by that maker for a whole year's output of cars, unless, of course, the saving in labour is sufficient to pay for a year's interest on tbe capital tied up in the machine and the material in store, together with a proper allowance for depreciation of the machine. The writer knows of at least one such example of mistaken idea of economy. The company in whose " interests" this enlightened works-manager was supposed to act is not now in existence.
Unless a machine can be kept employed during a fair proportion of the shop-hours of each year, it is extremely doubtful whether it should be allowed to occupy space in the machine department. Businesslike managers realize this fact, and, in increasing numbers, they are sending out, to works which are equipped for the job, such parts as require to be tooled on specially-designed machines. Plant for the cutting of gears of all kinds, whether done by millingcutter, worm-hobber, bevel-planer, or shaper, does not always pay for its installation, and many motor manufacturers, appreciating this, are now content to give the bulk of their gearcutting work to such people as David Brown and Sons (Huddersfield), Ltd., which company has long been associated with the making of gears of all descriptions, particularly with the cutting of worm wearing, a. form of drive, by the way, that is rapidly gaining favour on account of its many excellent qualities.
With a knowledge of the extended use of worm gearing strong in his mind, one of our representatives recently called at the Park Works, Lockwood, Huddersfield, at a few hours' notice, with a view to examining the up-to-date equipment which has been installed by that company in order to deal with its rapidly-growing business, and, in the course of his tour with Mr. F. E. Brown, through the immense machine department, where some 400 workmen are employed, he was greatly impressed by the imposing array of British and foreign-built machine tools. Among the machines are many that have been designed and built throughout at Brown's works, in order to meet peculiar requirements. All kinds of gears, in various stages of production, were shown to our representative, and he was interested to note that this factory is prepared to deal with worm wheels varying in weight from a few ounces up to 18 tons.
Among the builders of commercial vehicles, Dennis Bros., Ltd., of
Guildford. was perhaps the first user of worm gearing, and many others, including Argylls, Ltd., 'Talley's Industrial Motors, 1.141., Leyland Motors, Ltd., the London General Omnibus Co., Ltd., and several other well-known users and manufacturers, have either adopted or are experimenting with models in which a worm-drive has been adopted for the back axle. A welldesigned and accurately-cut worm gear combines simplicity, silence of running, and high efficiency with the property it reliability. Worm gears and bevel gears have one thing in common—they both are intended for the transmission of power from one shaft to another placed at any angle to ii—but, whereas the drive through worm gear is smooth and continuous, through bevel gears the power is transmitted in a series of blows which lead to intermittent StreSSOS in all parts of the mechanism. Theoretically, of course, there should be no impact between the teeth as they mesh together, but, on account of the practical limitations of manufacture, absolutely-silent-running, straight-cut spur gears or bevel gears have not so far been made. A worm gear provides a
very,simple means of transmitting power, and, in ninny cases, it is bath the simplest. and best that can be adopted. Until a few years ago, the idea was prevalent that it was unreliable and most inefficient; that view was largely based on traditional prejudice, and, in view of the crude and inaccurately-cut gears of this type which were offered until a few years ago, its old lack of popularity was not surprising. Since the great advan
tages attending the use of this type of gear have keen more appreciated, it has come to be regarded as a good and simple means of transmitting power, and most. if not n11. of the early objections to it, irwliidinic the excessive
amount. of friction inseparable from bad design, wrong combination of materials, inferior workmanship and misplaced thrust bearings, have been eliminated. It is only fair to state, however, that, even at the present day, the initial cost of such a gear is necessarily higher than a bevel gear of similar ratio. This is due chiefly to the fact that the machinery necessary for its production requires to be of a very-high-grade character, and is, of course, costly.
David Brown and Sons, Ltd., has probably a wider experience of this type of gear than any other maker in the country, and it has in its tool rooms over 1,000 hobs for the machining of worm wheels. Every designer should avail himself of this company's offer to forward a copy of its list of hobs, which list contains full particulars as to pitch diameters, pitch angles, length of lead, and other data necessary to enable him to select a gear best suited to his requirements. Not only are worm gears cut in these works, but gears of all kinds, and a fairly-representative group of worms, wheels, and pinions, as employed in motorcar construction, is shown in
one of our illustrations, whilst the various photographs we reproduce were specially taken for the purpose of this article, and they 6how the equipment in the different departments of the works. Machines for the turn ing and grinding of worms of all Sizes are to be found in the bay devoted to this particular type of gear, and near to these is a fine battery of stoutlybuilt lathes for the turning of gearwheel blanks. These lathes are of David Brown's own design, and have been manufactured at the company's own factory at Lockwood.
In the capstanand turret-lathe department, Alfred Herbert's machines predominate, although there are, of course, capital examples by other makers, including Jones and Lamson. In one of the photographs reproduced, a Jones and Lamson lathe is shown in the foreground with the head stock completely dissembled, and in this connection it should he noted that each machine throughout the works in turn receives careful attention at the hands of a staff of mechanics whose sole duty is to maintain, in an efficient condition, all the productive plant. The bevel-planing department is a most interesting one, as, in this bay, practically all the known types of bevel planing and shaping machines are to be found. Each has its special uses, but, for an all-round machine, that shown by the two separate illustrations or. page 416, may be considered one of the sturdiest and most-practical ma
chines in the bay. It was built at Brown's own works, and is the outcome of years of experience with different makes. Primarily, it is modelled on the Pilgrim bevel shaper, but its capacity is greater than the latter make, and it is altogether a muchsturdier machine, and more closely conforms to the British engineer's ideas of what a machine should be. Judging by the work which our representative saw being done by this tool, and from the other evidences of its makers' capacity for the design and manufacture of special machines, we predict that David Brown and Sons, Ltd., must, in the future, be reckoned among the manufacturers of ma chine tools. We understand that this company is about to place several new machines on the market, these being the outcome of its wide experience of gear-cutting requirements, one of the new machines is for the automatic grinding of the backed-off portions of milling cutters.
The covered portions of this company's factory at Lockwood, which, by the way, does not include the pattern shop and iron foundry—those departments being situated some distance from Lockwood, amount to over 22,acres of floor space, and about 10 acres of land are available for further extensions. By far the larger portion of the Park Works is laid out for machining work, and it is not surprising, therefore, that about 500 h.p. is constantly needed in order to keep the factory going. Of this total, 350 h.p. is generated by the company's own gas engines, and these are supplied with gas from producers; the balance of power is taken from the town's electricity generating station.