From Bonallack . . max-section
Page 57
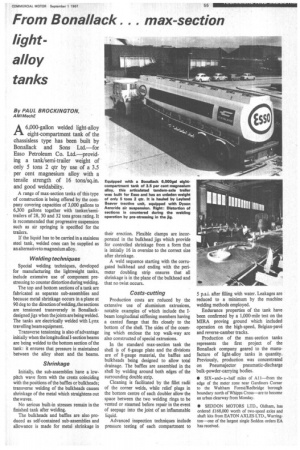
If you've noticed an error in this article please click here to report it so we can fix it.
light
alloy tanks
By PAUL BROCKINGTON,
AMIMechE
A6,000-gallon welded light-alloy eight-compartment tank of the chassisless type has been built by Bonallack and Sons Ltd.—for Esso Petroleum Co. Ltd.—providing a tank/semi-trailer weight of only 5 tons 2 qtr by use of a 3.5 per cent magnesium alloy with a tensile strength of 16 tonsisq.in. and good weldability.
A range of max-section tanks of this type of construction is being offered by the company covering capacities of 3,000 gallons to 6,300 gallons together with tanker/semitrailers of 28, 30 and 32 tons gross rating. It is recommended that progressive suspension such as air springing is specified for the trailers.
If the liquid has to be carried in a stainless steel tank, welded ones can be supplied as an alternativeto magnesium alloy.
Welding techniques Special welding techniques, developed for manufacturing the lightweight tanks, include extensive use of component prestressing to counter distortion during welding.
The top and bottom sections of a tank are fabricated as separate sub-assemblies and because metal shrinkage occurs in a plane at 90 deg to the direction ofwelding,the sections are tensioned transversely in Bonallackdesigned jigs when the joints are being welded. The tanks are electrically welded with Lynx travelling beam equipment.
Transverse tensioning is also of advantage initially when the longitudinal I-section beams are being welded to the bottom section of the tank: it ensures that pressure is maintained between the alloy sheet and the beams.
Shrinkage Initially, the sub-assemblies have a lowpitch wave form with the crests coinciding with the positions of the baffles or bulkheads; transverse welding of the bulkheads causes shrinkage of the metal which straightens out the waves.
No serious built-in stresses remain in the finished tank after welding.
The bulkheads and baffles are also produced as self-contained sub-assemblies and allowance is made for metal shrinkage in
their erection. Flexible clamps are incorporated in the bulkhead jigs which provide for controlled shrinkage from a form that is initially 16 in oversize to the correct size after shrinkage.
A weld sequence starting with the corrugated bulkhead and ending with the perimeter doubting strip ensures that all shrinkage is in the plane of the bulkhead and that no twist occurs.
Costs-cutting Production costs are reduced by the extensive use of aluminium extrusions, notable examples of which include the Ibeam longitudinal stiffening members having a canted flange that fits closely to the bottom of the shell. The sides of the coaming which enclose the top walk-way are also constructed of special extrusions.
In the standard max-section tank the shell is of 6-gauge plate and the divisions are of 8-gauge material, the baffles and bulkheads being designed to allow total drainage. The baffles are assembled in the shell by welding around both edges of the surrounding double strip.
Cleaning is facilitated by the fillet radii of the corner welds, while relief plugs in the bottom centre of each doubler allow the space between the two welding rings to be vented or steamed before repair in the event of seepage into the joint of an inflammable liquid.
Advanced inspection techniques include pressure testing of each compartment to 5 p.s.i. after filling with water. Leakages are reduced to a minimum by the machine welding methods employed.
Endurance properties of the tank have been confirmed by a 1,000-mile test on the MIRA proving ground which included operation on the high-speed, Belgian-pave and reverse-camber tracks.
Production of the max-section tanks represents the first project of the Bonallack company geared to the manufacture of light-alloy tanks in quantity. Previously, production was concentrated on Pneumajector pneumatic-discharge bulk-powder-carrying bodies.
• SIXanda -half miles of All—from the edge of the meter zone near Gardiners Corner to the Waltham Forest/Redbridge borough boundary north of Whipps Cross—are to become an urban clearway from Monday.
• SEDDON MOTORS LTD., Oldham, has ordered £168,000 worth of two-speed axles and shaft kits from EATON AXLES LTD., Warrington—one of the largest single Seddon orders EA has received,