Leyland Opens New Injector Factory E QUIPPED with the most modern
Page 38
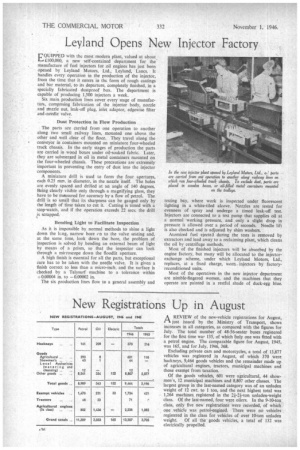
If you've noticed an error in this article please click here to report it so we can fix it.
plant, valued at about £100,000, a new self-contained department for the manufacture of fuel injectors for .oil engines has just been opened by Leyland Motors, Ltd., Leyland, Lancs. It handles every operation in the production of the injector, from the time that it enters in the. form of rough castings and bar material, to its departure, completely finished, in a specially fabricated dustproof box. The department is capable of producing 1,500 injectors a week.
Six main production lines cover every stage of manufacture, comprising fabrication of the injector body, nozzle and trozzle nut, leak-off plug, inlet adaptor, edgewise filter and-needle valve.
Dust Protection in Flow Production The parts are carried from one operation to another along two small railway lines, mounted one above the other and well clear of the floor. They travel along the conveyor in containers mounted on miniature four-wheeled truck chassis. In the early stages of production the parts are carried in wood boxes under oil-soaked fabric. Later, they are submerged in oil in metal containers mounted on the four-wheeled chassis. These precautions are extremely important in preventing the entry of dust into the injector components.
A miniature drill is used to form the four apertures, each 0.25 mm. in diameter, in the nozzle itself. The holes are evenly spaced and drilled at an angle of 140 degrees. Being clearly visible only through a magnifying glass, they have to be measured for accuracy by a flow of petrol. The drill is so small that its sharpness can be gauged only by the length of time taken to cut it. Cutting is timed with a stop-watch, and if the operation exceeds 22 secs. the drill is scrapped.
Bending Light to Facilitate Inspection As it is impossible by normal methods to shine a light down the long, narrow bore on to the valve seating and, at the same time, look down the bore, the problem of inspection is solved by.bending an external beam of light by means of a prism, so that the inspector can look through a microscope down the floodlit aperture.
A high finish is essential for all the parts, but exceptional care has to be taken with the needle valve. It is given a finish correct to less than a micro-inch, and the surface is checked by a Talysurf machine to a tolerance within +0.00004 in. to —0.00002 in.
The six production lines flow to a general assembly and
testing bay, where work is inspected under fluorescent lighting in a white-tiled alcove. Nozzles are tested for evenness of spray and undergo a timed leak-off test. Injectors are connected to a test pump that supplies oil at a normal working pressure, and only a slight drop in pressure is allowed over a period of seconds. Needle lift is also checked and is adjusted by shim washers.
Atomized fuel ejected during the tests is removed by extractors and lead away to a reclaiming plant, which cleans the oil by centrifuge methods.
Most of the finished injectors will be absorbed by the engine factory, but many will be allocated to the injectorexchange scheme, under which Leyland Motors, Ltd., replaces, at a fixed charge, worn injectors by factoryreconditioned units.
Most of the operatives in the new injector department are nimble-fingered women, and the machines that they operate are painted in a restful shade of duck-egg blue.