Mobile space heaters
Page 93
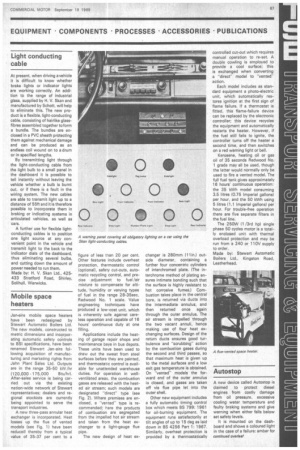
If you've noticed an error in this article please click here to report it so we can fix it.
Jan-aire mobile space heaters have been redesigned by Stewart Automatic Boilers Ltd. The new models, constructed to metric dimensions and incorporating automatic safety controls to BSI specifications, have been renamed Stewart Jan-aire following acquisition of manufacturing and marketing rights from Jahn Plant Sales Ltd. Outputs are in the range 35-50 kW /hr 1120,000 175,000 Btu/hr). After-sales service is being carried out via the existing nation-wide network of Stewart representatives; dealers and regional stockists are currently being appointed to serve the transport industries.
A new three-pass annular heat exchanger is incorporated. Heat losses up the flue of vented models (see Fig. 1) have been reduced thereby from a typical value of 35-37 per cent to a figure of less tian 20 per cent. Other features include overheat protection, thermostatic control (optional), safety cut-outs, automatic recycling control, and pre cise adjustment to fuel /air mixture to compensate for altitude, humidity or varying types of fuel in the range 28-35sec, Redwood No. 1 scale. Value engineering techniques have produced a low-cost unit, which is inherently sate against careless operation and capable of 16 hours' continuous duty at one filling.
Applications include the heating of garage repair shops and maintenance bays in bus depots. These units have been used to draw out the sweat from steel surfaces before they are painted, and thermostatic control is available for unattended warehouse duties. For operation in wellventilated areas, the combustion gases are released with the heated air stream; such models are designated "direct" type (see Fig. 21. Where premises are enclosed, a "vented" type is recommended; here the products of combustion are segregated from the impelled hot air stream and taken from the heat exchanger to a light-gauge flue pipe.
The new design of heat ex
changer is 280mm 111 in.) outside diameter, containing a further four concentric cylinders of interchromed plate. (The interchrome method of plating ensures intimate bonding such that the surface is highly resistant to hot corrosive fumes.) Combustion takes place in the central bore, is returned via ducts into the intermediate annulus, and then returned once again through the outer annulus. The air stream is impelled through the two vacant annuli, hence making use of four heat exchanging surfaces. Design of the return ducts ensures good turbulence and "scrubbing" action by the combustion gases during the second and third passes, so that maximum heat is given up to the metal surfaces and a low exit gas temperature is obtained. On "vented" models the forward end of the outer annulus is closed, and gases are taken off via flue pipe let into the outer shell.
Other new equipment includes a fully automatic timing control box which meets BS 799: 1961 for oil-burning equipment. The equipment runs satisfactorily at tilt angles of up to 15 deg as laid down in BS 4256 Part 1:1967. Similarly, overheat protection is provided by a thermostatically
controlled cut-out which requires manual operation to re-set. A double cowling is employed to provide a cool surface; this is exchanged when converting a -direct" model to "vented" action.
Each model includes as standard equipment a photo-electric unit, which automatically restores ignition at the first sign of flame failure. If a thermostat is fitted, this flame-failure device can be replaced by the electronic controller; this device recycles the equipment and automatically restarts the heater. However, if the fuel still fails to ignite, the controller turns off the heater a second time, and then switches on a red warning light or bell.
Kerosene, heating oil or gas oil of 35 seconds Redwood No. 1 grade may all be used, though the latter would normally only be used to fire a vented model. The full fuel tank gives approximately 16 hours' continuous operation: the 35 kWh model consuming 3.5 litres (0.75 Imperial gallons) per hour, and the 50 kWh using 5 litres (1.1 Imperial gallons) per hour. For trouble-free operation there are five separate filters in the fuel line.
The 250W (1 /3rd hp) single phase 60 cycles motor is a totally enclosed unit with thermal overload protection and may be run from a 240 or 110V supply to order, Made by: Stewart Automatic Boilers Ltd., Kingston Road, Leatherhead.