Productivity in freight transport the SPD scheme
Page 76
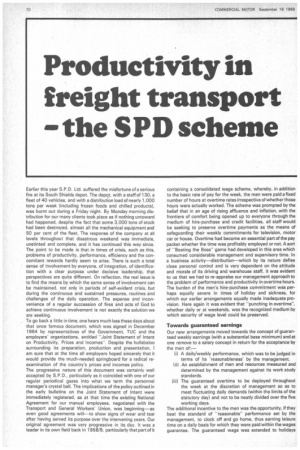
Page 77
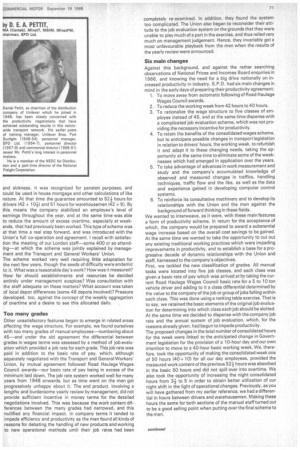
Page 78
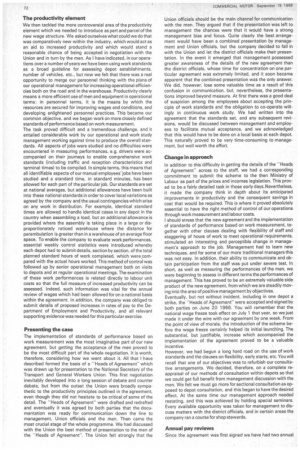
Page 79

If you've noticed an error in this article please click here to report it so we can fix it.
Earlier this year S.P.D. Ltd. suffered the misfortune of a serious fire at its South Shields depot. The depot, with a staff of 130, a fleet of 40 vehicles, and with a distribution load of nearly 1,000 tons per week (including frozen foods and chilled products), was burnt out during a Friday night. By Monday morning distribution for our many clients took place as if nothing untoward had happened, despite the fact that some 3,000 tons of stock had been destroyed, almost all the mechanical equipment and 50 per cent of the fleet. The response of the company at all levels throughout that disastrous weekend was immediate, unstinted and complete, and it has continued this way since. The point to be made is that in times of crisis, such as this, problems of productivity, performance, efficiency and the concomitant rewards hardly seem to arise. There is such a total sense of involvement by everyone, of integration, of identification with a clear purpose under decisive leadership, that perspectives are quite different. On reflection, the real issue is to find the means by which the same sense of involvement can be maintained, not only in periods of self-evident crisis, but during the continuous and sustained pressures, routines and challenges of the daily operation. The expense and inconvenience of a regular succession of fires and acts of God to achieve continuous involvement is not exactly the solution we are seeking.
To go back a little in time, one hears much less these days about that once famous document, which was signed in December 1964 by representatives of the Government, TUC and the employers' organizations, entitled "Joint Statement of Intent on Productivity, Prices and Incomes". Despite the hullabaloo surrounding its preparation, production and presentation, I am sure that at the time all employers hoped sincerely that it would provide the much-needed springboard for a radical reexamination of the country's prices and incomes policy.
The progressive nature of this document was certainly well accepted by S.P.D., particularly as it coincided with one of our regular periodical gazes into what we term the personnel manager's crystal ball. The implications of the policy outlined in the early bulletins on the Joint Statement of Intent were immediately registered, as at that time the existing National Agreement for our manual employees, negotiated with the Transport and General Workers' Union, was beginning—as even good agreements will to show signs of wear and tear after having served its purpose over the intervening years. Our original agreement was very progressive in its day. It was a leader in its own field back in 1958/9, particularly that part of it containing a consolidated wage scheme, whereby, in addition to the basic rate of pay for the week, the men were paid a fixed number of hours at overtime rates irrespective of whether those hours were actually worked. The scheme was prompted by the belief that in an age of rising affluence and inflation, with the frontiers of comfort being opened up to everyone through the medium of hire-purchase and credit facilities, all staff would be seeking to preserve overtime payments as the means of safeguarding their weekly commitments for television, motor car or house. Overtime had become an essential part of the pay packet whether the time was profitably employed or not. A sort of "Beating the Boss" game had developed in this area which consumed considerable management and supervisory time. In a business activity—distribution—which by its nature defies close personal control and is very dependent on the attitude and morale of its driving and warehouse staff, it was evident to us that we had to re-appraise our management approach to the problem of performance and productivity in overtime hours. The burden of the men's hire-purchase commitment was perhaps equally severe in times of holiday and sickness, for which our earlier arrangements equally made inadequate provision. Here again it was evident that "punching in overtime", whether daily or at weekends, was the recognized medium by which security of wage level could be preserved.
Towards guaranteed earnings
Our new arrangements moved towards the concept of guaranteed weekly earnings (with a substantial base minimum) and at one remove to a salary concept in return for the acceptance by the men of:—
Ii) A daily/weekly performance, which was to be judged in terms of its 'reasonableness' by the management.
(ii) An establishment of men and resources measured and determined by the management against its work study standards.
WO The guaranteed overtime to be deployed throughout the week at the discretion of management so as to meet fluctuating daily demands (within the limits of the statutory day) and not to be neatly divided over the five working days, The additional incentive to the men was the opportunity, if they beat the standard of "reasonable" performance set by the management, to clock off and go home, thus earning leisure time on a daily basis for which they were paid within the wages guarantee. The guaranteed wage was extended to holidays and sickness, it was recognized for pension purposes, and could be used in house mortgage and other calculations of like nature. At that time the guarantee amounted to 52+ hours for drivers (42+ 10+) and 51 hours for warehousemeni42 + 9). By this means the company stabilized an employee's level of earnings throughout the year, and at the same time was able to reduce the amount of excess overtime, especially at weekends, that had previously been worked. This type of scheme was at that time a real step forward, and was introduced with the Union's full co-operation and agreement. I recall with satisfaction the meeting of our London staff—some 400 or so attending—at which the scheme was jointly explained by management and the Transport and General Workers' Union.
The scheme worked very well requiring little adaptation for the next few years, though the seeds of difficulty were endemic to it. What was a reasonable day's work? How was it measured? How far should establishments and resources be decided entirely under management auspices? Was consultation with the staff adequate on these matters? What account was taken of local depot differences (some 48 depots involved)? Pressure developed, too, against the concept of the weekly aggregation of overtime and a desire to see this allocated daily.
Too many grades
Other unsatisfactory features began to emerge in related areas affecting the wage structure. For example, we found ourselves with too many grades of manual employees—numbering about 45—and under the old agreement the differential between grades in wages terms was assessed by a method of job evaluation which provided a job rate for each grade. This job rate was paid in addition to the basic rate of pay, which, although separately negotiated with the Transport and General Workers' Union, by mutual agreement followed Road Haulage Wages Council awards—our basic rate of pay being in excess of the minimum laid down. The job rate system worked well for many years from 1948 onwards, but as time went on the men got progressively unhappy about it. The end product, involving a lengthy and burdensome yearly review by management, did not provide sufficient incentive in money terms for the detailed negotiations involved, This was because the work content differences between the many grades had narrowed, and this nullified any financial impact. In company terms it tended to impede efficiency and productivity as the men found all kinds of reasons for debating the handling of new products and working to new operational methods until their job rates had been completely re-examined. In addition, they found the system too complicated. The Union also began to reconsider their attitude to the job evaluation system on the grounds that they were unable to play much of a part in the exercise, and thus relied very much on management judgement. Hence, they invariably got a most unfavourable playback from the men when the results of the yearly review were announced.
Six main changes
Against this background, and against the rather searching observations of National Prices and Incomes Board enquiries in 1966, and knowing the need for a big drive nationally on increased productivity in industry, S. P. D. had six main changes in mind in the early days of preparing their productivity agreement: 1. To move away from automatic following of Road Haulage Wages Council awards.
2. To reduce the working week from 42 hours to 40 hours.
3. To rationalize the wage structure to five classes of employee instead of 45. and at the same time dispense with a complicated job evaluation scheme, which was not providing the necessary incentive for productivity.
4. To retain the benefits of the consolidated wages scheme, but to anticipate possible changes in transport legislation in relation to drivers' hours, the working week, to refurbish it and adapt it to these changing needs, taking the opportunity at the same time to eliminate some of the weaknesses which had emerged in application over the years.
5. To take advantage of advances in work measurement and study and the company's accumulated knowledge of observed and measured changes in traffics, handling techniques, traffic flow and the like, as well as the data and experience gained in developing computer control systems.
6. To reinforce its consultative machinery and to develop its relationships with the Union and the men against the background of forward thinking in these fields.
We wanted to interweave, as it were, with these main features a form of productivity scheme, in return for the acceptance of which, the company would be prepared to award a substantial wage increase based on the overall cost savings to be gained. At the same time we wanted to take the opportunity to cut out any existing traditional working practices which were impeding improvements in productivity, and to establish a base for a progressive decade of dynamic relationships with the Union and staff, harnessed to the company's objectives.
First, we tackled the new classification of grades. All manual tasks were located into five job classes, and each class was given a basic rate of pay which was arrived at by taking the current Road Haulage Wages Council basic rate for a 5 to 10 ton vehicle driver and adding to it a class differential determined by the value to the company of the job or group of jobs falling within each class. This was done using a ranking table exercise. That is to say, we retained the basic elements of the original job evaluation for determining into which class each job should be slotted. At the same time we decided to dispense with the company job rate and the annual system of job evaluation, which, for the reasons already given, had begun to impede productivity.
The proposed changes in the total number of consolidated hours for the week were linked to the anticipated change in Government legislation for the provision of a 10-hour day and our own intention to move to a 40-hour basic working week. We, therefore, took the opportunity of making the consolidated week one of 50 hours (40+ 10) for all our day employees, provided the measured work content of the previous 52+ hours was absorbed in the basic 50 hours and did not spill over into overtime. We also took the opportunity of increasing the night consolidated hours from 3+ to 5 in order to obtain better utilization of our night shift in the light of operational changes. Previously, as you will have gathered from my earlier reference, we had a differential in hours between drivers and warehousemen. Making these hours the same for both sections of the manual staff turned out to be a good selling point when putting over the final scheme to the men.
The productivity element
We then tackled the more controversial area of the productivity element which we needed to introduce as part and parcel of the new wage structure. We asked ourselves what could we do that was comparatively new within the industry, which would act as an aid to increased productivity and which would stand a reasonable chance of being accepted in negotiation with the Union and in turn by the men. As I nave indicated, in our operations over a number of years we have been using work standards as a broad guideline for assessing depot establishments, number of vehicles, etc., but now we felt that there was a real opportunity to merge our personnel thinking with the plans of our operational management for increasing operational efficiencies both on the road and in the warehouse. Productivity clearly means a more efficient use of men and equipment in operational terms; in personnel terms, it is the means by which the resources are secured for improving wages and conditions, and developing enlightened personnel practices. This became our common objective, and we began work on more closely defined standards of performance based on work measurement.
The task proved difficult and a tremendous challenge, and it entailed considerable work by our operational and work study management working against time to produce the overall standards. All aspects of jobs were studied and no difficulties were encountered in measuring performances, e.g. drivers were accompanied on their journeys to enable comprehensive work standards (including traffic and reception characteristics and terminal times) to be compiled. In simple terms, this means that all identifiable aspects of our manual employees' jobs have been studied and a standard time, in standard minutes, has been allowed for each part of the particular job. Our standards are set at national averages, but additional allowances have been built into these national standards in order to cover local variations as agreed by the company and the usual contingencies which arise on any work in distribution. For example, identical standard times are allowed to handle identical cases in any depot in the country when assembling a load, but an additional allowance is provided where the assembly is taking place in a large or disproportionately ratioed warehouse where the distance for perambulation is greater than in a warehouse of an average floor space. To enable the company to evaluate work performances, essential weekly control statistics were introduced whereby each depot had to submit details, section by section, of the total planned standard hours of work completed, which were compared with the actual hours worked. This method of control was followed up by senior operational management both on visits to depots and at regular operational meetings. The examination of these work performances is related directly to labour unit costs so that the full measure of increased productivity can be assessed. Indeed, such information was vital for the annual review of wages which had been allowed for on a national basis within the agreement. In addition, the company was obliged to submit details of proposed increases in rates of pay to the Department of Employment and Productivity, and all relevant supporting evidence was needed for this particular exercise.
Presenting the case
The implementation of standards of performance based on work measurement was the most imaginative part of our new agreement, but getting the acceptance of the men proved to be the most difficult part of the.whole negotiation. It is worth, therefore, considering how we went about it. All that I have described formed the basis of a "Heads of Agreementwhich was drawn up for presentation to the National Secretary of the Transport and General Workers Union. This first negotiation inevitably developed into a long session of debate and counter debate, but from the outset the Union were broadly sympathetic to the productivity principles outlined in the agreement, even though they did not hesitate to be critical of some of the detail. The "Heads of Agreement" were drafted and redrafted and eventually it was agreed by both parties that the documentation was ready for communication down the line to management, Union officials and the men. Then came the most crucial stage of the whole programme. We had discussed with the Union the best method of presentation to the men of the "Heads of Agreement". The Union felt strongly that the
Union officials should be the main channel for communication with the men. They argued that if the presentation was left to management the chances were that it would have a strong management bias and focus. Quite clearly the best arrangement would have been a combined presentation by management and Union officials, but the company decided to fall in with the Union and let the district officials make their presentation. In the event it emerged that management possessed greater awareness of the details of the new agreement than the district officials, whose time for concentration on one particular agreement was extremely limited, and it soon became apparent that the combined presentation was the only answer. We did, however, lose some valuable time as a result of this confusion in communication, but, nevertheless, the presentations improved beyond measure. At first there was a good deal of suspicion among the employees about accepting the principle of work standards and the obligation to co-operate willingly in continuous work study. We had written into the agreement that the standards set, and any subsequent revisions, would be discussed between management and employees to facilitate mutual acceptance, and we acknowledged that this would have to be done on a local basis at each depot. This naturally proved to be very time-consuming to management, but well worth the effort.
Change in approach
In addition to this difficulty in getting the details of the "Heads of Agreement" across to the staff, we had a corresponding commitment to submit the scheme to the then Ministry of Labour as part of the prices and incomes legislation. This proved to be a fairly detailed task in those early days. Nevertheless, it made the company think in depth about its anticipated improvements in productivity and the consequent savings in cost that would be required. This is where it proved absolutely essential to have the right method of control of our operations through work measurement and labour costs.
I shoutd stress that the new agreement and the implementation of standards of performance based on work measurement, together with other clauses dealing with flexibility of staff and staggering of hours of work to meet operational requirements, stimulated an interesting and perceptible change in management's approach to the job. Management had to learn new techniques, and for some of our more traditional managers this was not easy. In addition, their ability to communicate and obtain participation from the staff was put under severe test. In short, as well as measuring the performances of the men, we were beginning to assess in different terms the performances of management. This has proved to be an extremely valuable side product of the new agreement, from which we are steadily moving into the area of positive management by objectives.
Eventually, but not without incident, including in one depot a strike, the "Heads of Agreement" were accepted and signed by both parties on June 20 1966. You will remember that the national wage freeze took effect on July 1 that year, so we just made it under the wire with our agreement by one week. From the point of view of morale, the introduction of the scheme before the wage freeze certainly helped its initial launching. The substantial, but justifiable, increase which accompanied the implementation of the agreement proved to be a valuable incentive.
However, we had begun a long hard road on the use of work standards and the clauses on flexibility, early starts, etc. You will recall that one of our objectives was to refurbish our consultative arrangements. We decided, therefore, on a complete reappraisal of our methods of consultation within depots so that we could get full benefit from management discussion with the men. We felt we must go more for sectional consultation as opposed to depot consultation, and this began to have the desired effect. At the same time our management approach needed restating, and this was achieved by holding special seminars. Every available opportunity was taken for management to discuss matters with the district officials, and in certain areas the company ran a course for shop stewards.
Annual pay reviews
Since the agreement was first signed we have had two annual reviews of rates of pay. The first review was in September 1967 when the scheme had been running for some 15 months. On this occasion we assessed the improvement in work performances with the help of our monthly performance statistics, and this was linked to labour unit costs over the period in question. We found that the men had responded to the extent that our forecast increase in productivity was in fact achieved, and this was translated into an appropriate wage increase under negotiation with the Transport and General Workers' Union and approved by the Department of Employment and Productivity.
When we came to the review of September 1968, we realized that we could no longer rely solely on assessing a wage increase related to improvements in standards of performance based on work measurement, and related simply to the physical response of men to manual tasks. At the time of the 1967 wage increase the men's performance had reached an acceptable level, and this had been maintained in 1968. However, this was not enough if future productivity improvements were to be progressively achieved. We had to look for some other changes in technologies and working practices that would be beneficial to the company's business and which would equally satisfy the requirements of the prices and incomes policy. We still could look for some degree of improvement in performance from our work measurement planning, but we decided in addition to examine such things as the benefits that could be obtained from 40m.p. h. scheduling and the introduction of vehicles with larger carrying capacities. We also began to consider the implications of a range of technological and other changes related to our Corporate Plan. 40 m.p.h. scheduling did, of course, mean a revamping of certain work standards for drivers, and this had to be included as part of the productivity deal.
Turning point
Looking back, 1968, in terms of our latest productivity arrangements, and to a greater extent 1969, marks a turning point. The years when we could establish a simple relationship between the physical performance of men in warehouse and on the road, on the one hand, and efficiency and productivity with company profitability and increased remuneration to the staff as the consequence on the other, are ending. I am sure that many companies who made an early start in productivity agreements are in the same position. It is true we are still finding opportunities for obtaining results mutually beneficial to management and men in the extension of the simple original formula to include damages, second deliveries, customer queries and the like, as well as in exploring opportunities within the local context of individual depot operations. Much more, however, is required. We still tend to pigeon hole the various group contributions to productivity and the remuneration which stems from them (management, manual, clerical and technical). For instance, it is much too easy to argue that the contribution of our manual staff is related to, indeed is confined to, a physical response to measured standards. This begins to look antediluvian as the industry moves from being labour intensive to being capital intensive, and as the job comes to be seen as a form of personal freehold. Staff attitudes and morale, the capacity of men to exploit the utilization of equipment and capital, their response to new systems and technologies are all vital in this restless search to improve productivity, efficiency, product pricing and ultimately profitability through personal involvement. No management today can categorically state that because it provides the capital it is solely entitled to the rewards which flow from its use. The staff, wherever they may be found, whose co-operation is required to utilize it, as well as the public who ultimately pay the price of a product or service, have a share to be recognized.
What is productivity?
Productivity is not synonymous with profitability, but it is a most significant contributor to it. It is possible for productivity to improve over a period during which profits decline; e.g. increased competition, threat of lost clients, taxation, etc., are all examples of external pressure on the business which tend to depress prices and erode profit margins. Under these circumstances, if productivity improves, it serves to reduce the rate of decline in profit. Conversely, productivity can decline or remain static during a period of profitability. A buoyant market, the ability to exploit a monopolistic situation, an improvement in a client's commercial ability to pay a higher price etc., are examples of influences which enhance profitability and which are not directly related to productivity.
In practice, S. P. D.'s situation is rarely as simple as the examples above might suggest, and it is the very existence of a complex mix of complementary and contradictory trends which leads to a confused understanding of the term "productivity". It is important, therefore, to establish that profit cannot be used as an effective indicator of productivity trend, although clearly, when consideration is given to rewarding employees for their contributions to improving productivity, overall profitability is a vital factor which determines the company's ability to pay.
Broadly, productivity can be defined as the level of output achieved from all resources employed. The term "resources" is used in its widest sense to comprehend depot facilities, building, equipment, vehicles, manpower, etc., etc. If this definition is acceptable, then it follows that the measurement of productivity must be related to the total cost per "unit" of output. The use of a total cost index comprehends the effects of all contributory elements, e.g.: Management/staff effort.
Work flow.
Work organization.
The efficiency of systems.
The quality of work done.
The quantity of work done.
Technical innovation.
The utilization of resources—buildings, land, etc.
Equipment and vehicle utilization.
Involvement in the company's Corporate Plan.
This cannot be achieved by looking at artificial performance indices which measure only isolated areas of the total productivity mix, and lead to sub-optimization, e.g. quality is sacrificed for quantity, costs are spuriously transferred from one area to another—cold store to warehouse and vice versa. The concept of a comprehensive "unit" cost is simple and totally sensitive. It also permits alignment of productivity in financial terms to this contribution to company profit. The fundamental difficulty in application lies, of course, in defining the base "unit" to be used as the measure of output.
A new unit of measurement
Our thinking, not yet firmly established, is moving steadily towards the definition in agreement with the staff of a productivity "unit" which is much more convincing to everyone in measuring achievement and apportioning reward. This base "unit" of measure must conform to the following criteria. It must be: a} Applicable nationally within defined limits of accuracy, say,
+ Or — 5 per cent.
b) Simple_ c} Either self-adjusting or capable of easy adjustment to take account of changing characteristics in traffic mix. packaging, variability, etc.
d) Readily obtainable from company statistics.
e) Easily calculated.
f) Independent of expensive administrative support.
Previously, endeavours to discover an all-embracing, noncontroversial, nationally acceptable "unit" of measure have eluded management ingenuity. Traditionally, S. P. D. measured its output in tons until the significance of packaging and product diversification dictated a timely move to the "case unit". This remains the best available measure in a general sense, but it still fails to meet the criteria already listed as a basis for productivity assessment.
This then is the stage we have reached. Not without considerable achievement behind us, it may bethought we have travelled a long way from the basic concept of a lump sum paid annually, known as Progress Pay. Nevertheless, it appears that until now we have only been involved in clearing the ground so as to get a firm base. So far, our approach has been that of relating measured physical effort to remuneration and reward. That begins to look adolescent in the light of our recent experiences (including the fire), and the need for productivity and revvard to be somehow more closely related to the total involvement of men, machines and resources deployed to achieve firm objectives u nder d ecisive leadership.