Machine for Producing Glasspol Parts
Page 53
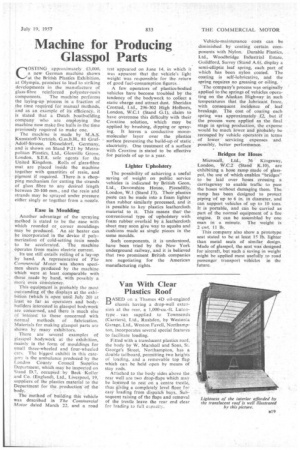
If you've noticed an error in this article please click here to report it so we can fix it.
COSTING approximately £3,000, a new German machine shown at the British Plastics Exhibition, at Olympia, promises to lead to striking developments in the manufacture of glass-fibre reinforced polyester-resin
components. The machine performs the laying-up process in a fraction of the time required for manual methods, and as an example of its efficiency, it is stated that a Dutch hoatbuilding company who are employing the machine now make five hulls in the time previously required to make one.
The machine is made by M.A.S. K.unststoff-Vertrieb, G.m.b.I-L, 81 GrafAdolf-Strasse, Diisseldorf, Germany, and is shown on Stand P.21 by Metropolitan Plastics, Ltd., Glenville Grove, London, S.E.8. sole agents for the United Kingdom. Rolls of glass-fibre mat are placed inside the machine together with quantities of resin, and pigment if required. There is a chopping mechanism for cutting the strands of glass fibre to any desired length between 20-100 mm., and the resin and strands may be sprayed under pressure either singly or together from a nozzle.
Ease in Moulding Another advantage of the spraying method is stated to be the ease with which rounded or corner mouldings may be produced. ' An air heater can be incorporated in the device if polymerization of cold-setting resin needs to be accelerated. The machine Operates from mains electric current.
Its use still entails rolling of a lay-up by hand. A representative of The Commercial Motor, was shown speciMen sheets produced by the machine which were at least comparable with -those made by hand, with possibly a more even consistency.
This equipment is probably the most outstanding of the displays at the exhibition (which is open until July 20) at least so far as operators and bodybuilders interested in giasspol bodywork are concerned, and there is much else of 'interest to those concerned with normal methods of fabrication. Materials for making glasspol parts are shown by many exhibitors.
There are several examples of glasspol bodywork at the exhibition, mainly in the form of mouldings for small three-wheeled and four-wheeled cars. The biggest exhibit in this category is the ambulance produced by the London County Council Supplies Department, which may be inspected on Stand D.7, occupied by Beck Koller and Co. (England), Ltd., Liverpool, 19, suppliers of the plastics material to the Department for the production' of the
body. ,
The method of building this vehicle was described in The Commercial Motor dated March 22, and a road
test appeared on June 14, in which it was apparent that the vehicle's light weight was responsible for the return of good fuel-consumption figures.
A few operators of plastics-bodied vehicles have become troubled by the tendency of the bodywork to collect a static charge and attract dust. Sheridan Croxted, Ltd., 296-302 High Holborn, London, w.ci (Stand 0.1), claim to have overcome this difficulty with their Croxtine solution, which may be applied by brushing, dipping or spraying. It leaves a conductive monomolecular layer over the plastics surface preventing the build-up of static electricity. One treatment of a surface with Croxtinc is stated to be effective for periods of up to a year.
Lighter Upholstery
The possibility of achieving a useful saving of weight on public service vehicles is indicated by British Geon, Ltd., Devonshire House, Piccadilly, London, W.1 (Stand J3). Their plastics paste can be made into a foam lighter than rubber similarly processed, and it is possible to key plastics leathercloth material to it. This means that' the conventional type of upholstery with foam rubber overlaid by a leathercloth sheet may soon give way to squabs and cushions made as single pieces in the same moulds.
Such components, it is -understood, have been tried by the New York underground railway, and it is believed that two prominent British companies are negotiating for the American manufacturing rights. Vehicle-maintenance costs can be diminished by coating certain components with Nylon. Durable Plastics, Ltd., Woodbridge Industrial Estate, Guildford, Surrey (Stand A.6), display a semi-elliptic leaf spring, each part of which has been nylon coated. The coating is self-lubricative, and the spring requires no greasing or oiling.
'The company's process was originally applied to the springs of vehicles operating on the Alaskan Highway in such temperatures that the lubricant froze, with consequent incidence of leaf breakage. The cost of coating each spring was approximately £2, but if the process were applied as the final stage in spring production, the expense would be much lower and probably be recouped by vehicle operators in terms of lower servicing expenses and, possibly, better performance.
•
Bridges for Hoses
Microcell, Ltd., 56 Kiagsway, London, W.C.2 (Stand K.10), are exhibiting a hose ramp made of glasspol, the use of which enables "bridges" to be laid over hoses crossing a carriageway to enable traffic to pass the hoses without damaging them. The ramp has been designed to protect piping of up to 6 in. in diameter, and can support vehicles of up to 10 tons. It is portable, and can be carried as part of the normal equipment of a fire engine. It can be assembled by one man in a minute. The weight is 2 cwt. 11 lb.
This company also show a prototype seat stated to be at least 15 lb. lighter than metal seats of similar design. Made of giasspol, the seat was designed for aircraft, but such a saving in weight might be applied most usefully to road passenger transport vehicles in the future.