Taking the gamble out of fleet maintenance
Page 32
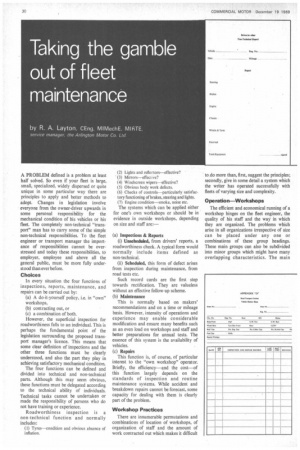
Page 33
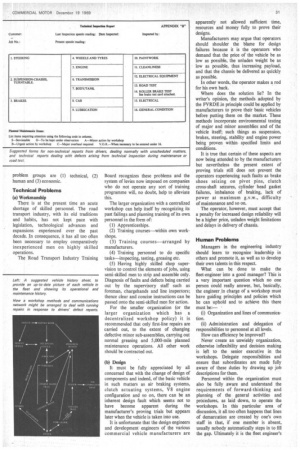
Page 34
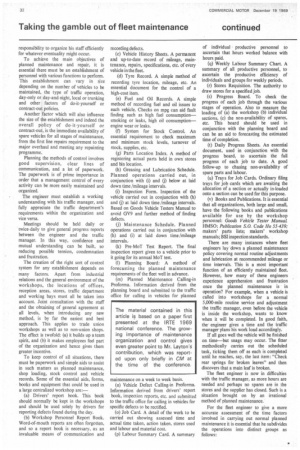
Page 35
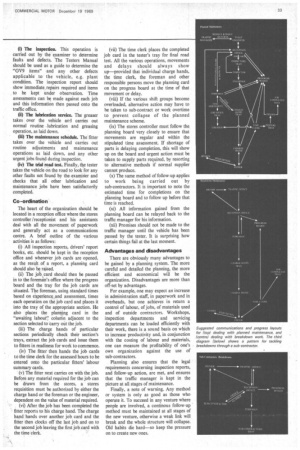
If you've noticed an error in this article please click here to report it so we can fix it.
by R. A. Layton, CEng, MIMechE, MIRTE,
service manages-, the Arlington Motor Co. Ltd.
A PROBLEM defined is a problem at least half solved. So even if your fleet is large, small, specialized, widely dispersed or quite unique in some particular way there are principles to apply and better methods to adopt. Changes in legislation involve everyone from the owner-driver upwards in some personal responsibility for the mechanical condition of his vehicles or his fleet. The completely non-technical "transport" man has to carry some of the simple non-technical responsibilities. To the fleet engineer or transport manager the importance of responsibilities cannot be overstressed and today these responsibilities, to employer, employee and above all the general public, must be more fully understood than ever before.
Choices In every situation the four functions of inspections, reports, maintenance, and repairs can be carried out by: (a) A do-it-yourself policy, i.e. in "own" workshops, (b) contracting out, or (c) a combination of both.
However, the superficial inspection for roadworthiness falls to an individual. This is perhaps the fundamental point of the legislation surrounding the proposed transport manager's licence. This means that some clear definition of inspections and the other three functions must be clearly understood, and also the part they play in achieving satisfactory mechanical condition.
The four functions can be defined and divided into technical and non-technical parts. Although this may seem obvious, these functions must he delegated according to the technical ability of individuals. Technical tasks cannot be undertaken or made the responsibility of persons who do not have training or experience.
Roadworthiness inspection is a non-technical function and normally includes: (I) Tyres—condition and obvious absence of inflation.
(2) Lights and reflectors—effective?
(3) Mirrors—effective?
(4) Windscreen wipers—effective?
(5) Obvious body work defects.
(6) Checks of controls—particularly satisfactory functioning of brakes, steering and lights.
(7) Engine condition—smoke, noise etc.
The systems which can be applied either for one's own workshops or should be in evidence in outside workshops. depending on size and staff are:—
(a) Inspections & Reports
(i) Unscheduled, from drivers' reports, a roadworthiness check. A typical form would normally include items defined as non-technical.
(ii) Scheduled, this form of defect arises from inspection during maintenance, from road tests etc.
Such record cards are the first step towards rectification. They are valueless without an effective follow-up scheme.
(b) Maintenance This is normally based on makers' recommendations and on a time or mileage basis. However, intensity of operations and experience may enable considerable modification and ensure many benefits such as an even load on workshops and staff and better preparations for annual tests. The essence of this system is the availability of vehicles.
(c) Repairs This function is, of course, of particular interest to the "own workshop" operator. Briefly, the efficiency—and the cost—of this function largely depends on the standards of inspection and routine maintenance systems. While accident and breakdown repairs cannot be forecast, some capacity for dealing with them is clearly part of the problem.
Workshop Practices There are innumerable permutations and combinations of location of workshops, of organization of staff and the amount of work contracted out which makes it difficult to do more than, first, suggest the principles: secondly, give in some detail a system which the writer has operated successfully with fleets of varying size and complexity.
Operation—Workshops
The efficient and economical running of a workshop hinges on the fleet engineer, the quality of his staff and the way in which they are organized. The problems which arise in all organizations irrespective of size can be placed under any one or combinations of these group headings. These main groups can also be subdivided into minor groups which might have many overlapping characteristics. The main problem groups are (I) technical, (2) human and (3) economic.
Technical Problems
(a) Workmanship
There is at the present time an acute shortage of skilled personnel. The road transport industry, with its old traditions and habits, has not kept pace with legislation, technological advances and expansions experienced over the past decade. In consequence, it has all too often been necessary to employ comparatively inexperienced men on highly skilled operations.
The Road Transport Industry Training Board recognizes these problems and the system of levies now imposed on companies who do not operate any sort of training programme will, no doubt, help to alleviate this.
The larger organization with a centralized workshop can help itself by recognizing its past failings and planning training of its own personnel in the form of: (1) Apprenticeships.
(2)Training courses—within own workshops_ (3) Training courses—arranged by manufacturers_ (4) Training personnel to do specific tasks—inspecting, testing, greasing etc.
(5) Having highly skilled shop supervision to control the elements of jobs, using semi-skilled men to strip and assemble only. Diagnosis of faults and defects being carried out by the supervisory staff such as foreman, chargehands and line inspectors; thence clear and concise instructions can be passed onto the semi-skilled men for action_ For the smaller organization (or the larger organization which has a decentralized workshop policy) it is recommended that only first-line repairs are carried out, to the extent of changing defective minor sub-assemblies, carrying out normal greasing and 5,000-mile planned maintenance operations_ All other work should be contracted out.
(b) Design
It must be fully appreciated by all concerned that with the change of design of components and indeed, of the basic vehicle in such matters as air braking systems, clutch actuating systems, V8 engine configuration and so on, there can be an inherent design fault which seems not to have become apparent during the manufacturer's proving trials but appears later when the vehicle is taken into use.
It is unfortunate that the design engineers and development engineers of the various commercial vehicle manufacturers are apparently not allowed sufficient time, resources and money fully to prove their designs.
Manufacturers may argue that operators should shoulder the blame for design failures because it is the operators who demand that the price of the vehicle be as low as possible, the unladen weight be as low as possible, thus increasing payload, and that the chassis be delivered as quickly as possible.
In other words, the operator makes a rod for his own back.
Where does the solution lie? In the writer's opinion, the methods adopted by the FVRDE in principle could be applied by manufacturers to prove their basic vehicles before putting them on the market. These methods incorporate environmental testing of major and minor assemblies and of the vehicle itself; such things as suspension, brakes, steering, stability and engine power being proven within specified limits and conditions.
It is true that certain of these aspects are now being attended to by the manufacturers but nevertheless the present extent of proving trials still does not prevent the operators experiencing such faults as brake shoes seizing on pivot pins, clutch cross-shaft seizures, cylinder head gasket failures, imbalance of braking, lack of power at maximum g.v.w., difficulty of maintenance and so on.
The operator, however, must accept that a penalty for increased design reliability will be a higher price, unladen weight limitations and delays in delivery of chassis.
Human Probiems Managers in the engineering industry should learn to recognize leadership in others and promote it, as well as to develop their own talents in this respect What can be done to make the fleet-engineer into a good manager? This is a very important question which no one person could really answer, but, basically, the engineer in charge of a workshop must have guiding principles and policies which he can uphold and to achieve this there must be:— (1) Organization and lines of communication.
(ii) Administration and delegation of responsibilities to personnel at all levels.
How can efficiency be improved?
Never create an unwieldy organization, otherwise inflexibility and decision making is left to the senior executive in the workshops. Delegate responsibilities and ensure that subordinates are made fully aware of these duties by drawing up job descriptions for them.
Personnel within the organization must also be fully aware and understand the requirements of forward-thinking and planning of the general activities and procedures, as laid down, to operate the workshops. In this particular area of discussion, it all too often happens that lines of demarcation are created by one's own staff in that, if one member is absent, usually nobody automatically steps in to fill the gap. Ultimately it is the fleet engineer's responsibility to organize his staff efficiently for whatever eventuality might occur.
To achieve the main objectives of planned maintenance and repair, it is essential there must be an establishment of personnel with various functions to perform. This establishment can vary in size depending on the number of vehicles to be maintained, the type of traffic operation, day-only or day-and-night, local or trunking and other factors of do-it-yourself or contract-out policies.
Another factor which will also influence the size of the establishment and indeed the overall policy of do-it-yourself or contract-out, is the immediate availability of spare vehicles for all stages of maintenance, from the first line repairs requirement to the major overhaul and meeting any repainting programme.
Planning the methods of control involves good supervision, clear lines of communication, and a lot of paperwork. The paperwork is of prime importance in order that a management control of every activity can be more easily maintained and organized.
The engineer must establish a working understanding with his traffic manager, and fully appreciate the traffic department's requirements within the organization and vice versa.
Meetings should be held daily or twice-daily to give general progress reports between the engineer and the traffic manager. In this way, confidence and mutual understanding can be built, so reducing possible tension, condemnation and frustration.
The creation of the right sort of control system for any establishment depends on many factors. Apart from industrial relations and the general environment of the workshops, the locations of offices, reception areas, stores, traffic department and working bays must all be taken into account. Joint consultation with the staff and the obtaining of general agreement at all levels, when introducing any new method, is by far the easiest and best approach. This applies to trade union workshops as well as to non-union shops. The effect is twofold: (a) it builds up a team spirit, and (b) it makes employees feel part of the organization and hence gives them greater incentive.
To keep control of all situations, there must be paperwork and simple aids to assist in such matters as planned maintenance, shop loading, stock control and vehicle records. Some of the essential aids, forms, books and equipment that could be used in a large centralized workshop are:—
(a) Drivers' report book. This book should normally be kept in the workshops and should be used solely by drivers for reporting defects found during the day.
(b) Workshop Personnel Report Book. Word-of-mouth reports are often forgotten, and so a report book is necessary, as an invaluable means of communication and recording defects.
(c) Vehicle History Sheets. A permanent and up-to-date record of mileage, maintenance, repairs, specifications, etc. of every vehicle in the fleet.
(d) Tyre Record. A simple method of recording tyre location, mileage, etc. An essential document for the control of a high-cost item.
(e) Fuel and Oil Records. A simple method of recording fuel and oil issues to each vehicle. Checks on mpg can aid fault finding such as high fuel consumption— smoking or leaks, high oil consumption— engine wear or leaks.
(f) System for Stock Control. An essential requirement to check maximum and minimum stock levels, turnover of stock, supplies, etc.
(g) Parts Location Index. A method of registering actual parts held in own stores and bin location.
(h) Greasing and Lubrication Schedule. Planned operations carried out, in conjunction with (i) and (j) below at laid down time /mileage intervals.
(i) Inspection Form. Inspection of the vehicle carried out in conjunction with (h) and (j) at laid down time /mileage intervals. Based on Goods Vehicle Testers Manual to avoid GV9 and further method of finding defects.
(j) Maintenance Schedule. Planned operations carried out in conjunction with (h) and (i) at laid down time /mileage intervals.
(k) Pre-MoT Test Report. The final inspection report given to a vehicle prior to it going for its annual MoT test.
(1) Planning Board: A method of forecasting the planned maintenance requirements of the fleet well in advance.
(m) Planned Maintenance Calling-in Proforma. Information derived from the planning board and submitted to the traffic office for calling in vehicles for planned maintenance on a week to week basis.
(n) Vehicle Defect Calling-in Proforma. Information derived from drivers' report book, inspection reports, etc. and submitted to the traffic office for calling in vehicles for specific defects to be rectified.
(o) Job Card. A detail of the work to be carried out showing assessed time and actual time taken, action taken, stores used and labour and material cost.
(p) Labour Summary Card. A summary of individual • productive personnel to ascertain that hours worked balance with hours paid.
(q) Weekly Labour Summary Chart. A summary of all productive personnel, to ascertain the productive efficiency of individuals and groups for weekly periods.
(r) Stores Requisition. The authority to draw stores for a specified job.
(s) Progress Board. To check the progress of each job through the various stages of operation. Also to measure the loading of (a) the workshop (b) individual sections, (c) the non-availability of spares, etc. This board should be used in conjunction with the planning board and can be an aid to forecasting the estimated time of completion.
(t) Daily Progress Sheets. An essential document, used in conjunction with the progress board, to ascertain the full progress of each job to date. A good follow-up to chasing non-availability of spare parts and labour.
(u) Trays for Job Cards. Ordinary filing trays for job cards which are awaiting the allocation of a section or actually in-loaded onto a section can be used for this purpose.
(v) Books and Publications. It is essential that all organizations, both large and small, have the following books and publications available for use by the workshop personnel: Goods Vehicle Tester Manua HMSO: Publication S.O. Code Ho 55-439; makers' parts lists; makers' workshop manuals; BSI inspection standards.
There are many instances where fleet engineers lay down a planned maintenance policy covering normal routine adjustments and lubrication at recommended mileage or time intervals. This is a most important function of an efficiently maintained fleet.
However, how many of these engineers experience apprehension and frustration once the planned maintenance is in operation? For example, when a vehicle is called into workshops for a normal 5,000-mile routine service and adjustment the traffic manager, even before the vehicle is inside the workshop, wants to know when it will be completed. In good faith, the engineer gives a time and the traffic manager plans his work load accordingly.
If all goes well the vehicle will be finished on time—but snags may occur. The fitter methodically carries out the scheduled task, ticking them off as each is completed until he reaches, say, the last item: "Check rear springs for broken leaves" and then discovers that a main leaf is broken.
The fleet engineer is now in difficulties with the traffic manager, as more hours are needed and perhaps no spares are in the stores and the supplier has closed. Such is a situation brought on by an irrational method of planned maintenance.
For the fleet engineer to give a more accurate assessment of the time factors involved in carrying out normal planned maintenance it is essential that he subdivides the operations into distinct groups as follows:
(i) The inspection. This operation is carried out by the examiner to determine faults and defects. The Testers Manual
should be used as a guide to determine the "GV9 items" and any other defects applicable to the vehicle, e.g. plant condition. The inspection report should show immediate repairs required and items to be kept under observation. Time assessments can be made against each job and this information then passed onto the traffic office.
(ii) The lubrication service. The greaser takes over the vehicle and carries out normal routine lubrication and greasing operation, as laid down.
(iii) The maintenance schedule. The fitter takes over the vehicle and carries out
routine adjustments and maintenance operations as laid down, and any other urgent jobs found during inspection.
(iv) The trial road test. Finally, the tester takes the vehicle on the road to look for any other faults not found by the examiner and checks that all other lubrication and maintenance jobs have been satisfactorily completed.
Co-ordination
The heart of the organization should be located in a reception office where the stores controller /receptionist and his assistants deal with all the movement of paperwork and generally act as a communications centre. A brief outline of the various activities is as follows: (i) All inspection reports, drivers' report books, etc_ should be kept in the reception office and whenever job cards are opened, as the result of a report, a planning card should also be raised_
(ii) The job card should then be passed in to the foreman's office where the progress
board and the tray for the job cards are situated. The foreman, using standard times based on ekperience and assessment, times each operation on the job card and places it into the tray of the appropriate section. He also places the planning card in the "awaiting labour column adjacent to the section selected to tarry out the job.
(iii) The charge hands of particular sections periodically check their section's trays, extract the job cards and issue them to fitters in readiness for work to commence.
(iv) The fitter then hands the job cards to the time clerk for the assessed hours to be entered onto the particular fitters' labour summary cards_ (v) The fitter next carries on with the job. Before any material required for the job can be drawn from the stores, a stores requisition must be authorized by either the charge hand or the foreman or the engineer, dependent on the value of material required.
(vi) After the job has been completed the fitter reports to his charge hand. The charge hand hands over another job card and the fitter then clocks off the last job and on to the• second job leaving the first job card with the time clerk. (vii) The time clerk places the completed job card in the tester's tray for final road test. All the various operations, movements and delays should always show up—provided that individual charge hands, the time clerk, the foreman and other responsible persons move the planning card on the progress board at the time of that movement or delay.
(viii) If the various shift groups become overloaded, alternative action may have to be taken to sub-contract or work overtime to prevent collapse of the planned maintenance scheme_ (ix) The stores controller must follow the planning board very closely to ensure that movements are regular and within the stipulated time assessment. If shortage of parts is delaying completion, this will show up on the board and urgent action must be taken to supply parts required, by resorting to alternative methods if normal supplier cannot produce.
(x) The same method of follow-up applies to work being carried out by sub-contractors. It is important to note the estimated time for completions on the planning board and to follow up before that time is reached_ (xi) All information gained from the planning board can be relayed back to the traffic manager for his information.
(xii) Promises should not be made to the traffic manager until the vehicle has been passed by the tester. It is surprising how certain things fail at the last moment.
Advantages and disadvantages
There are obviously many advantages to be gained by a planning system. The more careful and detailed the planning, the more efficient and economical will be the organization. Disadvantages are more than off-set by advantages.
For example, one may expect an increase in administration staff, in paperwork and in overheads, but one achieves in return a control of labour, of jobs, of materials used and of outside contractors. Workshops, inspection departments and servicing departments can be loaded efficiently with their work, there is a sound basis on which to increase productivity and, in conjunction with the costing of labour and materials, one can measure the profitability of one's own organization against the use of sub-contractors.
Planning also ensures that the legal requirements concerning inspection reports, and follow-up action, are met, and ensures that the traffic manager is kept in the picture at all stages of maintenance.
Finally, a note of warning. Any method or system is only as good as those who operate it. To succeed in any venture where people are involved, a continous follow-up method must be maintained at all stages of the new venture, otherwise a weak link will break and the whole structure will collapse. Old habits die hard—so keep the pressure on to create new ones.