Growing pains easec Dy articulation
Page 24
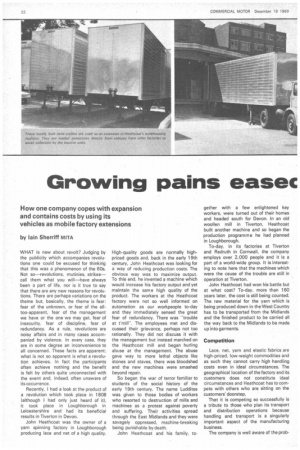
Page 25
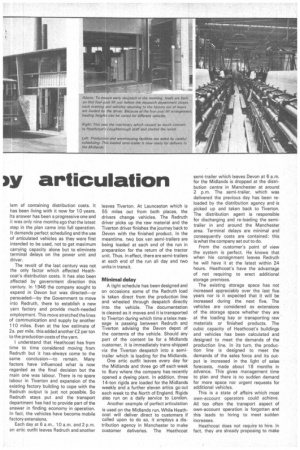
Page 26
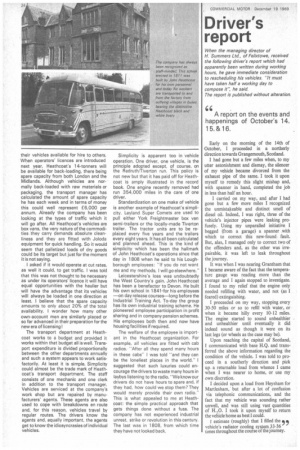
If you've noticed an error in this article please click here to report it so we can fix it.
How one company copes with expansion and contains costs by using its vehicles as mobile factory extensions by lain Sherriff MITA
WHAT is new about revolt? Judging by the publicity which accompanies revolutions one could be excused for thinking that this was a phenomenon of the 60s. Not so—revolutions, mutinies, strikes— call them what you will—have always been a part of life, nor is it true to say that there are any new reasons for revolutions. There are perhaps variations on the theme but, basically, the theme is fear: fear of the unknown, or fear of the alltoo-apparent, fear of the management we have or the one we may get, fear of insecurity, fear of discipline, fear of redundancy. As a rule, revolutions are noisy affairs and in many cases accompanied by violence. In every case, they are in some degree an inconvenience to all concerned. These facts are apparent; what is not so apparent is what a revolution achieves. In fact the participants often achieve nothing and the benefit is felt by others quite unconnected with the event and, indeed, often unaware of its occurrence.
Recently. I had a look at the product of a revolution which took place in 1808 (although I had only just heard of it). It took place in Loughborough in Leicestershire and had its beneficial results in Tiverton in Devon.
John Heathcoat was the owner of a yarn spinning factory in Loughborough producing lace and net of a high quality. High-quality goods are normally highpriced goods and, back in the early 19th century, John Heathcoat was looking for a way of reducing production costs, The obvious way was to maximize output. To this end, he invented a machine which would increase his factory output and yet maintain the same high quality of the product. The workers at the Heathcoat factory were not so well informed on automation as our workpeople to-day and they immediately sensed the great fear of redundancy. There was "trouble at frnill". The employees met and discussed their grievance, perhaps not too rationally. They did not discuss it with the management but instead marched on the Heathcoat mill and began hurling abuse at the management. The abuse gave way to more lethal objects like stones and staves, there was bloodshed and the new machines were smashed beyond repair.
So began the war of terror familiar to students of the social history of the early 19th century, The name Luddites was given to those bodies of workers who resorted to destruction of mills and machines as a protest against poverty and suffering. Their activities spread through the East Midlands and they were savagely oppressed, machine-breaking being punishable by death.
John Heathcoat and his family, to
gether with a few enlightened key workers, were turned out of their homes and headed south for Devon. In an old woollen mill in Tiverton, Heathcoat built another machine and so began the production programme he had planned in Loughborough.
To-day, in its factories at Tiverton and Redruth in Cornwall, the company employs over 2,000 people and it is a part of a world-wide group. It is interesting to note here that the machines which were the cause of the trouble are still in operation at Tiverton.
John Heathcoat had won his battle but at what cost? To-day, more than 160 years later, the cost is still being counted, The raw material for the yarn which is being produced down in the West Country has to be transported from the Midlands and the finished product to be carried all the way back to the Midlands to be made up into garments.
Competition Lace, net, yarn and elastic fabrics are high-priced, low-weight commodities and as such they cannot carry high handling costs even in ideal circumstances. The geographical location of the factory and its customers does not constitute ideal circumstances and Heathcoat has to compete with others who are sitting on the customers' doorstep.
That it is competing so successfully is a tribute to those who plan its transport and distribution operations because handling and transport is a singularly important aspect of the manufacturing business.
The company is well aware of the prob lem of containing distribution costs. It has been living with it now for 10 years. Its answer has been a progressive one and it was only nine months ago that the latest step in the plan came into full operation. It demands perfect scheduling and the use of articulated vehicles as they were first intended to be used, not to get maximum carrying capacity alone but to eliminate terminal delays on the power unit and driver.
The revolt of the last century was not the only factor which affected Heathcoat's distribution costs. It has also been affected by government direction this century. In 1 946 the company sought to expand in Devon but was directed—or persuaded—by the Government to move into Redruth, there to establish a new yarn factory and provide much-needed employment. This move stretched the lines of communication and supply by another 110 miles. Even at the low estimate of 2s. per mile, this added another £2 per ton to the production costs of the yarn.
I understand that Heathcoat has from time to time considered moving from Redruth but it has always come to the same conclusion—to remain. Many factors have influenced what is now regarded as the final decision but the main one was labour. There is no spare labour in Tiverton and expansion of the existing factory building to cope with the Redruth output is just not possible. So Redruth stays put and the transport department has had to provide part of the answer in finding economy in operation. In fact, the vehicles have become mobile factory extensions.
Each day at 6 a.m., 10 a.m. and 2 p.m. an artic outfit leaves Redruth and another leaves Tiverton. At Launceston which is 55 miles out from both places, the drivers change vehicles. The Redruth driver picks up the raw material and the Tiverton driver finishes the journey back to Devon with the finished product. In the meantime, two box van semi-trailers are being loaded at each end of the run in preparation for the return of the tractor unit. Thus, in effect, there are semi-trailers at each end of the run all day and two units in transit.
Minimal delay
A tight schedule has been designed and on occasions some of the Redruth load is taken direct from the production line and wheeled through despatch directly into the vehicle. The documentation is cleared as it moves and it is transported to Tiverton during which time a telex message is passing between Redruth and Tiverton advising the Devon depot of the contents of the vehicle. Should any part of the content be for a Midlands customer, it is immediately trans-shipped via the Tiverton despatch into a semitrailer which is loading for the Midlands.
One artic outfit leaves every day for the Midlands and three go off each week to Bury where the company has recently opened a dyeing plant. In addition, three 14-ton rigids are loaded for the Midlands weekly and a further eleven artics go out each week to the North of England. Rigids also run on a daily service to London.
Another example of perfect articulation is used on the Midlands run. While Heathcoat will deliver direct to customers if called upon to do so. it employs a distribution agency in Manchester to make customer deliveries. The Heathcoat
semi-trailer which leaves Devon at 6 a.m. for the Midlands is dropped at the distribution centre in Manchester at around 2 pin. The semi-trailer, which was delivered the previous day has been reloaded by the distribution agency and is picked up and taken back to Tiverton. The distribution agent is responsible for discharging and re-loading the semitrailer in and around the Manchester area. Terminal delays are minimal and consequently costs are contained: this is what the company set out to do.
From the customer's point of view the system is perfect. He knows that when his consignment leaves Redruth he will have it at the latest within 24 hours. Heathcoat's have the advantage of not requiring to erect additional storage premises.
The existing storage space has not increased appreciably over the last five years nor is it expected that it will be increased during the next five. The vehicles are considered as extensions of the storage space whether they are at the loading bay or transporting raw materials or finished products. The cubic capacity of Heathcoat's buildings and vehicles has been calculated and designed to meet the demands of the production line. In its turn, the production line is designed to meet the demands of the sales force and its output is increased in the light of sales forecasts, made about 18 months in advance. This gives management time to plan and there is no sudden demand for more space nor urgent requests for additional vehicles.
This is a state of affairs which most own-account operators could achieve. All too often the transport aspect of own-account operation is forgotten and this leads to hiring to meet sudden increases.
Heathcoat does not require to hire. In fact, they are already proposing to make their vehicles available for hire to others. When operators licences are introduced next year. Heathcoat's 14-tonners will be available for back-loading, there being spare capacity from both London and the Midlands, Although vehicles are normally back-loaded with raw materials or packaging, the transport manager has calculated the amount of spare capacity he has each week and in terms of money this could well represent £6,000 per annum. Already the company has been looking at the types of traffic which it will go after. All Heathcoat's vehicles are box vans, the very nature of the commodities they carry demands absolute cleanliness and they are fitted with Joloda equipment for quick handling. So it would seem that palletized loads of dry goods could be its target but just for the moment it is not saying.
I asked if it would operate at cut rates, as well it could, to get traffic. I was told that this was not thought to be necessary as under its operators' licence it will have equal opportunities with the haulier but will have the advantage that its vehicles will always be loaded in one direction at least, I believe that the spare capacity amounts to only about 20% of the total availability. I wonder how many other own-account men are similarly placed or so far advanced in their preparation for the new era of licensing !
The transport department at Heathcoat works to a budget and provided it works within that budget all is well. Transport expenditure is divided proportionally between the other departments annually and such a system appears to work satisfactorily. At least it is simple. Simplicity could almost be the trade mark of Heathcoat's transport department. The staff consists of one mechanic and one clerk in addition to the transport manager. Vehicles are serviced at the company's work shop but are repaired by manufacturers' agents. These agents are also used to cope with breakdowns en route and, for this reason, vehicles travel by regular routes. The drivers know the agents and, equally important, the agents get to know the idiosyncrasies of individual vehicles. Simplicity is apparent too in vehicle operation. One driver, one vehicle, is the principle adopted except, of course, on the Redruthaiverton run. This policy is not new but that it has paid off for Heathcoat is amply illustrated in the record book. One engine recently removed had run 354,000 miles in the care of one driver.
Standardization on one make of vehicle is another example of Heathcoat's simplicity. Leyland Super Comets are used to pull either York Freightmaster box van semi-trailers or the locally-made Tiverton trailer. The tractor units are to be replaced every five years and the trailers every eight years. It has all been calculated and planned ahead. This is the kind of simplicity which has been the hallmark of John Heathcoat's operations since that day in 1808 when he said to his Loughborough employees: "If you do not want me and my methods, I will go elsewhere."
Leicestershire's loss was undoubtedly the West Country's gain, John Heathcoat has been a benefactor to Devon. He built his own school in 1841,for his employees —on day release courses—long before the Industrial Training Act. To-day the group has its own industrial training scheme. He pioneered employee participation in profit sharing and in company pension schemes. His employees both then and now have housing facilities if required.
The welfare of the employee is important in the Heathcoat organization. For example, all vehicles are fitted with cab radios. "After all they spend many hours in these cabsI was told -and they can be the loneliest places in the world." I suggested that such luxuries could encourage the drivers to waste many hours in iaybys listening to the radio. "We know our drivers do not have hours to spare and, if they had, how could we stop them? They would merely provide their own radio.This is what appealed to me at Heathcoat: the simple practical approach that gets things done without a fuss. The company has not experienced industrial unrest, strike or revolution in this century. The last was in 1808, from which time they have not looked back.