Cures for Tyre and Mechanical Troubles
Page 59
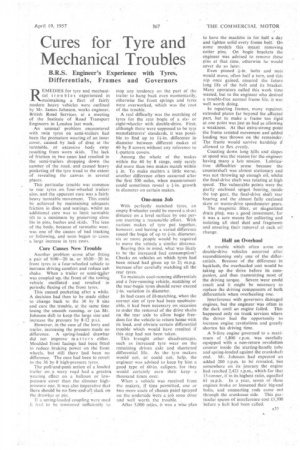
If you've noticed an error in this article please click here to report it so we can fix it.
B.R.S. Engineer's Experience with Tyres, Differentials, Frames and Governors
REMED1ES for tyre and mechanical troubles experienced in maintaining a fleet of fairly modern heavy vehicles were outlined by Mr. James Johnson, works engineer, British Road Services, at a meeting of the Institute of Road Transport Engineers in London last week.
An unusual problem encountered with twin tyres on semi-trailers had been the 'premature wearing of an inner cover, caused by lack of drag at the turntable, or excessive .body sway resulting from worn skids, The lack of friction in two cases had resulted in the semi-trailers dropping down the camber of the road. and caused heavy pocketing of the tyre tread to the extent of revealing the canvas in several places.
This particular trouble was common to rear tyres on four-wheeled trailers also, and the apparent cure was a fairly heavy turntable movement This could be achieved by maintaining adequate friction in discs and seatings, whilst an additional cure was to limit turntable tilt to a minimum by preServing close fits in pins, bushes and.skids. The lean of the body, because of turntable wear, was one of the causes of bad tracking or following, and soon began to cause a large increase in tyre costs.
Cure Causes New Trouble
Another problem -arose after fitting a pair of 9.00-20 in. or 10.00-20 in. front tyres to a four-wheeled vehicle to increase driving comf on and reduce cab shake. When a trailer or semi-t4ler was coupled up, the front of the towing vehicle oscillated and resulted in periodic flexing ofthe front tyres.
This caused pocketing after a while. A decision had then to be made either to change back to the 36 by 8 size and cure the trouble, at the same time losing the smooth running, or (as Mr. Johnson did) to keep the large size-and increase the pressure by 8-12 p.s.i.
However, in the case of the lorry and trailer, increasing the pressure made no difference. A spring-loaded drawbar did not improve matters either. Moulded front facings had been fitted to reduce braking power on the front wheels, but still there had been no difference. The cure had been to revert to the 36 by 8 high-pressure tyres, The pull-and-push action of a loaded trailer on, a. wavy road had a greateni wearing effect on a balloon or lowpressure cover than the slimmer highpressure one. It was also imperative that there should be no fore-and-aft slack on the drawbar or pin.
If a spring-loaded coupling were used it had. to be tensioned sufficiently to stop any tendency on the part of the trailer to hang back even momentarily, otherwise the front springs and tyres were overworked, which was the root of the trouble.
A real difficulty was the snatching of tyres for the rear bogie of a sixor eight-wheeler with double-drive. First; although there were supposed to be tyre manufatturers' standards, it was possible., to find up to 14-in, difference in diameter between different makes of 40 by 8 covers without any reference to L-pattern covers.
Among etc whole of the Makes within the 40 by 8 range, only rarely .did more than two makes match within +, in. To make matters a little worse, another difference often occurred. after the first 500 miles, when measurement could sometimes reveal a growth in diameter on certain makes.
One-man Job
With perfectly matched tyres, an empty 8-wheeler could be moved a short distance on a level surface by one person exerting a reasonable effort. With various makes of tyre put together, however, and having a varied difference round the bogie of up to Fin, diameter, six or more people would be required to move the vehicle a similar distance.
Bearing this in mind, what was likely to be the increased fuel consumption'? Checks on vehicles on which tyres had been mixed had given up to 2+ m.p.g. increase after carefully matching all the rear tyres.
To maintain cool-running differentials and a free-running vehicle, matching of the rear-bogie tyres should never exceed 1-in. variation in diameter.
In bad cases of illAnatching, when the correct size of tyre had been unobtainable, it had been necessary on occasion to order the removal of the drive shafts on the rear axle to allow bogie freedom for the vehicle to return home with its load, and obviate certain differential trouble which would have resulted if this step had not been taken.
This brought other disadvantages, such as increased tyre wear on the remaining driven axle and shortened differential life, As the tyre makers would not, or could not, help, the engineer was advised to keep by him a good type of 60-in, calipers, for they would certainly earn their keep a thousand times over.
When a vehicle was received from the makers, if time permitted, one or two more coats of chassispaint sprayed on the underside were a job soon done and well worth the trouble.
After 5,000 miles, it was a wise plan to have the machine in for half a day and tighten solid every frame bolt: On some models this meant removing cotter pins. On bogie brackets the engineer was advised to remove these pins at that time, otherwise he would never do so later.
Even pinned frin, bolts and nuts would move, often half a turn, and this nip once gained, ensured the future long life of the bolt and its bracket. Many operators called this work time wasted, but to the engineer who desired a trouble-free normal frame life, it was well worth doing.
In repairing frames, many repairers extended plates far beyond the affected part, but to make a frame too rigid at one point was just as bad as allowing a .weakness. At that extra-strong point the frame resisted movement and added loading was thrown on the remainder.
• The fratte would survive hardship if allowed to flex evenly.
Coasting down long hills and slopes -at speed was the reason for the engineer having many a late session. Lubrication difficulties arose because the
• countershaft was almost stationary and was not throwing up enough oil, whilst the final-drive shaft was rotating at high speed. The vulnerable points were the partly enclosed spigot bearing_ inside the top gear, the final-drive shaft rear bearing and the almost fully enclosed skew or worm-drive speedometer gears.
The magnetic filter, or Magnetized drain plug, was a good investment, for it was a sure means for collecting and isolating all steel dust and fragments and ensuring their removal at each oil change.
Half an Overhaul
A trouble which often arose on double-drive vehicles occurred after reconditioning only one of the differentials. Because of the difference in b4cklash, the overhauled unit would be taking up the drive before its companion, and thus transmitting most of the driving torque. Severe Wear could result and it might be necessary to replace the driving components of both differentials when overhauling one.
Interference with governors damaged engines, but the engineer', was often in the dark until an engine failed. This happened only on trunk services where the driver had the opportunity to increase engine revolutions and greatly shorten his driving time.
A 9-litre engine governed to a maximum of 1,800 r.p.m. was carefully equipped with a non-return revolution counter inside the starting-handle tube and spring-loaded against the crankshaft end. Mr. Johnson had expected an added 200 r.p.m. to be revealed, but somewhere on its journey the engine had reached 2,421 r.p.m., which for that 15-tonner, if in its highest ratio, equalled 61 m.p.h. In a year, seven of these engines broke or loosened their big-end bolts, and connecting rods came out through the crankcase side. This particular spasm of interference cost £1,300 before a halt had been called.