PREVENTABLE PIN-PRICKS.
Page 65
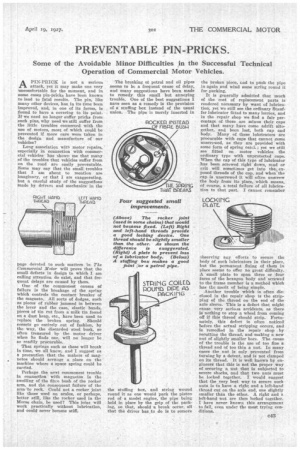
If you've noticed an error in this article please click here to report it so we can fix it.
Some of the Avoidable Minor Difficulties in the Successful Technical Operation of Commercial Motor Vehicles.
APIN-PRICK is not a serious attack, yet it may make one very uncomfortable for the moment, and in some cases pin-pricks have been known to lead to fatal results. The pin, like many other devices, has in its time been improved, and, in one of its forms, is found to have a covering to its point. If we need no longer suffer pricks from such pins, why need we still suffer from the little troubles connected with the use of motors, most of which could be prevented if more care were taken in the design and manufacture of our vehicles?
Long association with motor repairs, especially in connection with commercial vehicles has shown me that many of the troubles that vehicles suffer from on the road are easily preventable. Some may say that the small troubles that I am about to mention are imaginary, or that I am exaggerating, hut a careful study of the suggestions made by drivers and mechanics in the
page devoted to such matters in The Commercial Motor will prove that the small defects in design to which I am calling attention do exist, and that frequent delays are caused by them.
One of the commonest causes of failure is the breakage of the spring which controls the contact breaker of the magneto. All sorts of dodges, such • as pieces of rubber jammed in between the lever and the case, elastic bands, pieces of tin cut from a milk tin found on a dust heap, etc., have been used to replace the broken spring. Should corsets go entirely out of fashion, by the way, the discarded steel busk, so often treasured by the motor driver when he finds one, will no longer be so readily procurable.
That springs such as these will break In time, we all know, and I suggest as a precaution that the makers of magnetos should arrange a place on the machine where a spare spring could he carried.
Perhaps the next commonest trouble in connection with magnetos is the swelling of the fibre bush of the rocker arm, and the consequent failure of the arm to rock. Could not a rocker joint like those used on scales, or perhaps, better still, like the rocker used in the Morse chain, be used? This joint will work practically without lubrication, and could never become stiff.
The breaking oi petrol and oil pipes seems to be a frequent cause of delay, and many suggestions have been made to remedy this small but annoying trouble. One of the best suggestions 1 nave seen as a remedy is the provision of a stuffing box instead of the usual union. The pipe is merely inserted in the stuffing box, and string wound round it as one would pack the piston rod of a model engine, the pipe being held in place by the grip of the packing, so that, should a break °emir, all that the driver has to do is to remove
the broken piece, and to push the pipe in again and wind some string round it for packing.
It is generally admitted that much of the cost of replacement Parts is rendered necessary by want of lubrication, yet we still see the ordinary Stauffer lubricator fitted to many lorries, and in the repair shop we find a fair percentage of these are minus their caps and that many have come adrift altogether, and been lost, both cap and body. Many of those lubricators are procurable with caps that cannot come unscrewed, as they are provided with some form of spring catch ; yet we still see fitted on motor vehicles the ordinary type with unprotected caps. When the cap of this type of lubricator has been screwed right down, mud or grit will sometimes get into the exposed threads of the cap, and when the cap is unscrewed it will often unscrew the body from its place, which means, of course, a total failure of all lubrication to that part. I cannot remember observing any efforts to secure the body of such lubricators in their place, but the permanent fixing of them in place seems to offer no great difficulty. A small plate to span three or four faces of the hexagon body and screwed to the frame member is a method which has the merit of being simple.
Another trouble which is often disclosed in the repair shop is the stripping of the thread on the end of the axle sleeve. This is a defect that might cause very seriosts accidents, as there is nothing to stop a wheel from coming _ off if this thread should strip. Fortunately, this defect is often noticed before the actual stripping occurs, and is remedied in the repair shop by recutting the thread, and making a new nut of slightly smaller bore. The cause of the trouble is the use of too fine a thread and of too thin a nut. In many cases the nut is only prevented from turning by a detent, and is not clamped on its thread. It is well known by engineers that this is not the proper way of securing a nut that is subjected to severe shocks, and that two nuts must be locked together. I would suggest that the _very best way to secure such nuts is to have a right and a loft-hand thread cut on the axle end, one slightly smaller than the other. A right and a left-hand nut are then locked together. I have never known this arrangement to fail, even under the most trying conditions.