Control and Construction of
Page 34
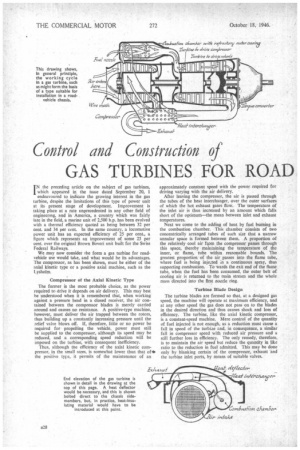
Page 35
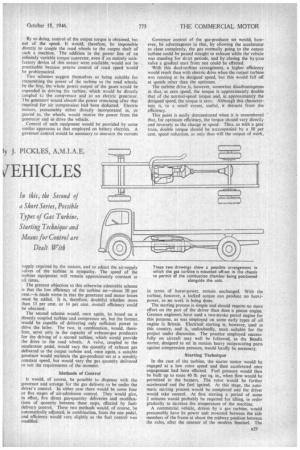
Page 36
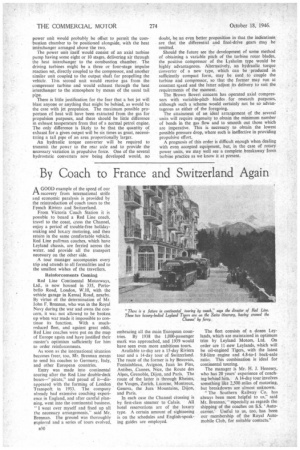
If you've noticed an error in this article please click here to report it so we can fix it.
GAS TURBINES FOR ROAD 7EHICLES
IN the preceding article on the stibject of gas turbines, which appeared in the issue dated September 20, 1 endeavoured to indicate the growing interest in the gas turbine, despite the limitations of this type of power unit at its present stage of development. Improvement is taking place at a rate unprecedented in any other field of engineering, and in America, a country which was fairly late in the field, a marine unit of 2,500 h.p. has been evolved with a thermal efficiency quoted as being between 32 per cent. and 34 per centin the same country, a locomotive power unit has an expected efficiency of 25 per cent., a figure which represents an improvement of some 25 per cent. over the original Brown Boveri unit built for the Swiss Federal Railways.
We may now consider the form a gas turbine for roadvehicle use would take, and what would be its advantages. The compressor, as has been shown, must be either of the axial kinetic type or a positive axial machine, such as the Lysholm.
Compressor of the Axial Kinetic Type The former is the most probable choice, as the power required to drive it depends on air delivery. This may best be understood when it is remembered that, when working against a pressure head in a closed receiver, the air contained between the compressor blades is merely carried around and causes no resistance. A positive-type machine, however, must deliver the air trapped between the rotors, thus building up a constantly increasing pressure until the relief valve blows off. If, therefore, little or no power be required for propelling the vehicle, power must still be supplied to the compressor, although its speed may be reduced, and a corresponding speed reduction will be imposed on the turbine, with consequent inefficiency.
Thus, although the efficiency of the axial kinetic compressor, in the small sizes, is somewhat lower than that of* the positive tyre, it permits of the maintenance of an
approximately constant speed with the power required for driving varying with the air delivery.
After leaving the compressor, the air is passed through the tubes of the heat interchanger, over the outer surfaces of which the hot exhaust gases flow. The temperature of the inlet air is thus increased by an amount which fails short of the optimum—the mean between inlet and exhaust temperatures.
Next we come to the adding of heat by fuel burning in the combustion chamber. This chamber consists of two concentrically arranged tubes of such size that a narrow annular space is formed between them. A proportion of the relatively cool air fnpm the compressor passes through this space, thereby maintaining the temperature of the inner, or flame, tube within reasonable bounds. The greatest proportion of the air passes into the flame tube, where fuel is being injezted in a continuous spray, thus supporting combustion. To wards the exit end of the flame tube, when the fuel has been consumed, the outer belt of cooling air is returned to the main stream and the whole mass directed into the first nozzle ring.
Turbine Blade Design The turbine blades are formed so that, at a designed gas speed, the machine will operate at maximum efficiency, and at any other speed the gas does not pass on to the blades in the desired direction and thus causes shock and loss of efficiency. The turbine, like the axial kinetic compressor, is a constant-speed machine. Mere control of the quantity of fuel injected is not enough, as a reduction must cause a fall in speed of the turbiae and, in consequence, a similar fall in compressor speed with reduced air pressure and a still further loss in efficiency. The only remedy, therefore, is to maintain the air speed but reduce the quantity in like ratio to the reduction in fuel admitted. This may be done only by blanking certain of the compressor, exhaust and the turbine inlet ports, by means of suitable valves.
By so doing, control of the output torque is obtained, but not of the speed. It would, therefore, be impossible directly to couple the road wheels to the output shaft of such a machine. The addition in the power line of an infinitely variable torque converter, even if an entirely satisfactory device of this nature were available, would not be practicable because precise control of road speed would he problematical.
Two schemes suggest themselves as being suitable for transmitting the power of the turbine to the road wheels. In the first, the whole power output of the gases would be expended in driving the turbine, which would be directly coupled to the compressor and to an electric generator.
he generater would absorb the power remaining after that required for air compression had been deducted. Electric motors, presumably either directly incorporated in, or geared to, the wheels, would receive the power from the generator and so drive the vehicle.
Control of such equipment would be provided by some similar apparatus to that employed on battery electrics. A governor control would be necessary to measure the current supply required by the motors, and to adjust the air-supply valves of the turbine in sympathy. The speed of the turbine equipment will remain approximately constant at all times.
The greatest objection to this otherwise admirable scheme is that the low efficiency of the turbine set—about 20 per cent.—is made worse in that the generator and motor losses must be added. It is, therefore, doubtful whether more than 13 per cent. or 14 per cent. overall efficiency could be obtained.
The second scheme would, once again, be based on a directly coupled turbine and compressor set, but the former. would be capable of delivering only sufficient power to drive the latter. The two, in combination, would, therefore, serve only in the capacity of exhaust-gas producers for the driving of a second turbine, which would provide the drive to the road wheels. A valve, coupled to the accelerator pedal, would vary the quantity of exhaust gas delivered to the output turbine and, once again, a suitable governor would maintain the gas-producer set at a sensibly constant speed, but would vary the gas quantity delivered to suit the requirements of the moment.
Methods of Control It would, of course, be possible to dispense with the governor and arrange for the gas delivery to be under the driver's control. In either case there would be some four or five stages of air-admission contrpl. They would give, in effect, five direct gas-quantity deliveries and modifications of quantity between these steps, effected by fueldelivery control. These two methods would, of course, be automatically adjusted, in combination, from the one pedal, and efficiency would vary slightly as the fuel control was modified.
Governor control of the gas-producer set would; however, be advantageous in that, by allowing the accelerator to close completely, the gas normally going to the output turbine could be passed straight to exhaust while the vehicle was standing for short periods, and by closing the by-pass valve a gradual start from rest could be effected.
With this dual-turbine arrangement, a higher efficiency would result than with electric drive when the output turbine was running at its designed speed, but this would fall off at speeds other than the optimum. The turbine drive is, however, somewhat disadvantageous in that, at zero speed, the torque is approximately double that of the normal-speed torque and, at approximately the designed speed, the torque is zero. Although this characteristic is, to a small extent, useful, it detracts from the efficiency. This point is easily demonstrated when it is remembered that, for optimum efficiency, the torque should vary directly and inversely as the change in speed. Thus, as with a gear train, double torque should be accompanied by a 50 per cent. speed reduction, as only thus will the output of work, in terms of horse-power, remain unchanged. With the turbine, however, ,a locked torque can produce no horsepower, as as no work is being done.
The starting process is simple and should require no more effort on the part of the driver than does a piston engine. German engineers have used a two-stroke petrol engine for this purpose, as was employed on some early types of oil engine in Britain. Electrical starting is, however, used in this country, and is, undoubtedly, most suitable for the project under discussion. The practice employed successfully on aircraft may well be followed, as the Bendix starter, designed to set in motion heavy reciprocating parts against compression pressure, would hardly be necessary.
Starting Technique In the case of the turbine, the starter motor would be engaged at a low rotor speed and then accelerated once engagement had been effected. Fuel pressure would then be built up to some 40 lb. per sq. in., when flow would be permitted to the burners. The rotor would be further accelerated and the fuel ignited. At this stage, the automatic starting process would be completed and the driver would take control, At first starting a period of some 2 minutes would probably be required for idling, in order gradually to increase the temperature of the machine.
A commercial vehicle, driven by a gas turbine, would presumably have its power unit mounted between the side members of the frame at about the midway position between the axles, after the manner of the modern Sentinel. The
power unit would probably be offset to permit the combustion chamber to be positioned alongside, with the heat interchanger arranged above the two.
The power unit itself would consist of an axial turbine pump having some eight or 10 stages, delivering air through the heat interchanger to the combustion chamber. The driving turbines might be a three or four-stage impulse reaction set, directly coupled to the compressor, and another similar unit coupled to the output shaft for propelling the vehicle. This second unit would receive gas from the compressor turbine and would exhaust through the heat interchanger to the atmosphere by means of the usual tail pipe.
There is little justification for the fear that a hot jet will blast anyone or anything that might be behind, as would be the case with jet propulsion. The maximum possible proportion of heat will have been extracted from the gas for propulsion purposes, and there should be little difference in exhaust temperature from that of a normal petrol engine. The only difference is likely to be that the quantity of exhaust for a given output will be six times as great, necessitating a tail pipe of an area proportionally larger.
An hydraulic torque converter will be required to transmit the power to the rear axle and to provide the necessary variation in propulsive force. One of the several hydrostatic converters now being developed would, no doubt, be an even better proposition in that the indications, are that the differential and final-drive gears may be omitted.
Should the future see the development of some method of obtaining a variable pitch of the turbine rotor blades, the positive compressor of the Lysholm type would be highly advantageous. Alternatively, an hydraulic torque converter of a new type, which can be produced in sufficiently compact form, may be used to couple the turbine and compressor, so that the former may run at constant speed and the latter adjust its delivery to suit the requirements of the moment.
The Brown Boveri concern has operated axial compressors with variable-pitch blades for research purposes, although such a scheme would certainly not be so advantageous as either of the foregoing. The attainment of an ideal arrangement of the several units will require ingenuity to obtain the minimum number of bends in the gas flow and to smooth out those which are imperative. This is necessary to obtain the lowest possible pressure drop, where such is ineffective in providing propulsive effort. A prognosis of this order is difficult enough when dealing with even accepted equipment, but, in the case of rotary power units, we may well see a complete breakaway from turbine practice as we know it at present.