• From the Orekiinq
Page 52
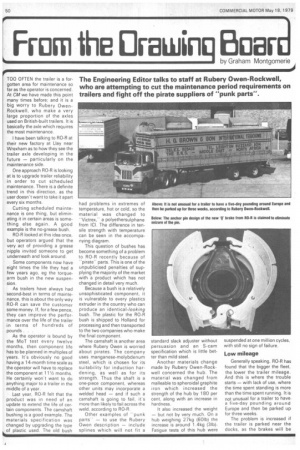
Page 53
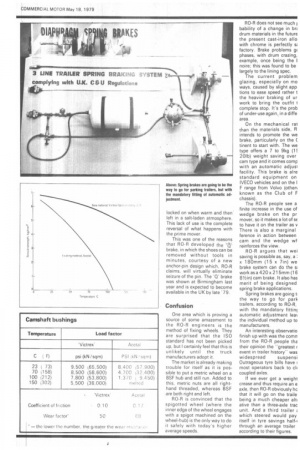
If you've noticed an error in this article please click here to report it so we can fix it.
Pr?,,,Psonee,
The Engineering Editor talks to staff at Rubery Owen-Rockwell, who are attempting to cut the maintenance period requirements on trailers and fight off the pirate suppliers of "punk parts".
TOO OFTEN the trailer is a forgotten area for maintenance so far as the operator is concerned. At CM we have made this point many times before; and it is a big worry to Rubery OwenROckwell, who make a very large proportion of the axles used on British-built trailers. It is basically the axle which requires the most maintenance.
I have been talking to RO-R at their new factory at Llay near Wrexham as to how they see the trailer axle developing in the future — particularly on the maintenance side.
One approach RO-R is looking at is to upgrade trailer reliability in order to cut scheduled maintenance. There is a definite trend in this direction, as the user doesn't want to take it apart every six months.
Cutting scheduled maintenance is one thing, but eliminating it in certain areas is something else again. A good example is the no-grease bush.
RO-R looked at this idea once, but operators argued that the very act of providing a grease nipple invited someone to get underneath and look around.
Some components now have eight times the life they had a few years ago, eg the torquearm bush in the new suspension.
As trailers have always had second-best in terms of maintenance, this is about the only way RO-R can save the customer some money. If, for a few pence, they can improve the performance over the life of the trailer in terms of hundreds of pounds.
As the operator is bound by the MoT test every twelve months, then component life has to be planned in multiples of years. It's obviously no good having a 14-month time scale as the operator will have to replace the component at 111/2 months. He certainly won't want to do anything major to a trailer in the middle of a year.
Last year, RO-R felt that the product was in need of an update to extend the life of certain components. The camshaft bushing is a good example. The materials specification was changed by upgrading the type of plastic used. The old bush had problems in extremes of temperature, hot or cold, so the material was changed to "Victrex," a polyethersulphane from id. The difference in tensile strength with temperature can be seen in the accompanying diagram.
This question of bushes has become something of a problem to R0-R recently because of
pirateparts. This is one of the unpublicised penalties of supplying the majority of the market with a product which has not changed in detail very much.
Because a bush is a relatively unsophisticated component, it is vulnerable to every plastics extruder in the country who can produce an identical-looking bush. The plastic for the RO-R bush is shipped to Holland for processing and then transported to the two companies who make the final component.
The camshaft is another area where Rubery Owen is worried about pirates. The company uses manganese-molybdenum steel, which is chosen for its suitability for induction hardening, as well as for its strength. Thus the shaft is a one-piece component, whereas other units may incorporate a welded head — and if such a camshaft is going to fail, it's more than likely to fail across the weld, according to RO-R.
Other examples of ''punk parts" — to use the Rubery Owen description — include splines which will not fit a standard slack adjuster without persuasion and an S-cam specification which is little better than mild steel.
Another materials change made by Rubery Owen-Rockwell concerned the hub. The material was changed from malleable to spheroidal graphite iron which increased the strength of the hub by 180 per cent, along with an increase in hardness.
It also increased the weight — but not by very much. On a hub weighing 27kg {60Ib) the increase is around 1.4kg (31b).. Fatigue tests of this hub were suspended at one million cycles, with still no sign of failure.
Low mileage
Generally speaking, RO-R has found that the bigger the fleet, the lower the trailer mileage. And this is where the trouble starts — with lack of use, where the time spent standing is more than the time spent running. It is not unusual for a trailer to have. a five-day pounding around Europe and then be parked up for three weeks.
The problem is increased if the trailer is parked near the docks, as the brakes will be locked on when warm and then• left in a salt-laden atmosphere. This lack of use is the complete reversal of what happens with the prime mover.
This was one of the reasons that R0-R developed the Ti' brake, in which the shoes can be removed without tools in minutes, courtesy of a new anchor-pin design which, R0-R claims, will virtually eliminate seizure of the pin. The 'Q' brake was shown at Birmingham last year and is expected to become available in the UK by late '79.
Confusion
One area which is proving a source of some amazement to the RO-R engineers is the method of fixing wheels. They are surprised that the ISO standard has not been picked up, but I certainly feel that this is unlikely until the truck manufacturers adopt it.
The market is already making trouble for itself as it is possible to put a metric wheel on a BSF hub and still run. Added to this, metric nuts are all righthand threaded, whereas BSF .are both right and left.
RO-R is convinced that the spigotted wheel (where the inner edge of the wheel engages with a spigot machined on the wheel-hub) is the only way to do it safely with today's higher average speeds.
R0-R does not see much I bability of a change in br: drum materials in the future the present cast-iron allo with chrome is perfectly si
factory. Brake problems gi phases, with drum crazing, example, once being the I noire; this was found to be largely to the lining spec.
The current problem glazing, especially on ma ways, caused by slight app tions to ease speed rather t the heavier braking of ur work to bring the outfit 1 complete stop. It's the prob of under-use again, in a diffe area.
On the mechanical rat than the materials side, R intends to promote the we brake, particularly on the ( tinent to start with. The we type offers a 7 to 9kg (1! 20Ib) weight saving over cam type and it comes comp with an automatic adjust facility. This brake is alre standard equipment on IVECO vehicles and on the I F range from Volvo (othen known as the Club of F chassis).
The RO-R people see a finite increase in the use of wedge brake on the pr mover, so it makes a lot of SE to have it on the trailer as v There is also a marginal ference in action between cam and the wedge wt reinforces the view.
RO-R argues that wei saving is possible as, say, a x 180mm (15 x 7in) we brake system can do the si work as a 420 x 215mm (16 81/2in) cam brake. It also has merit of being designed spring brake applications.
Spring brakes are going t the way to go for park trailers, according to RO-R, with the mandatory fittini automatic adjustment lea■ the individual method up to manufacturers,
An interesting observatio finish up with was the comn from the RO-R people the. their opinion the "greatest r event in trailer history" was
widespread suspensi Outrageous tyre bills have most operators back to cli coupled axles.
If we ever get a weight crease and thus require an e axle, then RO-R obviously hc that it will go on the traile being a much cheaper alt' ative than a three-axle trac unit. And a third trailer which steered would pay itself in tyre savings half-) through an average trailer according to their figures.