Newer Alloys Achieve Prominence
Page 30
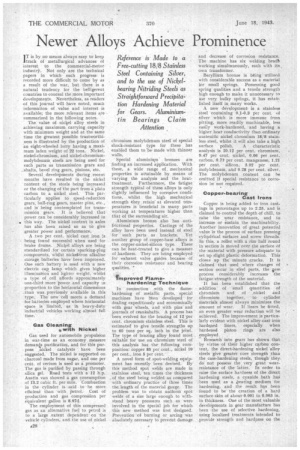
Page 33
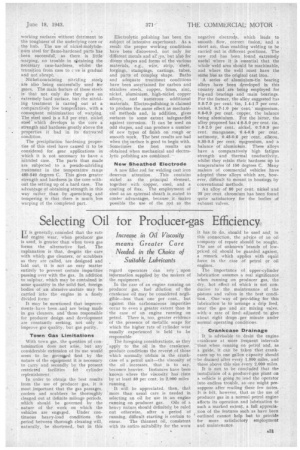
If you've noticed an error in this article please click here to report it so we can fix it.
Reference is Made to a Free-cutting 18/8 Stainless Steel Containing Silver, and to the use of Nickelbearing Nitriding Steels as Straightforward Precipitation Hardening Material for Gears. Aluminiumtin Bearings Claim
Attention
IT is by no means always easy to keep track of metallurgical advances of interest to the commercial-motor. inclustrY. Not only are the technical papers in which such progress is recorded more difficult to come by as a result of the war, but there is a natural tendency for the belligerent countries to conceal the more important. developments. Nevertheless, as readers of this journal will have noted, much information of value and interest is available; the more relevant items are . summarized in the following notes.
The value of nickel alloy steels in achieving maximum carrying capacity' with minimum weight and at the same time the greatest possible trustworthiness is illustrated by the production of an eight-wheeled lorry having a maximum laden weight of 22 tons. Nickel, nickel-chromium, and nickel-chromiummolybdenum steels .are being used for such parts as transmission gears and shafts, bevel ring gears, pinions, etc.
Several developments during recent months have resulted in the nickel content of the steels being increased or the changing of the part from a plain carbon to a nickel steel. This particularly applies to speed-reduction gears, bull-ring gears, master pins, etc., and is being contemplated for trans..mission gears. It is believed that power can be considerably increased in this .way. The nickel content in axles has also been raised so as to give greater power and performance.
A two per cent. nickel cast iron is being found successful when used for brake drums. NiclFel alloyS are being standardized for certain sparking-plug components, whilst nickel-iron alkaline storage, batteries have been improved. One such battery is used with a new electric call lamp which gives higher illumination and lighter weight, whilst • a type of cell affords approximately one-third more power and capacity In proportion to the horizontal dimensions than was previously available in this type. The new cell meets a demand for batteries employed where horizontal space is limited, as its heavy-duty industrial vehicles working almost full time.
Gas Cleaning
*with Nickel
Gas used for automobile propulsion in War-time as an economy measure demanis purification, and for this purpose ,nickel catalysts have been suggested. The nickel is supported on charcoal made from sugar, and one per cent. of cerium is used as a promoter. The gas is purified by passing through silica gel. Road tests with a 12 h.p. Austin van showed a gas consumption of 13.2 cubic ft. per mile. Combustion in the cylinder is said to be more efficient than with petrol. Cost of production and gas compression per equivalent gallon is 8,97d.
The employment of this compressed gas as an alternative fuel to petrol is to a large .extent dependent on the vehicle cylinders; and the use of nickel chromium moly1xleitum steel of special shock-resistant type for these has enabled them to 'be' made with thinner walls.
Special aluminiwnbronzes are finding an increased application. With these, a wide range of. mechanical properties is attainable by means of varying the analysis and the heattreatment Furthermore, the fatigue strength typical of these alloys is only slightly influenced by corrosive conditions, whilst the high mechanical strength ,they retain' at elevated temperatures is beneficial in many parts working at temperatures higher than that of the surrounding air.
Aluminium bronze also has antifrictional properties. Castings of the alloy have been used instead of steel for such parts as brackets. Yet another group of copper-base alloys is the copper-nickel-silicon type. These can be heat-treated to give a measure of hardness. They are being employed for exhaust valve guides because of their corrosion resistance and. bearing qualities. ` • Improved Flame hardening Technique
In connection with the flamehardening of metallic parts, special machines have been developed for dealing expeditiously and economically with gear wheels, and with pins. and journals of etrankshafts. A process has been evolved for the brazing of 12 per cent, chromium stainless steel. This is estimated to give tensile strengths up to 60 tons per sq. inch in the joint. The type of brazing alloy found most suitable for use on chromium steel of this analysis has the following composition: copper 85 per cent., nickel 10 per cent., iron 5 per cent.
A novel form of spot-welding equipment has recently been devised. By this method spot welds are made in stainless steel, ten times the thickness . of the steel being welded as compared with ordinary practice of three times the, length of the material gauge. The problem was to obtain uniform spot welds of a size large enough to withstand heavy pressures such as were involved in the Special job for which -this new method was first designed. Prevention of burning or arcing 'Was absolutely necessary to prevent damage
and decrease of corrosion resistance. The machine has six welding head% working simultaneously, each with its., own transformer.
Beryllium bronze is bting utilized with considerable success as a material for small springs. Possessing good spring qualities and a tensile strength high enough to make it unnecessary lo Lise very bulky springs, it has established itself in many works.
A new development is a stainless steel containing 0,1-0.3 per cent. of silver which is more immune from pitting, more readily machinable, less easily work-hardened, and having a higher heat conductivity than ordinary austenitic nickel chromium 18/8 stainless steel, whilst it will also.take a high surface polish. A characteristic analysis is 20.12 per cent. chromium, 9.47 per cent. nickel, 0.06 per cent. carbon, 0.7/ per cent. manganese, 1.21 per gent. silicon; 3.02 • per cent. molybdenum, and 0.28 per cent. silver. The molybdenum content can he omitted if special resistance to corrosion be not required.
Copper-bearing Cast Irons Copper is being added to iron Castings in percentages up to 2.25, and is claimed to control the depth of chill, to raise the wear resistance, and to increase or sustain the machinability. Another innovation of great potential value Is the process of surface pressing cylindrical surfaces and screw threads. In this, a roller with a rim half round in section is moved over the surface of the material with pressure adequate to set up slight plastic deformation. This closes up the minute ,cracks, It is claimed that used where changes of section occur in steel parts, the few. process considerably increases the fatigue strength of the material.
It has . been established that the addition of small quantities of chromium and of • .nickel and criromium together, to • cylinder Materials almost always minimizes the amount of wear. If liners be fitted, an even greater wear reduction will he achieved. The improvement is particularly evident with nickel alloy cast iron hardened liners, especially When hardened piston rings are also employed. • Research into gears has shown that by virttie of their higher carbon content, the direct-hardening nickel alloy steels give greater tore strength than the case-hardening steels, though they do not possess the very great wearresistance of the latter. In order to raise the surface hardness of the direct hardening steels, a cyanide bath has been used as a ,eating medium, for hardening, and the result has been found to be the creation of a bard surface skin of about 0.001 to 0.003 in. in thickness. One of the most valuable develOpments in gear manufacture has been the use of selective hardening, using localized treatments intended to• provide strength and hardness on the working surface.; without detriment to the toughness of the underlying core or the hub, The use of nickel:molybdenum steel for flame-hardened parts has been successful, as there is little warping, no trouble in obtaining the necessary case-hardness, whilst the transition from case to r ere is gradual and not abrupt,
Nickel-containing nitriding steels are also being successfully used or gears. The main feature of these steels is that not only do they give an extremely hard surface, but the nitriding treatment is carriel out at a comparatively low temperature, with a consequent minimization of warping. The steel used is a 3.5 per cent. niCkel. steel which develops in the core a strength and hardness greatly above the properties it had in its nntreak.ed condition.
The precipitation hardening properties of this steel have caused it to be considered for gear applications in which it is not necessary to have a intrided case.. The parts thus made are subjected to a pseudo-nitriding treatment in the temperature range 480-540 degrees C. This gives greater strength and hardness in the core without the setting up of a hard case. The advantage of obtaining strength in this way rather than by quenching and tempering is that there is much less warping of the completed part.
Electrolytic polishing has been the subject of intensive experiment. As a result the proper working conditions have been discovered, not only for different metals and al Jys," but also for divers shapes and fords of the various materials, e.g., wire, strip, sheet, forgings, stampings, Castings, tubes, and parts of comple* shape. Baths and adequate treatment conditions have been ascertained for carbon and stainless steels, copper, brass, zinc, nickel, aluminium, high-nickel copper alloys, and numerous additional materials, Electro-polishing is claimed to produce the ,same effect as mechanical methods and, in addition, gives surfaces to some extent Safeguarded against corrosion. It can be used on odd shapes, and can produce a number of new types of finish on rough or smooth work. The best results are had when the surface is good to begin with.
• Sometimes the best results are obtained when mechanical and electrolytic polishing are combined.
New Sheathed Electrode
A new filler rod for welding cast iron deserves attention. This contains nickel as the principal element, together with copper, steel, and a coating of flux. The employment of steel as an external sheath is stated to confer advantages, because it makes possible the use of the rod as the
negative electrode, which leads to smooth flow, correct fusion; and a short arc, thus enabling welding to be carried out in different positions. The new rod has been found extremely useful where it is essential that the whole weld area should be machinable, and where the weld must have the same hue as the original cast iron.
A series of aluminium-tin bearing alloys have been developed in this country and are being employed for big-end bearings and main bearings. For the former, the alloy suggested has 5.5-7,0 per cent. tin, 1.4-1.7 per cent. nickel, 0.7-1,0 per cent" magnesium, 0.6-0.9 per cent, copper, the balance being aluminium. For the latter, the alloy proposed has 4.6-5.0 per cent. tin, 1.6-2.0 per cent. nickel, 0.7-0.9 per cent. manganese, 0.4-0,8 per cent. antimony, 0.45-0.6 per cent. .silicon, 0.95-0.5 per cent. magnesium, and a balance of aluminium. These alloys have a comparatively high fatigue strength and thermal conductivity, whilst they retain their hardness up to temperatures of 150 degrees C. Many makers of commercial vehicles have adopted these alloys which are, however, difficult to mount in housings by conventional methods.
An alloy of 80 per cent, nickel and 20 per cent_ chromium has been found quite satisfactory for the bodies of exhaust valves.